The Physical Vapor Deposition (PVD) process on metal involves the physical vaporization of materials in a vacuum environment, which are then deposited onto a substrate to form a thin film. Unlike Chemical Vapor Deposition (CVD), which relies on chemical reactions, PVD uses physical processes such as sputtering or evaporation to transfer material from a solid source to the substrate. PVD is particularly advantageous for depositing a wide range of materials, including metals, alloys, and ceramics, and is performed at relatively lower temperatures compared to CVD. The process results in less dense and less uniform coatings but is faster and more versatile in terms of material compatibility. PVD is widely used in applications requiring durable, wear-resistant, and corrosion-resistant coatings, such as in the aerospace, automotive, and tooling industries.
Key Points Explained:
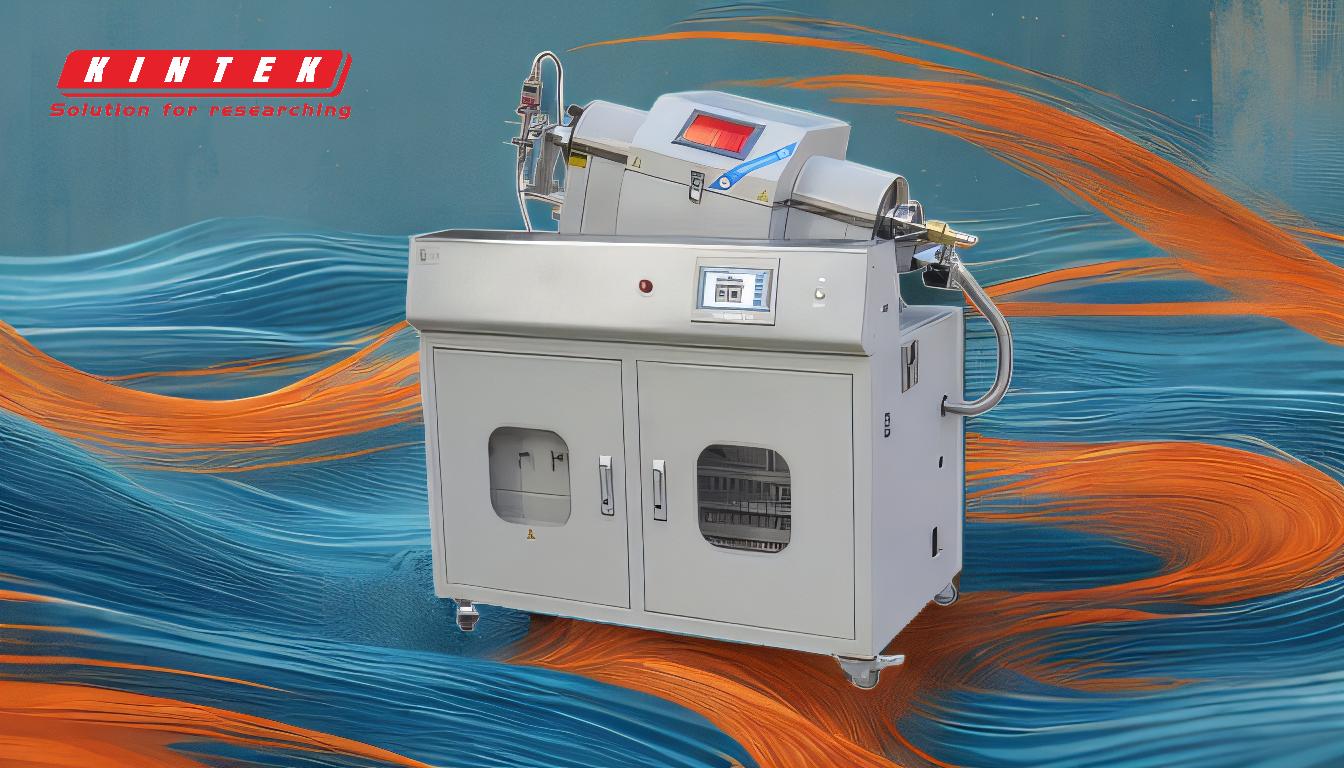
-
Definition and Mechanism of PVD:
- PVD is a process where materials are physically vaporized in a vacuum and then deposited onto a substrate to form a thin film. This is achieved through methods like sputtering or evaporation, where the material is ejected from a solid source and condenses on the substrate.
- Unlike CVD, which involves chemical reactions between gaseous precursors and the substrate, PVD is a purely physical process, making it suitable for a broader range of materials, including metals, alloys, and ceramics.
-
Operating Conditions:
- PVD is typically performed in a vacuum environment, which minimizes contamination and allows for better control over the deposition process.
- The process occurs at relatively lower temperatures (250°C to 450°C) compared to CVD (450°C to 1050°C), making it more suitable for temperature-sensitive substrates.
-
Coating Characteristics:
- PVD coatings are generally less dense and less uniform than CVD coatings. This is due to the line-of-sight nature of the deposition process, where material is deposited directly onto the substrate without chemical interaction.
- However, PVD coatings are faster to apply and can be tailored to achieve specific properties such as hardness, wear resistance, and corrosion resistance.
-
Material Compatibility:
- PVD can deposit a wide range of materials, including metals, alloys, and ceramics. This versatility makes it suitable for various industrial applications where different material properties are required.
- In contrast, CVD is typically limited to ceramics and polymers, which may not be suitable for all applications.
-
Applications:
- PVD is widely used in industries that require durable, wear-resistant, and corrosion-resistant coatings. For example, it is commonly used in the aerospace and automotive industries for coating engine components, cutting tools, and other critical parts.
- The ability to deposit a broad range of materials and the relatively lower operating temperatures make PVD a preferred choice for many applications where CVD may not be feasible.
-
Comparison with CVD:
- The key difference between PVD and CVD lies in the nature of the deposition process. PVD involves physical vaporization and deposition, while CVD relies on chemical reactions between gaseous precursors and the substrate.
- PVD is a line-of-sight process, meaning that the material is deposited directly onto the substrate without chemical interaction, whereas CVD involves multidirectional deposition where chemical reactions occur on the substrate surface.
-
Role of Plasma in Deposition:
- Plasma can enhance the deposition process by providing energy to activate the source gas or vapor, leading to the formation of electrons, ions, and neutral radicals. This activation allows for the dissociation and condensation of the gas or vapor on the substrate surface, enabling the deposition of coatings at lower temperatures.
- This process, known as microwave plasma chemical vapor deposition, can expand the range of possible substrates and coating materials, making it a valuable technique in both PVD and CVD processes.
In summary, the PVD process on metal is a versatile and efficient method for depositing thin films with specific properties. Its ability to work with a wide range of materials, operate at lower temperatures, and produce coatings quickly makes it a preferred choice for many industrial applications. While it may not offer the same level of density and uniformity as CVD, its advantages in terms of material compatibility and processing speed make it an essential technique in modern manufacturing.
Summary Table:
Aspect | PVD Process |
---|---|
Mechanism | Physical vaporization in a vacuum (sputtering or evaporation) |
Operating Temperature | 250°C to 450°C (lower than CVD) |
Coating Characteristics | Less dense, less uniform, but faster and versatile |
Material Compatibility | Metals, alloys, ceramics (broader range than CVD) |
Applications | Aerospace, automotive, tooling (durable, wear-resistant, corrosion-resistant coatings) |
Key Advantage | Lower temperature, faster processing, and material versatility |
Discover how the PVD process can enhance your metal coatings—contact our experts today for a tailored solution!