Quenching is a critical heat treatment process where metals are rapidly cooled to achieve specific mechanical properties. Typically, quenching is followed by tempering, which involves reheating the metal to a lower temperature to reduce brittleness and improve toughness. This combination of quenching and tempering ensures that the metal gains both hardness and durability, making it suitable for demanding applications like aerospace and automotive industries. The process involves precise temperature control and cooling methods, such as oil, water, or nitrogen quenching, depending on the material and desired outcome.
Key Points Explained:
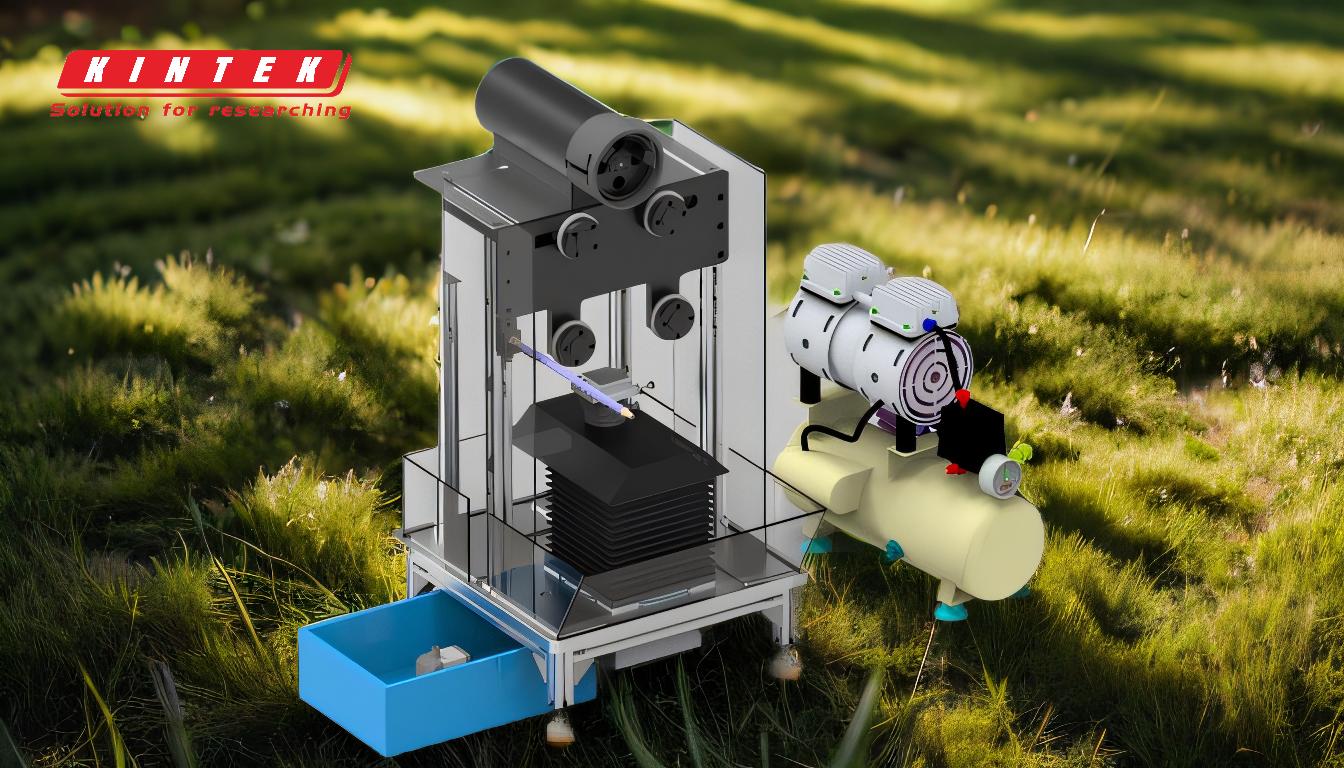
-
Quenching Process Overview:
- Quenching involves heating metal to a high temperature and then rapidly cooling it using mediums like water, oil, or nitrogen. This rapid cooling locks the metal's microstructure, enhancing hardness and strength.
- The process is essential for achieving specific mechanical properties, such as increased hardness and wear resistance.
-
Purpose of Quenching:
- The primary goal of quenching is to transform the metal's microstructure into a hardened state. This is particularly important for materials like medium carbon alloy steel, which require high strength for industrial applications.
- Quenching fixes the metal's structure in a solidified state, preventing undesirable phase transformations.
-
Common Quenching Methods:
- Oil Quenching: Often used for medium carbon alloy steels, oil provides a controlled cooling rate that minimizes distortion and cracking.
- Water Quenching: Faster cooling than oil, suitable for materials requiring extreme hardness but with a higher risk of cracking.
- Nitrogen Quenching: Used in aerospace applications for precise cooling and minimal oxidation.
- Air Quenching: Slower cooling rate, suitable for materials that are less prone to cracking.
-
Quenching Followed by Tempering:
- After quenching, metals are often too brittle for practical use. Tempering is the next step, where the metal is reheated to a lower temperature (below the critical point) and then cooled slowly.
- Tempering reduces internal stresses and brittleness while maintaining hardness. This balance is crucial for applications requiring both strength and toughness.
-
Quench and Temper Process:
- This two-step process involves:
- Heating the metal above its transformation range.
- Rapidly cooling it (quenching) to room temperature, typically using oil.
- Reheating to a lower temperature (tempering) to achieve the desired hardness and toughness.
- The quench and temper process is widely used for medium carbon alloy steels, enhancing their strength and durability.
- This two-step process involves:
-
Applications of Quenching and Tempering:
- Aerospace: Components like landing gear and engine parts require high strength and resistance to fatigue.
- Automotive: Critical parts such as gears, shafts, and suspension components benefit from the enhanced mechanical properties.
- Industrial Machinery: Tools and dies that undergo high stress and wear are often quenched and tempered.
-
Importance of Cooling Rate:
- The cooling rate during quenching significantly affects the final properties of the metal. Too rapid cooling can cause cracking, while too slow cooling may not achieve the desired hardness.
- Selecting the appropriate quenching medium (oil, water, nitrogen, etc.) is crucial for balancing hardness and structural integrity.
-
Challenges in Quenching:
- Distortion and Cracking: Rapid cooling can lead to internal stresses, causing warping or cracking. Proper tempering helps mitigate these issues.
- Material Selection: Not all metals respond well to quenching. For example, some alloys may require specific cooling rates or post-quench treatments.
-
Future Trends in Quenching:
- Advances in quenching technologies, such as high-pressure gas quenching, are improving precision and reducing environmental impact.
- Automation and digital monitoring are enhancing process control, ensuring consistent results in industrial applications.
By understanding the quenching process and its subsequent tempering step, manufacturers can optimize the mechanical properties of metals for various high-performance applications. This combination ensures a balance between hardness, strength, and toughness, making it indispensable in modern engineering and manufacturing.
Summary Table:
Step | Description |
---|---|
Quenching | Rapidly cools metal to lock its microstructure, increasing hardness and strength. |
Tempering | Reheats metal to a lower temperature to reduce brittleness and improve toughness. |
Applications | Aerospace, automotive, and industrial machinery for high-strength components. |
Cooling Methods | Oil, water, nitrogen, or air, depending on material and desired outcome. |
Optimize your metal heat treatment process—contact our experts today for tailored solutions!