RF sputtering is a technique used to deposit thin films of non-conductive (dielectric) materials onto substrates. Unlike DC sputtering, which is effective for conductive materials, RF sputtering uses an alternating current (AC) power source at a specific radio frequency, typically 13.56 MHz. This frequency is chosen because it avoids interference with communication frequencies and ensures efficient ion bombardment of the target material. The alternating electrical potential prevents charge buildup on insulating targets, allowing continuous sputtering. The process involves creating a plasma in a vacuum chamber filled with inert gas (usually Argon), ionizing the gas, and bombarding the target material to eject atoms that deposit as a thin film on the substrate.
Key Points Explained:
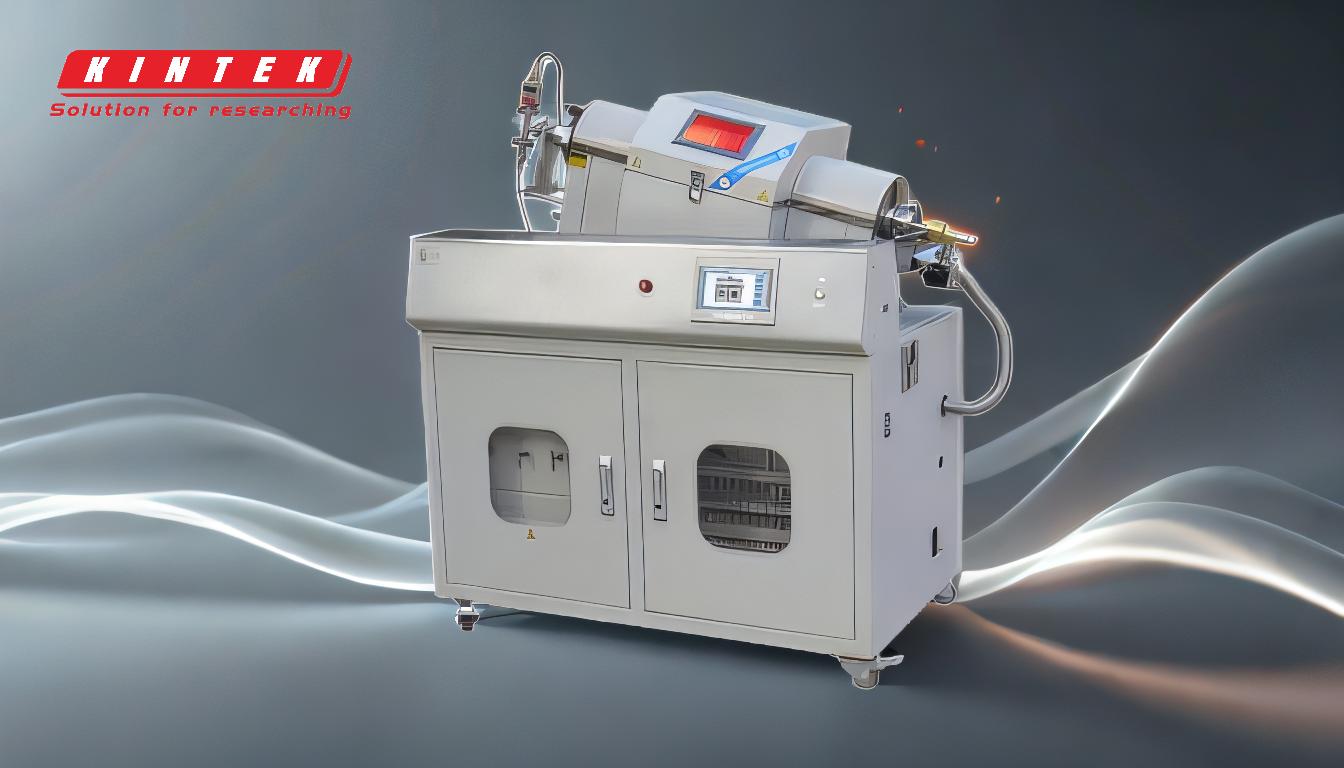
-
RF Sputtering Overview:
- RF sputtering is a method for depositing thin films of non-conductive (dielectric) materials.
- It overcomes the limitations of DC sputtering, which is unsuitable for insulating materials due to surface charging.
-
Frequency Used in RF Sputtering:
- The standard frequency used in RF sputtering is 13.56 MHz.
- This frequency is chosen because it is within the industrial, scientific, and medical (ISM) radio band, ensuring it does not interfere with communication frequencies.
-
Why 13.56 MHz?:
- 13.56 MHz is a globally accepted frequency for industrial applications, including RF sputtering.
- It allows efficient energy transfer to the plasma while minimizing energy losses and interference.
-
Mechanism of RF Sputtering:
- RF sputtering uses an AC power source, which alternates between positive and negative cycles.
- During the positive cycle, electrons are attracted to the target, creating a negative bias.
- During the negative cycle, ion bombardment of the target continues, ejecting atoms that deposit on the substrate.
-
Preventing Charge Buildup:
- Insulating materials cannot dissipate charge, leading to surface charging in DC sputtering.
- RF sputtering alternates the electrical potential, preventing charge buildup and enabling continuous sputtering.
-
Role of Plasma and Inert Gas:
- The process begins by introducing an inert gas (typically Argon) into a vacuum chamber.
- A negative charge applied to the target material creates a plasma, ionizing the Argon atoms.
- These ions bombard the target, ejecting atoms that form a thin film on the substrate.
-
Advantages of RF Sputtering:
- Suitable for depositing a wide range of materials, including insulators, semiconductors, and metals.
- Provides better control over film thickness and uniformity compared to other deposition methods.
- Enables the deposition of high-quality thin films with minimal defects.
-
Applications of RF Sputtering:
- Used in the fabrication of microelectronics, optical coatings, and solar cells.
- Essential for depositing dielectric layers in semiconductor devices and thin-film transistors.
By using RF sputtering at 13.56 MHz, manufacturers can effectively deposit thin films of insulating materials, ensuring high-quality and uniform coatings for various applications. This frequency is critical for maintaining process efficiency and avoiding interference with other systems.
Summary Table:
Key Aspect | Details |
---|---|
RF Frequency | 13.56 MHz |
Purpose | Deposits thin films of non-conductive (dielectric) materials |
Why 13.56 MHz? | Avoids interference, ensures efficient energy transfer, and minimizes losses |
Mechanism | Alternating current (AC) prevents charge buildup on insulating targets |
Role of Plasma | Ionizes inert gas (Argon) to bombard the target material |
Advantages | Uniform film thickness, high-quality coatings, minimal defects |
Applications | Microelectronics, optical coatings, solar cells, and semiconductor devices |
Ready to achieve high-quality thin film deposition? Contact our experts today to learn more about RF sputtering solutions!