Sintering is a critical process in engineering and materials science, used to increase the density and strength of materials by heating them to temperatures just below their melting point. This process involves the compaction and bonding of powdered materials into a solid mass through the application of heat and pressure. The sintering process is widely used in industries such as powder metallurgy, ceramics, and electronics to produce high-density, durable, and functional components. Below, we break down the key aspects of sintering, its stages, and its applications.
Key Points Explained:
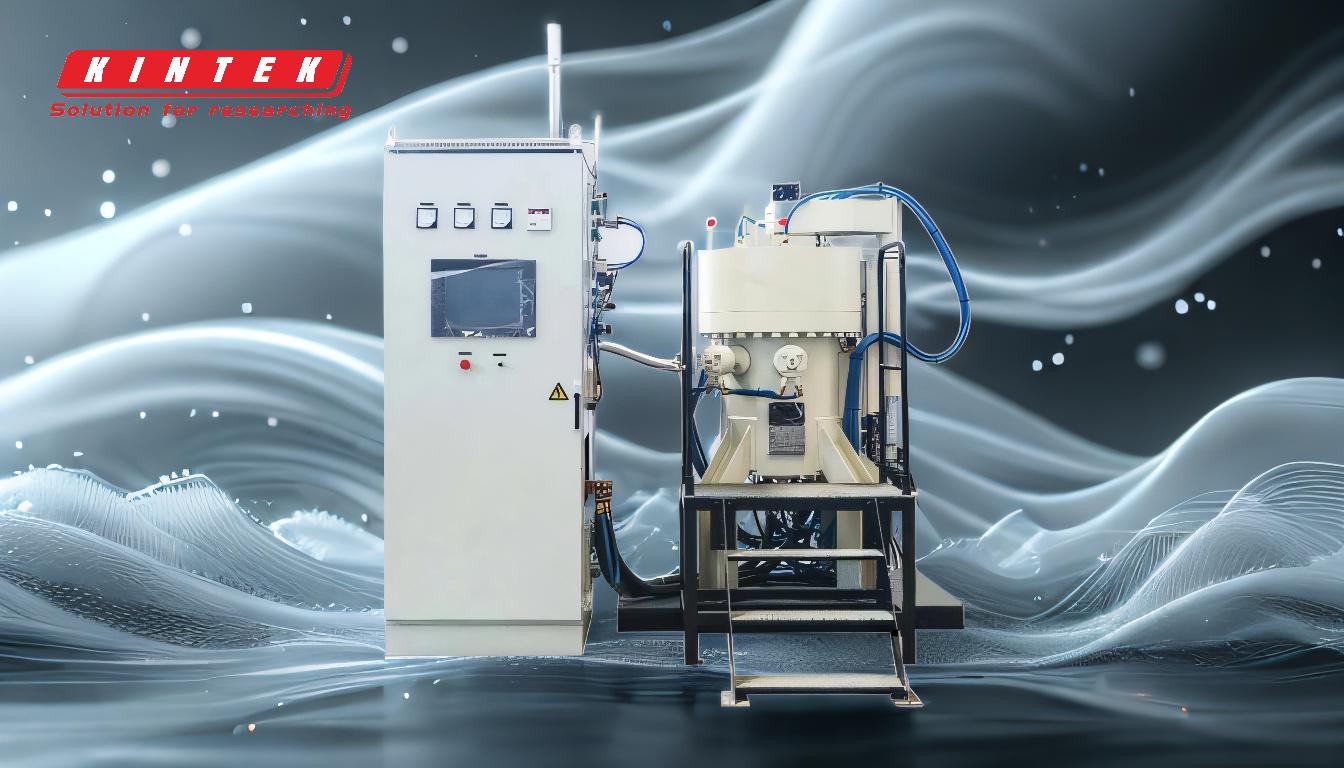
-
Definition and Purpose of Sintering:
- Sintering is a thermal process that consolidates powdered materials into a dense, solid structure without melting them completely. The primary goal is to enhance the material's density, strength, and durability by facilitating atomic diffusion and particle bonding.
-
Stages of the Sintering Process:
- Powder Preparation: The raw material is processed into fine powder, which is then shaped into the desired form, often using pressing tools or 3D printing techniques.
- Compaction: The powder is compacted under high pressure to form a green body, which is a loosely bonded structure with minimal voids.
- Heating: The compacted material is heated in a controlled environment, typically in a sintering furnace, to a temperature just below its melting point. This stage activates particle diffusion and bonding.
- Particle Merging and Densification: During heating, particles form necks and merge, reducing porosity and increasing density. Liquid phase sintering (LPS) can be used to accelerate this process.
- Cooling and Solidification: The material is cooled, allowing it to solidify into a cohesive, rigid structure with improved mechanical properties.
-
Applications of Sintering:
- Powder Metallurgy: Sintering is widely used to produce metal components, such as gears, bearings, and automotive parts, with high strength and precision.
- Ceramics Manufacturing: It is essential for creating dense ceramic materials used in capacitors, varistors, thermistors, and other electronic components.
- Electrical and Electronic Components: Sintering is employed in the fabrication of electrical contacts, semiconductor packaging, and circuit board components, ensuring high conductivity and durability.
-
Key Factors Influencing Sintering:
- Temperature: The sintering temperature must be carefully controlled to ensure particle bonding without causing complete melting.
- Pressure: Compaction pressure determines the initial density of the green body and influences the final product's density.
- Material Composition: The addition of binders, lubricants, or alloying elements (e.g., copper powder) can enhance the sintering process and improve material properties.
-
Advantages of Sintering:
- Produces materials with high density, strength, and durability.
- Enables the creation of complex shapes and intricate designs.
- Reduces material waste and energy consumption compared to traditional melting processes.
-
Challenges in Sintering:
- Controlling shrinkage and dimensional accuracy during heating and cooling.
- Ensuring uniform particle bonding and density throughout the material.
- Managing the removal of binders and lubricants to prevent defects.
By understanding the sintering process and its stages, engineers and manufacturers can optimize material properties and produce high-quality components for various applications.
Summary Table:
Aspect | Details |
---|---|
Definition | Thermal process consolidating powdered materials into dense, solid structures. |
Stages | Powder Preparation, Compaction, Heating, Particle Merging, Cooling. |
Applications | Powder Metallurgy, Ceramics, Electronics. |
Key Factors | Temperature, Pressure, Material Composition. |
Advantages | High density, strength, durability; complex shapes; reduced waste. |
Challenges | Shrinkage control, uniform bonding, binder removal. |
Discover how sintering can optimize your material production—contact our experts today!