Chemical vapor deposition (CVD) is a widely used method for synthesizing carbon nanotubes (CNTs), offering structural controllability, cost-effectiveness, and scalability. The process involves the decomposition of carbon-containing gases on a substrate, often aided by a metal catalyst, to form CNTs at relatively lower temperatures compared to other methods like laser ablation or arc discharge. CVD is the dominant commercial process for CNT production due to its ability to produce high-quality nanotubes with minimal environmental impact. The process can be further enhanced using techniques like plasma-enhanced CVD (PECVD), which reduces energy consumption and deposition temperatures.
Key Points Explained:
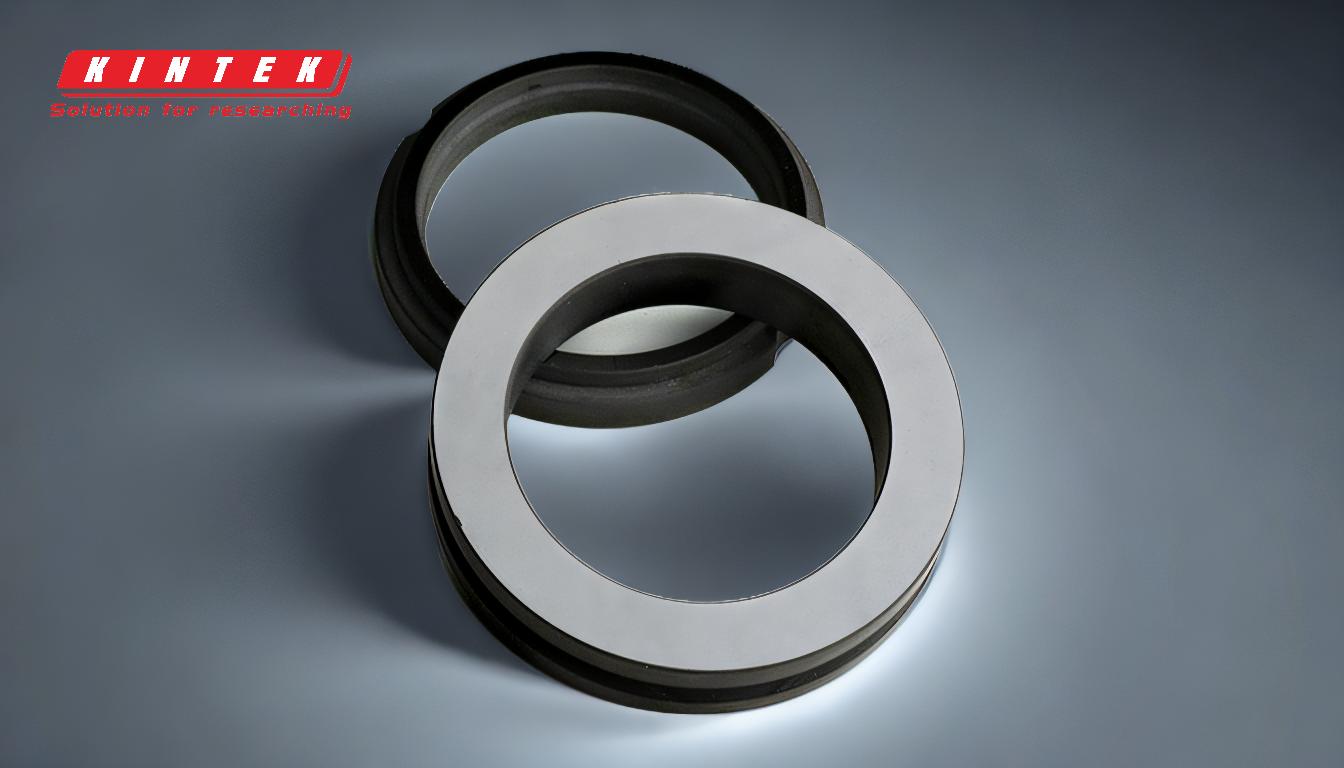
-
Overview of CVD Process:
- CVD involves exposing a substrate to volatile precursors in vapor form, which react or decompose on the substrate surface to form a solid deposit.
- For CNT synthesis, carbon-containing gases like methane or ethylene are introduced into a reactor, where they decompose on a catalyst-coated substrate.
-
Role of Catalysts:
- Catalytic CVD (CCVD) is the most common method for CNT synthesis. A metal catalyst (e.g., iron, nickel, or cobalt) is used to lower the reaction temperature and facilitate the decomposition of carbon precursors.
- The catalyst nanoparticles act as nucleation sites for CNT growth, enabling precise control over the nanotube structure.
-
Steps in CNT Synthesis via CVD:
- Preparation of Substrate and Catalyst: The substrate is coated with a thin layer of catalyst nanoparticles.
- Introduction of Carbon Precursor: Carbon-containing gases are introduced into the reactor.
- Thermal Decomposition: The gases decompose at elevated temperatures (typically 500–1000°C) on the catalyst surface.
- CNT Growth: Carbon atoms diffuse through or around the catalyst particles, forming nanotubes.
- Cooling and Collection: The reactor is cooled, and the CNTs are collected from the substrate.
-
Advantages of CVD for CNT Synthesis:
- Structural Control: CVD allows for precise control over CNT diameter, length, and chirality by adjusting parameters like temperature, gas flow rate, and catalyst type.
- Scalability: The process is easily scalable for industrial production.
- Cost-Effectiveness: Compared to other methods, CVD is more economical and energy-efficient.
-
Environmental Considerations:
- CVD is designed to minimize environmental impact by reducing material and energy consumption.
- Emerging methods focus on using green or waste feedstocks, such as carbon dioxide captured by electrolysis or methane pyrolysis, to further enhance sustainability.
-
Plasma-Enhanced CVD (PECVD):
- PECVD uses plasma to excite the precursor gases, enabling CNT growth at lower temperatures and with reduced energy consumption.
- This method is particularly useful for applications requiring low-temperature processing, such as flexible electronics.
-
Comparison with Other Methods:
- Laser Ablation and Arc Discharge: These methods are less controllable and more energy-intensive compared to CVD.
- CVD Dominance: CVD is the preferred method for commercial CNT production due to its superior controllability and scalability.
-
Future Trends:
- Research is ongoing to optimize CVD processes for even greater efficiency and sustainability.
- Innovations include the use of alternative feedstocks and advanced reactor designs to further reduce costs and environmental impact.
By understanding these key aspects, purchasers and researchers can make informed decisions about the synthesis of carbon nanotubes using CVD, ensuring high-quality production while minimizing environmental and economic costs.
Summary Table:
Aspect | Details |
---|---|
Process Overview | Decomposition of carbon-containing gases on a catalyst-coated substrate. |
Catalyst Role | Metal catalysts (e.g., iron, nickel) lower reaction temperature and enable growth. |
Key Steps | Substrate preparation, gas introduction, thermal decomposition, CNT growth. |
Advantages | Structural control, scalability, cost-effectiveness, and energy efficiency. |
Environmental Impact | Minimized material/energy use; green feedstocks enhance sustainability. |
PECVD Benefits | Lower temperatures, reduced energy consumption, ideal for flexible electronics. |
Comparison | CVD outperforms laser ablation and arc discharge in controllability and scalability. |
Future Trends | Optimization for sustainability, alternative feedstocks, advanced reactor designs. |
Interested in high-quality carbon nanotube synthesis? Contact our experts today to learn more!