Activated carbon regeneration typically involves heating the material to high temperatures to remove adsorbed contaminants and restore its adsorption capacity. The temperature range for regeneration depends on the method used, with catalytic regeneration being one of the common approaches. Based on the provided reference, catalytic regeneration occurs between two key temperature ranges: Tp (220–240 °C) and Tc (320–370 °C). These temperatures are critical for ensuring effective removal of contaminants without damaging the carbon structure.
Key Points Explained:
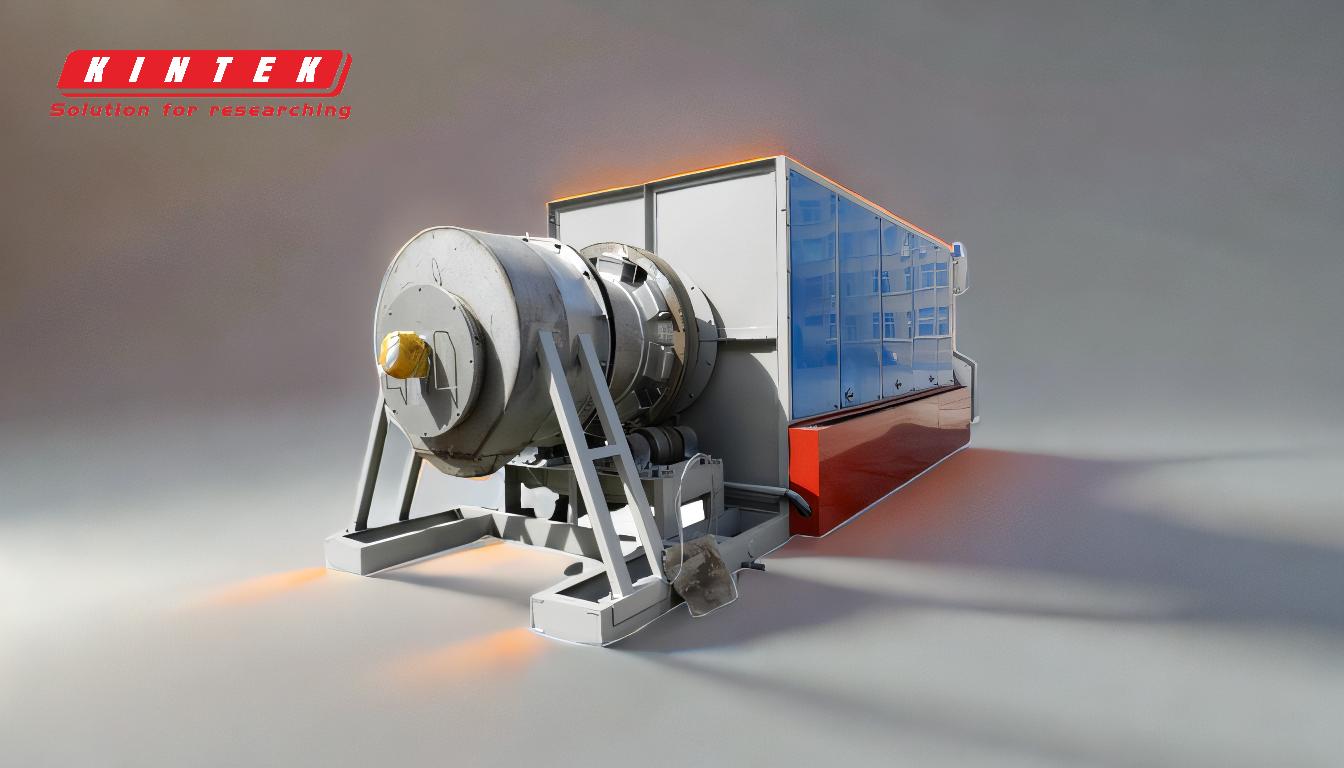
-
Temperature Ranges for Catalytic Regeneration:
- Tp (220–240 °C): This is the initial temperature range where the regeneration process begins. At this stage, lighter and more volatile contaminants start to desorb from the activated carbon.
- Tc (320–370 °C): This is the higher temperature range where more stubborn and heavier contaminants are removed. The higher temperature ensures complete regeneration of the activated carbon.
-
Importance of Temperature Control:
- Avoiding Carbon Degradation: Temperatures above 400 °C can lead to the degradation of the activated carbon structure, reducing its adsorption capacity. Therefore, staying within the specified ranges is crucial.
- Efficient Contaminant Removal: The two-stage temperature process ensures that both light and heavy contaminants are effectively removed, restoring the carbon's adsorption properties.
-
Catalytic Regeneration Process:
- Catalyst Role: The presence of a catalyst helps lower the activation energy required for desorption, making the process more energy-efficient.
- Controlled Heating: The process involves controlled heating to ensure that the carbon is not exposed to temperatures that could cause structural damage.
-
Applications and Considerations:
- Industrial Use: This method is commonly used in industries where activated carbon is used for air and water purification.
- Energy Efficiency: Catalytic regeneration is preferred in many applications due to its lower energy requirements compared to thermal regeneration, which often requires higher temperatures.
-
Comparison with Other Regeneration Methods:
- Thermal Regeneration: Typically requires temperatures above 500 °C, which can be more energy-intensive and risk damaging the carbon.
- Chemical Regeneration: Involves the use of chemicals to desorb contaminants, which can be less effective for certain types of contaminants and may introduce additional waste.
By understanding these key points, a purchaser can make informed decisions about the regeneration process for activated carbon, ensuring optimal performance and longevity of the material.
Summary Table:
Temperature Range | Purpose | Key Benefit |
---|---|---|
Tp (220–240°C) | Initial desorption of lighter contaminants | Efficient removal of volatile impurities |
Tc (320–370°C) | Removal of heavier contaminants | Complete regeneration of adsorption capacity |
Above 400°C | Avoid | Prevents carbon degradation |
Ensure your activated carbon performs at its best—contact our experts today to learn more about catalytic regeneration!