Induction hardening is a process used to harden the surface of metal parts by heating them with an alternating magnetic field and then rapidly cooling them. The temperature required for induction hardening typically exceeds the critical point temperature of the steel, which is the temperature at which the steel undergoes a phase transformation from ferrite to austenite. This critical temperature varies depending on the type of steel but is generally in the range of 700°C to 900°C (1292°F to 1652°F). The process involves placing the workpiece in an inductor coil, where an alternating current generates a magnetic field, inducing eddy currents that heat the surface of the workpiece. The high current density on the surface causes rapid heating, and once the desired temperature is reached, the workpiece is quickly cooled to achieve surface hardening.
Key Points Explained:
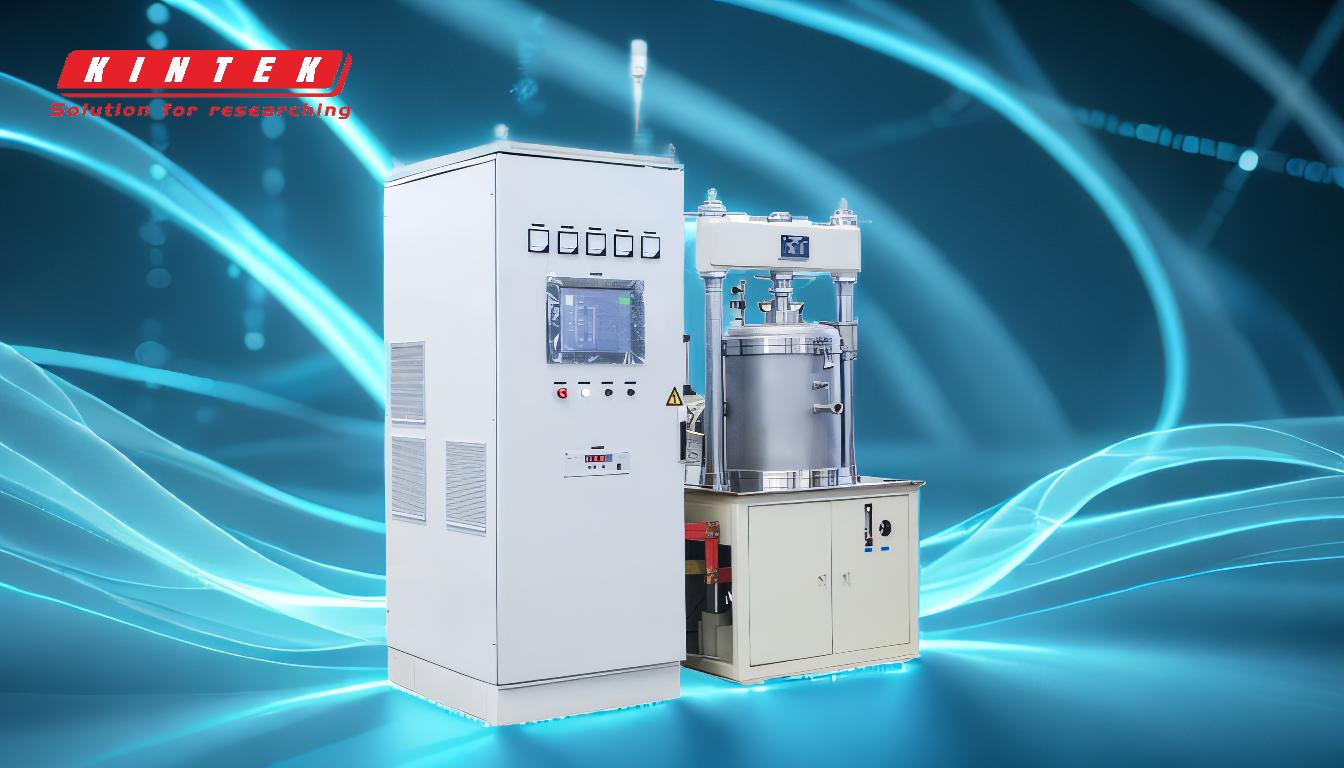
-
Induction Hardening Process:
- Induction hardening involves placing the workpiece in an inductor coil.
- An alternating current in the coil generates a magnetic field, inducing eddy currents in the workpiece.
- The eddy currents cause the surface of the workpiece to heat up rapidly due to the skin effect, where the current density is highest on the surface.
-
Temperature Range for Induction Hardening:
- The temperature required for induction hardening must exceed the critical point temperature of the steel.
- The critical point temperature is the temperature at which the steel transforms from ferrite to austenite, typically between 700°C and 900°C (1292°F to 1652°F).
- The exact temperature depends on the specific type of steel being treated.
-
Effect of Current Frequency:
- The frequency of the alternating current affects the depth of the heating layer.
- Higher frequencies result in a greater current density difference between the surface and the interior, leading to a thinner heating layer.
- This allows for precise control over the depth of the hardened layer, making induction hardening suitable for applications requiring specific surface hardness without affecting the core properties of the material.
-
Rapid Cooling:
- Once the surface of the workpiece reaches the critical temperature, it is rapidly cooled, typically using water, oil, or polymer-based quenchants.
- This rapid cooling transforms the austenite into martensite, a hard and brittle phase, resulting in a hardened surface layer.
-
Applications and Benefits:
- Induction hardening is widely used in industries such as automotive, aerospace, and manufacturing for components like gears, shafts, and bearings.
- The process offers several benefits, including localized hardening, minimal distortion, and the ability to harden specific areas of a part without affecting the entire component.
In summary, the temperature for induction hardening is determined by the critical point temperature of the steel, which is typically between 700°C and 900°C. The process involves heating the surface of the workpiece using an alternating magnetic field and then rapidly cooling it to achieve a hardened surface layer. The frequency of the alternating current influences the depth of the heating layer, allowing for precise control over the hardening process. Induction hardening is a versatile and efficient method for improving the wear resistance and durability of metal components.
Summary Table:
Key Aspect | Details |
---|---|
Temperature Range | 700°C to 900°C (1292°F to 1652°F) |
Critical Point Temperature | Phase transformation from ferrite to austenite |
Heating Mechanism | Alternating magnetic field induces eddy currents for rapid surface heating |
Cooling Method | Rapid cooling using water, oil, or polymer-based quenchants |
Applications | Gears, shafts, bearings in automotive, aerospace, and manufacturing |
Benefits | Localized hardening, minimal distortion, precise control |
Discover how induction hardening can improve your metal components—contact our experts today!