The temperature of a ceramic furnace varies depending on its type and application, but it generally ranges from 600°C to 1,700°C or higher. For instance, high-temperature ceramic applications often require heating to around 1,120°C (2,050°F) with precise temperature uniformity. Muffle furnaces, commonly used in laboratories, operate between 1,000°C and 1,800°C, while dental furnaces typically process materials at 600°C to 1,050°C. Standard sintering furnaces can reach up to 1,700°C. The specific temperature depends on the furnace's design, the materials being processed, and the intended application. Proper maintenance, such as operating below the furnace's maximum temperature and ensuring a clean environment, is crucial for longevity and performance.
Key Points Explained:
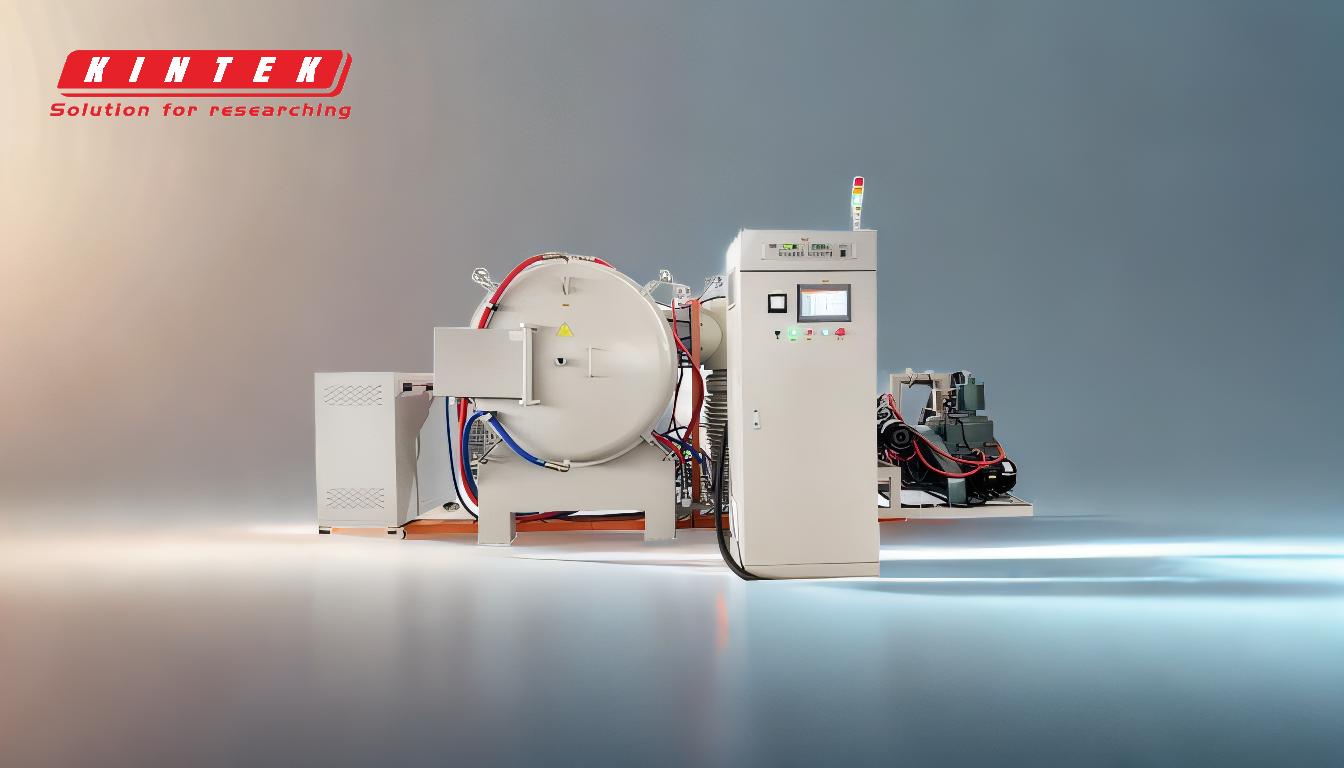
-
Temperature Range of Ceramic Furnaces:
- Ceramic furnaces operate across a wide temperature range, typically from 600°C to 1,700°C or higher, depending on the application.
- For example, high-temperature ceramic applications often require heating to around 1,120°C (2,050°F), with strict temperature uniformity (±5°F or 2.5°C) to ensure consistent results.
-
Muffle Furnaces:
- Muffle furnaces are commonly used in laboratories and industrial settings for processes requiring temperatures above 200°C.
- They typically operate between 1,000°C and 1,800°C, making them suitable for high-temperature applications such as sintering, annealing, and material testing.
- To prolong their lifespan, muffle furnaces should be operated at 50°C below their maximum temperature and kept in environments free from dust, humidity, and corrosive gases.
-
Dental Furnaces:
- Dental furnaces are specialized for processing dental materials and operate at temperatures between 600°C and 1,050°C.
- These furnaces are designed to handle the specific requirements of dental ceramics, ensuring precise temperature control for optimal results.
-
Sintering Furnaces:
- Standard sintering furnaces are used for high-temperature processes like sintering ceramics and metals.
- They can reach maximum temperatures ranging from 1,400°C to 1,700°C, depending on the furnace's design and the materials being processed.
-
Operating Conditions and Maintenance:
- Furnaces should be operated in environments with relative humidity not exceeding 85% and free from conductive dust, explosive gases, or corrosive gases.
- Dedicated power outlets are recommended to prevent power surges or circuit overloads, which can negatively affect performance.
- Proper airflow and a clean, temperature-controlled environment are essential for maintaining the furnace's efficiency and lifespan.
-
Specialized Furnaces:
- Continuous furnaces are designed for specific processes, such as annealing, hardening, or carburizing, and operate at constant temperatures.
- These furnaces are tailored for heating components made of the same grade of steel, ensuring consistent heat treatment cycles.
By understanding the specific temperature requirements and operating conditions of different types of ceramic furnaces, users can select the appropriate furnace for their needs and ensure its longevity and performance through proper maintenance.
Summary Table:
Furnace Type | Temperature Range | Key Applications |
---|---|---|
Muffle Furnace | 1,000°C - 1,800°C | Sintering, annealing, material testing |
Dental Furnace | 600°C - 1,050°C | Dental ceramics processing |
Sintering Furnace | 1,400°C - 1,700°C | High-temperature sintering of ceramics |
High-Temperature Furnace | Up to 1,700°C+ | Specialized high-temperature applications |
Need help selecting the right ceramic furnace for your needs? Contact our experts today for personalized advice!