The temperature of a heat-treating furnace varies significantly depending on the type of furnace, the material being treated, and the specific heat treatment process (e.g., annealing, hardening, normalizing, or carburizing). Continuous furnaces typically operate at permanent temperature conditions suited for specific processes, while specialized furnaces like HVF types can reach up to 3000°C. High-temperature furnaces generally operate up to 1700°C, and vacuum furnaces can range between 1,500 and 5,400°F. Muffle furnaces should operate 50°C below their maximum temperature for longevity. The exact temperature is determined by the material and treatment process, with common steel hardening temperatures ranging from 1400 to 2375°F.
Key Points Explained:
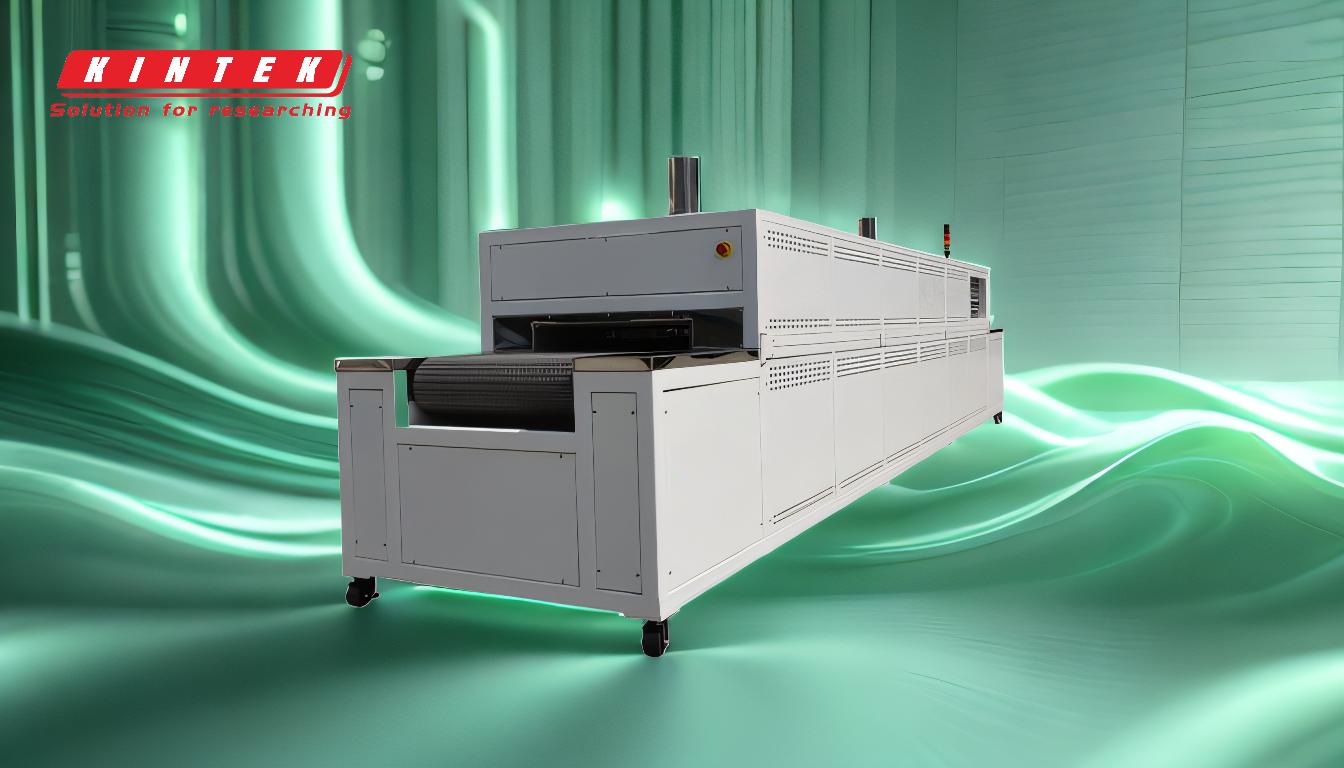
-
Types of Heat-Treating Furnaces and Their Temperature Ranges:
- Continuous Furnaces: Operate at permanent temperature conditions, ideal for repetitive processes like annealing, hardening, or carburizing. These furnaces are designed for consistency and efficiency when treating the same grade of steel or components.
- HVF-Type Furnaces: Capable of reaching extremely high temperatures, up to 3000°C, making them suitable for specialized applications requiring ultra-high heat.
- High-Temperature Furnaces: Typically have a maximum operating temperature of 1700°C, used for processes requiring intense heat but not as extreme as HVF furnaces.
- Vacuum Furnaces: Operate within a broad temperature range, from 1,500 to 5,400°F (approximately 815 to 2,982°C), depending on the system. These are used for processes requiring controlled atmospheres and precise temperature regulation.
- Muffle Furnaces: Should operate 50°C below their maximum temperature to ensure longevity of the furnace wire. These are often used in environments requiring protection from corrosive or volatile gases.
-
Factors Influencing Operating Temperature:
- Material Being Treated: The temperature is highly dependent on the material's properties. For example, common steels require hardening temperatures between 1400 and 2375°F (approximately 760 to 1,300°C).
- Heat Treatment Process: Different processes (e.g., annealing, hardening, normalizing) require specific temperature ranges. Annealing and normalizing temperatures for steels can vary widely based on the desired outcome.
-
Practical Considerations for Furnace Operation:
- Environmental Conditions: Muffle furnaces, for instance, should be used in environments with relative humidity not exceeding 85% and free from conductive dust, explosive gases, or corrosive gases.
- Material Preparation: When heating materials like metals with grease or volatile components, precautions such as using sealed containers or appropriate openings are necessary to prevent corrosion of heating elements.
-
Temperature Control and Longevity:
- Operating a furnace below its maximum temperature (e.g., 50°C below for muffle furnaces) ensures a longer lifespan for the furnace components, particularly the heating elements.
- Proper maintenance and adherence to operational guidelines are critical to maintaining consistent performance and avoiding premature wear or failure.
In summary, the temperature of a heat-treating furnace is not a fixed value but depends on the furnace type, material, and process. Understanding these variables is essential for selecting the right furnace and achieving optimal results in heat treatment applications.
Summary Table:
Furnace Type | Temperature Range | Key Applications |
---|---|---|
Continuous Furnaces | Permanent conditions for specific processes | Annealing, hardening, carburizing |
HVF-Type Furnaces | Up to 3000°C | Specialized applications requiring ultra-high heat |
High-Temperature Furnaces | Up to 1700°C | Processes requiring intense heat |
Vacuum Furnaces | 1,500 to 5,400°F (815 to 2,982°C) | Controlled atmosphere processes with precise temperature regulation |
Muffle Furnaces | Operate 50°C below maximum temperature | Environments requiring protection from corrosive or volatile gases |
Need help selecting the right heat-treating furnace for your application? Contact our experts today!