Induction heating is a versatile and efficient method for heating conductive materials, with temperatures ranging widely depending on the application. The temperature achieved through induction heating is influenced by factors such as the material's properties, the design of the induction system, and the power supply capacity. Induction heating can accommodate a wide range of temperature variations, from low-temperature applications like preheating to high-temperature processes such as metal melting. The heat is generated internally within the material, allowing for rapid and precise temperature control without direct contact, making it ideal for applications where contamination is a concern.
Key Points Explained:
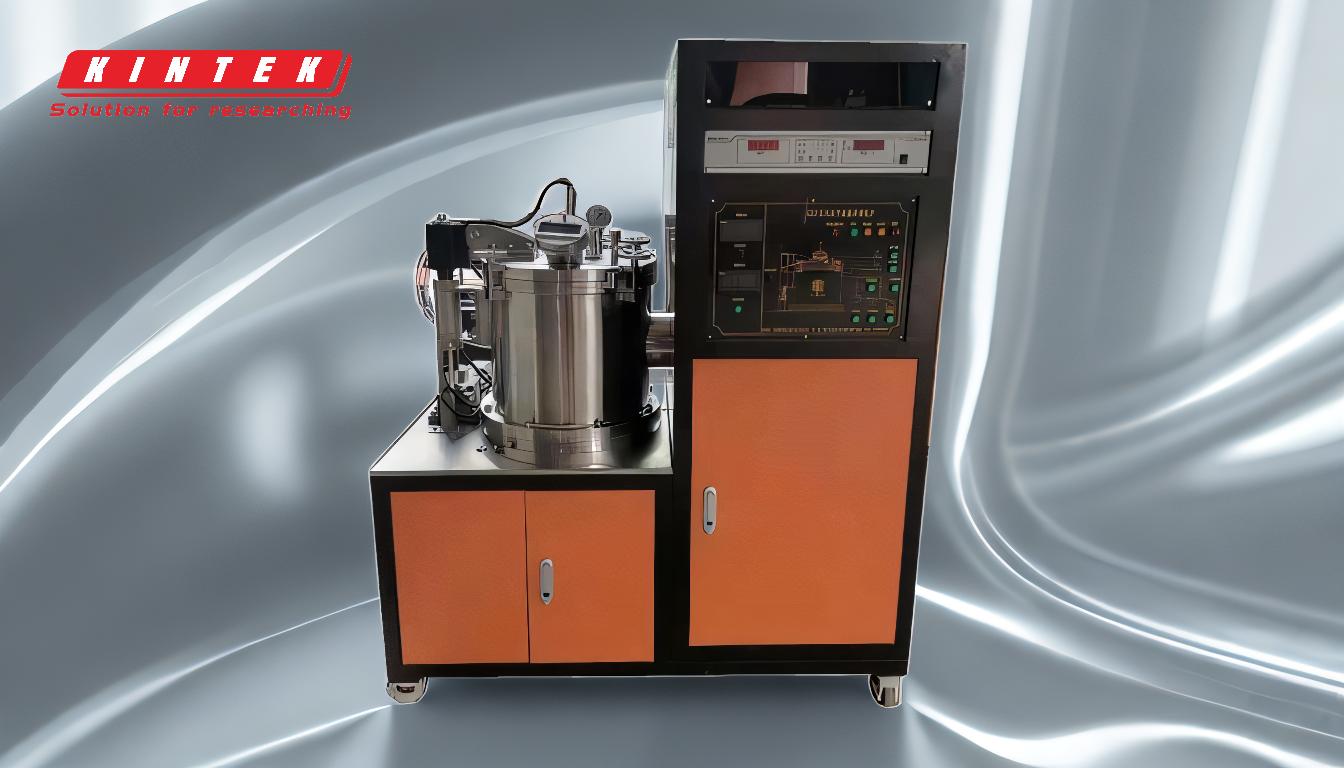
-
Temperature Range in Induction Heating
- Induction heating can achieve a wide range of temperatures, from relatively low temperatures for processes like preheating or annealing to extremely high temperatures for melting metals.
- The specific temperature depends on the application, material properties, and the power supplied to the induction system.
-
Factors Influencing Temperature
- Material Properties: The type of material being heated (e.g., metals, semiconductors) and its resistivity affect how quickly and to what temperature it can be heated. Materials with higher resistivity heat faster.
- Size and Thickness: Smaller and thinner materials heat more quickly and can reach higher temperatures in less time.
- Frequency of Alternating Current: Higher frequencies result in shallower heating depths, which can influence the temperature distribution within the material.
- Power Supply Capacity: The power supply must account for the material's specific heat, mass, required temperature rise, and heat losses due to conduction, convection, and radiation.
-
Internal Heat Generation
- Induction heating generates heat internally within the material through electromagnetic induction, rather than relying on external heat sources. This allows for rapid and efficient heating.
- The absence of direct contact with an external heat source minimizes contamination risks, making it suitable for applications in industries like medical device manufacturing.
-
Applications and Temperature Requirements
- Low-Temperature Applications: Preheating, drying, or annealing processes typically require lower temperatures.
- High-Temperature Applications: Processes like metal melting, forging, or hardening require much higher temperatures, often exceeding 1000°C.
- The temperature variation required for a specific application influences the design and power requirements of the induction heating system.
-
Types of Induction Heating Systems
- Intermediate Frequency Induction Heating: Characterized by fast heating speeds, high efficiency, and large output power, suitable for applications requiring moderate to high temperatures.
- High-Frequency Induction Heating: Known for its speed, compact size, and cost-effectiveness, ideal for small-scale or precision heating applications.
-
Efficiency and Control
- The efficiency of an induction heating system depends on the design of the inductor, the characteristics of the material being heated, and the required temperature change.
- Precise temperature control is achievable due to the localized and rapid nature of induction heating, making it suitable for processes requiring consistent and repeatable results.
-
Industrial Use Cases
- Induction heating is widely used in industries such as automotive, aerospace, and manufacturing for processes like brazing, soldering, hardening, and melting.
- Its ability to achieve high temperatures quickly and efficiently makes it a preferred method over traditional heating techniques like resistance or flame heating.
In summary, the temperature of induction heating varies significantly based on the application, material, and system design. It offers precise and rapid heating capabilities, making it a preferred choice for a wide range of industrial and commercial applications.
Summary Table:
Aspect | Details |
---|---|
Temperature Range | Low (preheating, annealing) to High (metal melting, >1000°C) |
Factors Influencing Temp | Material properties, size, frequency, power supply capacity |
Heat Generation | Internal, rapid, and precise; no direct contact minimizes contamination |
Applications | Preheating, drying, annealing, metal melting, forging, hardening |
System Types | Intermediate Frequency (moderate-high temp) & High Frequency (precision) |
Efficiency | High efficiency, precise control, repeatable results |
Industries | Automotive, aerospace, manufacturing, medical device production |
Unlock the potential of induction heating for your applications—contact our experts today to learn more!