Brazing is a joining process that involves heating a filler metal above its melting point and distributing it between two or more close-fitting parts by capillary action. The temperature range used for brazing is crucial to ensure a strong and reliable joint. Typically, the brazing temperature should be at least 25ºC (50ºF) above the liquidus temperature of the braze alloy to ensure proper flow and bonding. Specific parameters can vary, but common temperatures range from 577°C (1071°F) to 600°C (1112°F), with dwell times adjusted accordingly. The choice of heating method and the balance between time and temperature are also critical factors in achieving a successful brazed product.
Key Points Explained:
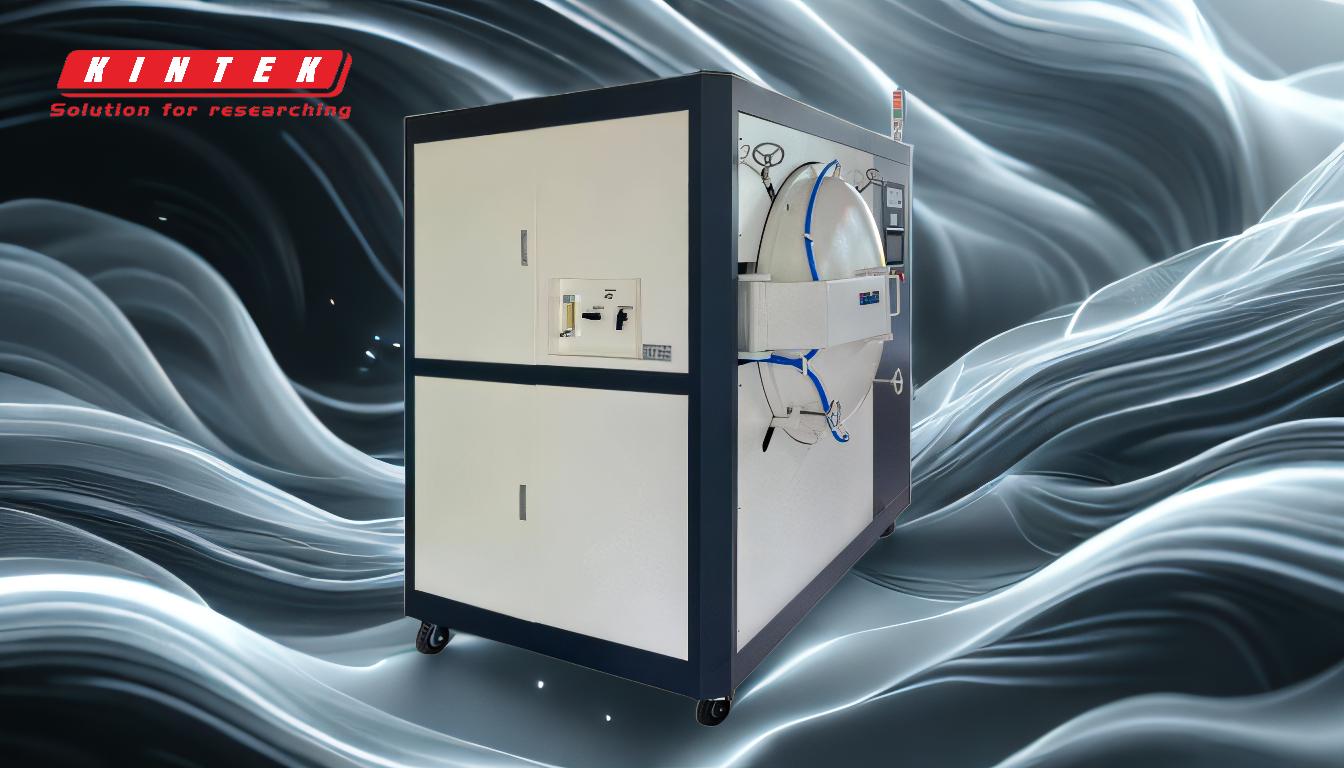
-
Temperature Range for Brazing:
- The brazing temperature should ideally be the lowest possible within the recommended range. This is typically at least 25ºC (50ºF) above the liquidus temperature of the braze alloy. This ensures that the filler metal flows properly and forms a strong bond without overheating the base materials.
- Specific parameters can vary depending on the materials and the brazing method used. For example, temperatures of ≥577°C (1071°F) for more than 5 minutes, or ≥585°C (1085°F) for a maximum of 1 to 8 minutes, are common. The maximum temperature should not exceed 600°C (1112°F) to avoid damaging the base materials.
-
Importance of Temperature Control:
- Temperature control is critical in brazing to achieve the desired mechanical properties of the joint. Excessive temperatures can lead to grain growth, oxidation, or even melting of the base materials, while insufficient temperatures may result in poor filler metal flow and weak joints.
- Cooling of powders during mechanical milling can accelerate the fracture process and suppress cold welding, recovery, and recrystallization, leading to rapid grain refinement. This principle can be analogously applied to brazing, where controlled cooling can help achieve the desired microstructure and joint strength.
-
Heating Methods in Brazing:
- Various heating methods are used in brazing, each with its own advantages and limitations. Common methods include:
- Torch Brazing: Uses a gas flame to heat the joint and filler metal.
- Furnace Brazing: Involves heating the assembly in a furnace, often with controlled atmospheres such as exothermic, hydrogen, argon, or vacuum.
- Induction Brazing: Uses electromagnetic induction to heat the joint.
- Dip Brazing: Involves immersing the assembly in a molten salt or metal bath.
- Resistance Brazing: Uses electrical resistance to generate heat at the joint.
- Infrared Brazing: Utilizes infrared radiation to heat the joint.
- Blanket Brazing: Uses flexible heating blankets for localized heating.
- Electron Beam and Laser Brazing: High-precision methods using focused energy beams.
- Braze Welding: Combines brazing and welding techniques for specific applications.
- Various heating methods are used in brazing, each with its own advantages and limitations. Common methods include:
-
Balance Between Time and Temperature:
- The balance between time and temperature is critical in the brazing process. Longer dwell times at the highest temperatures of the brazing cycle can reduce the amount of scrap and improve joint quality, provided the surface chemistry is good.
- For example, a longer dwell time at a slightly lower temperature may be more effective than a shorter dwell time at a higher temperature, as it allows for better filler metal flow and bonding without excessive heating of the base materials.
-
Surface Chemistry and Joint Quality:
- Good surface chemistry is essential for a successful brazing process. Proper cleaning and preparation of the surfaces to be joined ensure that the filler metal can wet and flow over the surfaces, forming a strong bond.
- Contaminants such as oils, oxides, or other residues can prevent proper wetting and bonding, leading to weak joints. Therefore, surface preparation, including cleaning and sometimes the use of fluxes, is a critical step in the brazing process.
In summary, the temperature range used for brazing is typically at least 25ºC (50ºF) above the liquidus temperature of the braze alloy, with common temperatures ranging from 577°C (1071°F) to 600°C (1112°F). The choice of heating method, the balance between time and temperature, and proper surface preparation are all critical factors in achieving a successful brazed joint.
Summary Table:
Parameter | Details |
---|---|
Temperature Range | 577°C (1071°F) to 600°C (1112°F) |
Liquidus Offset | At least 25ºC (50ºF) above the braze alloy's liquidus temperature |
Dwell Time | ≥577°C for >5 minutes or ≥585°C for 1–8 minutes |
Heating Methods | Torch, furnace, induction, dip, resistance, infrared, electron beam, laser |
Key Factors | Temperature control, time-temperature balance, surface chemistry |
Optimize your brazing process with expert guidance—contact us today!