Thermal deposition, specifically thermal evaporation deposition, is a widely used technique in thin-film coating processes. It involves heating a solid material in a high-vacuum environment until it vaporizes, creating a vapor stream that deposits onto a substrate as a thin film. This method is highly effective for creating precise and uniform coatings, ranging from single atomic layers to thicker films. The process relies on maintaining a high vacuum to ensure the vaporized material travels unimpeded to the substrate, where it condenses and forms a solid film. Thermal evaporation deposition is versatile, enabling the creation of freestanding structures and complex multi-layered designs, making it essential in industries such as electronics, optics, and materials science.
Key Points Explained:
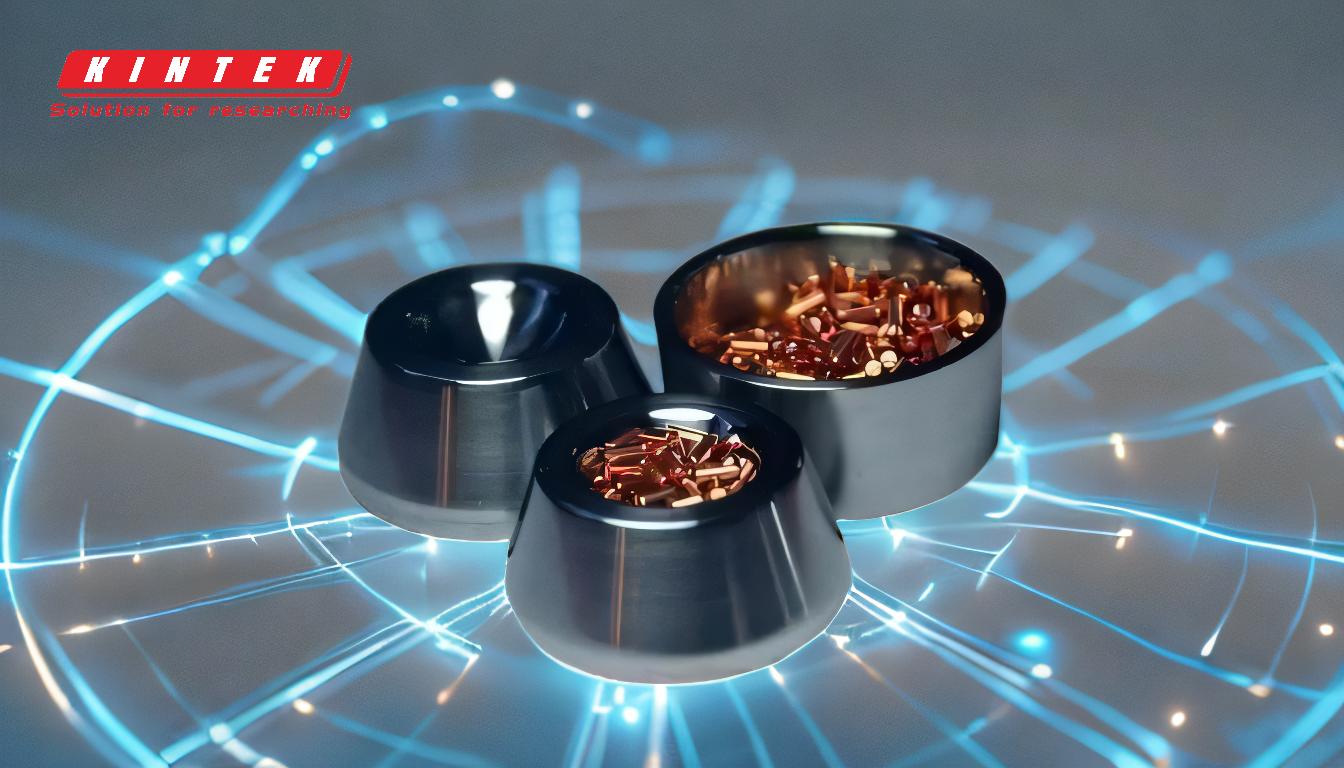
-
Process Overview:
- Thermal evaporation deposition is a vacuum-based coating technique where a solid material is heated to its evaporation point, producing a vapor stream.
- The vaporized material travels through the vacuum chamber and deposits onto a substrate, forming a thin film.
-
Heating Mechanism:
- The target material is heated using a tungsten filament, boat, basket, or electron beam.
- The heating process raises the material to its melting or boiling point, generating sufficient vapor pressure for evaporation.
-
Vacuum Environment:
- The process occurs in a high-vacuum chamber, typically maintained by a vacuum pump.
- The vacuum ensures minimal interference from other gases, allowing the vapor stream to travel freely and deposit uniformly on the substrate.
-
Vaporization and Deposition:
- The material transitions from a solid to a vapor state due to thermal energy.
- The vapor stream condenses on the substrate, forming a solid film with precise thickness and uniformity.
-
Applications:
- Used in creating thin films for electronics (e.g., semiconductors, solar cells), optics (e.g., anti-reflective coatings), and materials science (e.g., freestanding structures).
- Enables the deposition of multi-layered and complex designs.
-
Advantages:
- High precision and control over film thickness.
- Suitable for a wide range of materials, including metals, alloys, and some organic compounds.
- Minimal contamination due to the high-vacuum environment.
-
Limitations:
- Limited to materials with relatively low evaporation temperatures.
- May require additional techniques (e.g., electron beam evaporation) for high-melting-point materials.
- Challenges in achieving uniform coatings on complex or non-planar substrates.
-
Key Components:
- Vacuum Chamber: Provides the controlled environment for the process.
- Heating Source: Generates the thermal energy needed for evaporation.
- Substrate Holder: Positions the substrate for uniform deposition.
- Vacuum Pump: Maintains the high-vacuum conditions required for the process.
-
Material Considerations:
- The target material must have a vapor pressure suitable for evaporation at achievable temperatures.
- Compatibility with the heating source and substrate is critical for successful deposition.
-
Future Developments:
- Advancements in heating sources and vacuum technology are improving deposition rates and material compatibility.
- Integration with other deposition techniques (e.g., sputtering) is expanding the range of applications.
Thermal evaporation deposition is a foundational technique in thin-film fabrication, offering precision, versatility, and scalability. Its ability to create high-quality coatings makes it indispensable in modern manufacturing and research.
Summary Table:
Aspect | Details |
---|---|
Process Overview | Heating solid material in a vacuum to create a vapor stream for deposition. |
Heating Mechanism | Tungsten filament, boat, basket, or electron beam. |
Vacuum Environment | High-vacuum chamber ensures minimal gas interference. |
Applications | Electronics, optics, materials science (e.g., solar cells, coatings). |
Advantages | High precision, minimal contamination, versatile material compatibility. |
Limitations | Limited to low-evaporation-temperature materials. |
Key Components | Vacuum chamber, heating source, substrate holder, vacuum pump. |
Future Developments | Improved heating sources, vacuum tech, and integration with other methods. |
Discover how thermal evaporation deposition can enhance your projects—contact us today for expert advice!