The thin film process in semiconductors is a critical step in the fabrication of semiconductor devices, involving the deposition of thin layers of material onto a substrate. These layers, often only a few atoms or molecules thick, are essential for the functionality of devices like transistors, diodes, and integrated circuits. The process relies on high-precision techniques such as Chemical Vapour Deposition (CVD) and Physical Vapour Deposition (PVD) to ensure the films are pure, uniform, and adhere to strict performance standards. The quality of these thin films is paramount, as even minor defects can significantly impact the performance of the semiconductor device.
Key Points Explained:
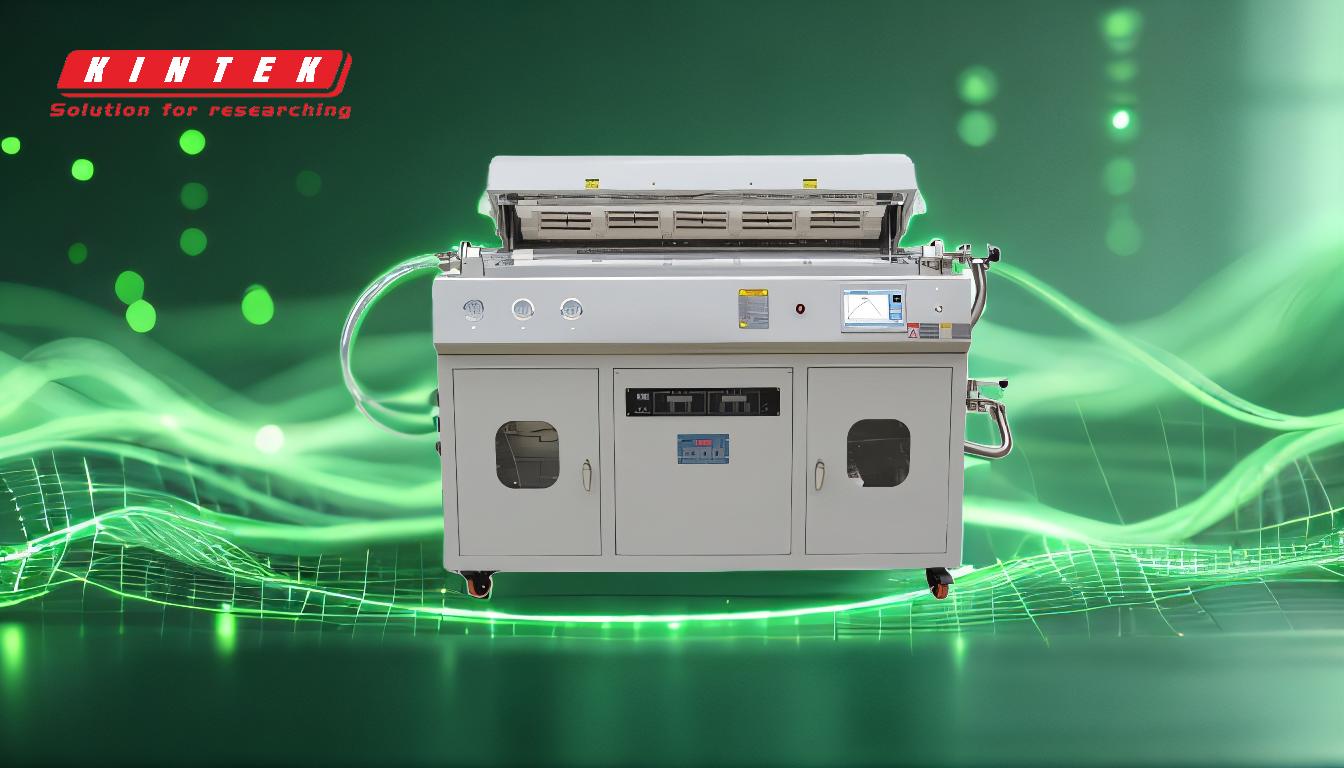
-
High-Precision Deposition Techniques:
- Chemical Vapour Deposition (CVD): This technique involves the chemical reaction of gaseous precursors to form a solid thin film on the substrate. CVD is widely used because it can produce high-quality, uniform films with excellent step coverage, meaning it can coat complex geometries evenly.
- Physical Vapour Deposition (PVD): PVD techniques, such as sputtering and evaporation, involve the physical transfer of material from a source to the substrate. These methods are valued for their ability to deposit a wide range of materials, including metals, alloys, and ceramics, with high precision and control over film thickness.
-
Optimal Manufacturing Conditions:
- Purity: The environment in which thin films are deposited must be meticulously controlled to prevent contamination. Even trace amounts of impurities can degrade the electrical properties of the semiconductor device.
- Temperature and Pressure: These parameters must be carefully regulated to ensure the desired chemical reactions occur and to control the growth rate and morphology of the thin film.
- Uniformity: Achieving a uniform film thickness is crucial for the consistent performance of semiconductor devices. Techniques like plasma-enhanced CVD (PECVD) and atomic layer deposition (ALD) are often used to enhance uniformity.
-
Atomic or Molecular Scale Deposition:
- Atomic Layer Deposition (ALD): ALD is a variant of CVD that allows for the deposition of films one atomic layer at a time. This method provides exceptional control over film thickness and composition, making it ideal for applications requiring ultra-thin, high-quality films.
- Molecular Beam Epitaxy (MBE): MBE is another technique used for depositing thin films at the atomic level. It is particularly useful for creating complex multilayer structures with precise control over each layer's composition and thickness.
-
Quality of Thin Films:
- Defects and Their Impact: Even a few misplaced atoms or molecules can create defects in the thin film, leading to issues such as increased electrical resistance, reduced carrier mobility, and overall degradation of device performance.
- Characterization Techniques: To ensure the quality of thin films, various characterization techniques are employed, including scanning electron microscopy (SEM), atomic force microscopy (AFM), and X-ray diffraction (XRD). These techniques help in identifying defects, measuring film thickness, and analyzing the film's structural properties.
In summary, the thin film process in semiconductors is a sophisticated and highly controlled procedure that plays a vital role in the performance and reliability of semiconductor devices. The use of advanced deposition techniques, stringent manufacturing conditions, and precise quality control measures ensures that the thin films meet the exacting standards required for modern semiconductor technology.
Summary Table:
Key Aspect | Details |
---|---|
Deposition Techniques | - CVD: Chemical Vapour Deposition for uniform, high-quality films. |
- PVD: Physical Vapour Deposition for precise material transfer. | |
Manufacturing Conditions | - Purity, temperature, and pressure control for optimal film quality. |
- Uniformity achieved via PECVD and ALD. | |
Atomic/Molecular Deposition | - ALD: Atomic Layer Deposition for ultra-thin, high-quality films. |
- MBE: Molecular Beam Epitaxy for precise multilayer structures. | |
Quality Control | - Defects impact device performance; SEM, AFM, and XRD used for analysis. |
Discover how advanced thin film processes can enhance your semiconductor devices—contact our experts today!