Cold isostatic pressing (CIP) is a versatile manufacturing process used primarily for consolidating powders or healing defects in castings across a wide range of materials, including ceramics, metals, composites, plastics, and carbon. It operates at room temperature, using liquid as the pressure medium and rubber or plastic molds, and can apply extremely high pressures (up to 100,000 psi). CIP is particularly useful for producing large or complex-shaped parts that cannot be easily formed using uniaxial presses. It is widely applied in industries such as solid-state battery production, wear and metal forming tools, advanced ceramics, and refractory materials. Additionally, CIP is used in research and development for process parameter studies and sample preparation.
Key Points Explained:
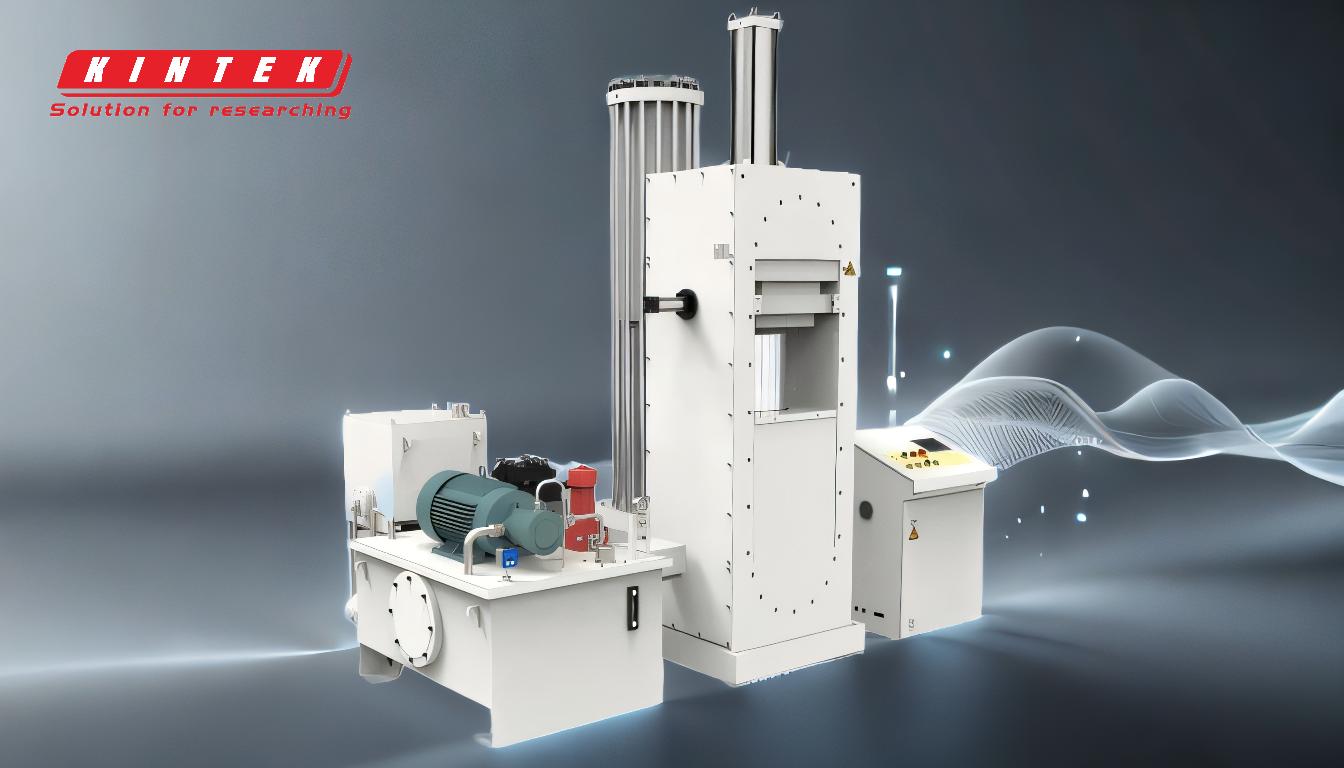
-
Principle of Cold Isostatic Pressing:
- CIP operates at room temperature, eliminating the need for heating devices.
- It uses a liquid medium (often an oil-water mixture) and rubber or plastic molds to apply uniform pressure on all sides of the material.
- The process can achieve extremely high pressures, typically ranging from 100 to 630 MPa (or up to 100,000 psi).
-
Applications in Industry:
- Solid-State Battery Production: CIP is used to prepare materials like garnet-based ultra-thin flexible composite solid electrolyte membranes and Li6.34La3Zr1.75Ta0.25O12 solid electrolytes. It is also employed in the production of negative electrode-free all-solid-state batteries.
- Advanced Ceramics and Refractory Materials: CIP is ideal for consolidating ceramic powders, graphite, and refractory materials. It is commonly used for materials such as silicon nitride, silicon carbide, boron nitride, and titanium boride.
- Wear and Metal Forming Tools: CIP is used to produce durable and complex-shaped tools that require high-density and uniform properties.
-
Advantages Over Uniaxial Pressing:
- CIP is suitable for large or intricate parts that cannot be effectively pressed using uniaxial methods.
- It provides uniform density and microstructure throughout the material, which is critical for high-performance applications.
- It is particularly beneficial for materials that do not require high precision in the sintered state.
-
Research and Development:
- CIP is used in laboratories for process parameter studies and to produce powder samples for research purposes.
- It allows for the exploration of new materials and manufacturing techniques, such as the development of isotropic graphite or artificial bones.
-
Material Versatility:
- CIP is applicable to a wide range of materials, including:
- Ceramics (e.g., silicon nitride, boron carbide)
- Metals (e.g., high-melting-point metals, tool steel)
- Composites and plastics
- Food processing and resin powders
- CIP is applicable to a wide range of materials, including:
-
Process Details:
- The powder material is placed in a mold and then into the CIP processing chamber.
- A liquid medium is pumped in and pressurized uniformly on all sides, ensuring consistent product quality.
- The high pressure compacts the powder into a dense, uniform shape, which can then be sintered or further processed.
By leveraging the unique capabilities of cold isostatic press, manufacturers can achieve high-quality, uniform products across a wide range of industries and applications.
Summary Table:
Aspect | Details |
---|---|
Principle | Operates at room temperature, uses liquid medium, and applies up to 100,000 psi. |
Applications | Solid-state batteries, advanced ceramics, wear tools, and R&D. |
Advantages | Uniform density, suitable for large/complex parts, versatile material use. |
Materials | Ceramics, metals, composites, plastics, and more. |
Process | Powder is pressed uniformly using liquid pressure in a mold. |
Interested in leveraging cold isostatic pressing for your manufacturing needs? Contact us today to learn more!