The vacuum evaporation technique for thin films is a physical vapor deposition (PVD) process where a material is heated in a vacuum chamber until it evaporates. The evaporated particles then condense onto a substrate, forming a thin film. This method is widely used in industries requiring precise and uniform coatings, such as electronics, optics, and advanced thin-film devices. The process relies on creating a vacuum environment to minimize contamination and ensure high-quality film deposition. Thermal evaporation, a common form of this technique, uses resistive heating or electron beams to melt and vaporize the material. The resulting thin films are crucial for applications like semiconductors, solar cells, and optical coatings.
Key Points Explained:
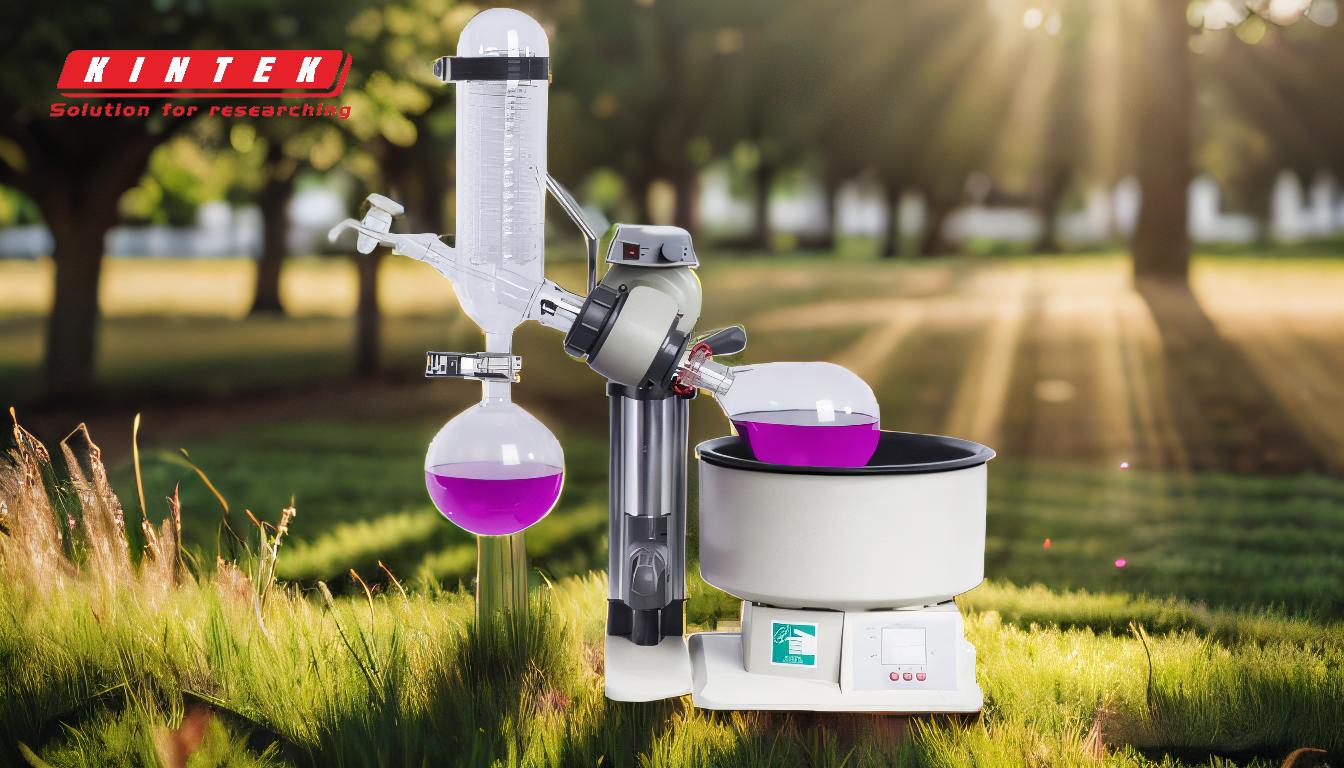
-
Definition and Process of Vacuum Evaporation:
- Vacuum evaporation is a type of Physical Vapor Deposition (PVD) where a material is heated in a vacuum chamber until it evaporates.
- The evaporated particles form a vapor stream that condenses onto a substrate, creating a thin film.
- This process is performed in a vacuum to reduce contamination and ensure uniform film deposition.
-
Types of Vacuum Evaporation:
- Thermal Evaporation: Uses resistive heating to melt and vaporize the material. The material is placed in a high-temperature-resistant container (boat, basket, or coil) and heated until it evaporates.
- Electron Beam Evaporation: An electron beam is directed at the material to heat and vaporize it, allowing for the deposition of high-melting-point materials.
- Chemical Vapor Evaporation: Similar to PVD but involves thermally induced chemical reactions to deposit the thin film.
-
Applications of Vacuum Evaporation:
- Electronics: Used to create thin films for semiconductors, integrated circuits, and microelectronic devices.
- Optics: Produces anti-reflective coatings, mirrors, and optical filters.
- Solar Cells: Deposits thin films for photovoltaic applications.
- Advanced Thin-Film Devices: Enables the creation of highly precise and uniform coatings for various high-tech applications.
-
Advantages of Vacuum Evaporation:
- High Purity: The vacuum environment minimizes contamination, resulting in high-purity thin films.
- Uniformity: Ensures consistent and uniform film thickness across the substrate.
- Versatility: Can deposit a wide range of materials, including metals, non-metals, oxides, and nitrides.
- Precision: Allows for precise control over film thickness and composition.
-
Challenges and Considerations:
- Material Limitations: Some materials may decompose or react under high temperatures, limiting their use in thermal evaporation.
- Equipment Cost: Vacuum systems and evaporation equipment can be expensive to install and maintain.
- Complexity: The process requires careful control of parameters like temperature, pressure, and deposition rate to achieve desired results.
-
Comparison with Other PVD Methods:
- Sputtering: Another common PVD method where atoms are ejected from a target material and deposited onto a substrate. Sputtering is often used for materials that are difficult to evaporate.
- Chemical Vapor Deposition (CVD): Involves chemical reactions to deposit thin films, unlike the purely physical process of vacuum evaporation.
-
Future Trends and Innovations:
- Nanotechnology: Vacuum evaporation is being adapted for the deposition of nanoscale thin films, enabling advancements in nanomaterials and devices.
- Hybrid Techniques: Combining vacuum evaporation with other methods like sputtering or CVD to enhance film properties and deposition efficiency.
- Sustainability: Developing more energy-efficient and environmentally friendly vacuum evaporation systems.
In summary, the vacuum evaporation technique is a versatile and precise method for depositing thin films, essential for various high-tech applications. Its ability to produce high-purity, uniform coatings makes it a cornerstone of modern manufacturing and research in fields like electronics, optics, and renewable energy.
Summary Table:
Aspect | Details |
---|---|
Definition | A PVD process where material is heated in a vacuum to evaporate and deposit thin films. |
Types | Thermal Evaporation, Electron Beam Evaporation, Chemical Vapor Evaporation. |
Applications | Semiconductors, optics, solar cells, and advanced thin-film devices. |
Advantages | High purity, uniformity, versatility, and precision. |
Challenges | Material limitations, high equipment costs, and process complexity. |
Comparison with PVD | Sputtering (ejects atoms) vs. CVD (chemical reactions). |
Future Trends | Nanotechnology, hybrid techniques, and sustainable systems. |
Discover how vacuum evaporation can enhance your thin-film applications—contact our experts today!