The VAR (Vacuum Arc Remelting) process is a specialized method used to refine and improve the quality of steel and other alloys. It involves remelting a consumable electrode under a vacuum atmosphere to achieve high purity, directional solidification, and enhanced mechanical properties. The process consists of three main phases: start-up, steady state, and hot top. Key components include a water-cooled copper crucible, a metallurgical vacuum, and a DC arc to initiate melting. The VAR process removes dissolved gases, reduces trace impurities, improves oxide cleanliness, and ensures uniform solidification, making it ideal for producing high-performance materials used in aerospace, medical, and industrial applications.
Key Points Explained:
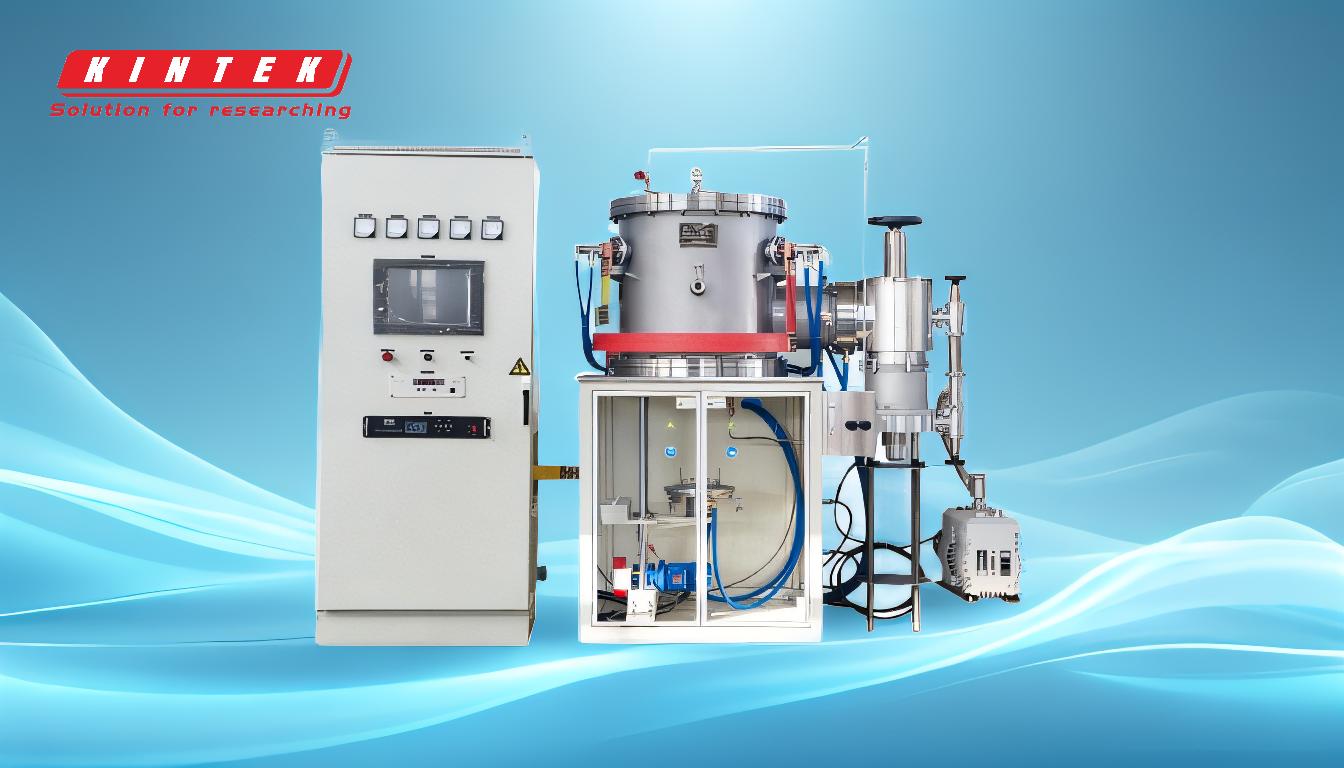
-
What is the VAR Process?
- The VAR process, or Vacuum Arc Remelting, is a secondary melting technique used to refine metals and alloys, particularly steel. It involves remelting a consumable electrode under a vacuum to achieve high purity and improved material properties.
- The process is essential for producing materials with enhanced strength, fatigue resistance, and cleanliness, making it suitable for critical applications.
-
Key Components of the VAR Process
- Crucible: A large cylindrical copper crucible with a water jacket for cooling. The crucible ensures controlled solidification and prevents contamination.
- Vacuum Atmosphere: The process operates under a metallurgical vacuum (0.001–0.1 mmHg or 0.1–13.3 Pa), which removes dissolved gases and volatile impurities.
- DC Arc: A high-current DC arc is used to melt the consumable electrode, initiating the remelting process.
- Consumable Electrode: The alloy to be refined is formed into a cylindrical electrode, which is continuously melted during the process.
-
Phases of the VAR Process
- Start-Up: The electrode is brought close to a small amount of alloy at the bottom of the crucible. An arc is struck to begin melting the electrode.
- Steady State: The melting process continues consistently, with the electrode being lowered as it is consumed. This phase ensures uniform melting and solidification.
- Hot Top: The final phase focuses on controlling the solidification of the ingot to minimize defects such as shrinkage cavities and segregation.
-
Advantages of the VAR Process
- Removal of Dissolved Gases: The vacuum environment eliminates hydrogen, nitrogen, and carbon dioxide, reducing the risk of gas-related defects.
- Reduction of Trace Elements: Volatile impurities with high vapor pressure are removed, enhancing material purity.
- Improved Oxide Cleanliness: The process reduces oxide inclusions, leading to better mechanical properties.
- Directional Solidification: Controlled cooling ensures uniform solidification, preventing macro-segregation and improving material homogeneity.
- Low Energy Input: The process is energy-efficient compared to other refining methods.
- Ceramic-Free Melting: The absence of ceramic liners eliminates potential contamination sources.
-
Applications of the VAR Process
- The VAR process is widely used in industries requiring high-performance materials, such as aerospace (turbine blades, engine components), medical (implants, surgical instruments), and industrial (tool steels, superalloys).
- It is particularly valuable for refining materials produced by the VIM (Vacuum Induction Melting) process, further enhancing their quality and performance.
-
Process Control in VAR
- Effective control of the arc current, cooling water flow, and electrode gap is critical to ensure consistent melting and solidification.
- The vacuum level must be maintained throughout the process to achieve the desired material properties.
By combining precise control, a vacuum environment, and directional solidification, the VAR process produces high-quality steel and alloys with superior mechanical and metallurgical properties, making it indispensable for advanced engineering applications.
Summary Table:
Aspect | Details |
---|---|
Process | Vacuum Arc Remelting (VAR) |
Key Components | Water-cooled crucible, metallurgical vacuum, DC arc, consumable electrode |
Phases | Start-up, steady state, hot top |
Advantages | Removes dissolved gases, reduces impurities, improves oxide cleanliness |
Applications | Aerospace, medical, industrial |
Process Control | Arc current, cooling water flow, electrode gap, vacuum level |
Discover how the VAR process can elevate your material quality—contact our experts today!