A rotary furnace operates by rotating a barrel-shaped chamber around its central axis, allowing materials to move from one end to the other due to a slight tilt. The rotation facilitates mixing and heating of the materials, while hot gases flow through the chamber to perform heat treatment. The furnace can be used for various applications, including smelting, heat treatment, and manufacturing lenses or mirrors. The heat source, typically gas or electric, transfers energy to the rotating tube, which then heats the materials inside. The furnace's design allows for efficient heat transfer and material processing, making it suitable for both continuous and batch operations.
Key Points Explained:
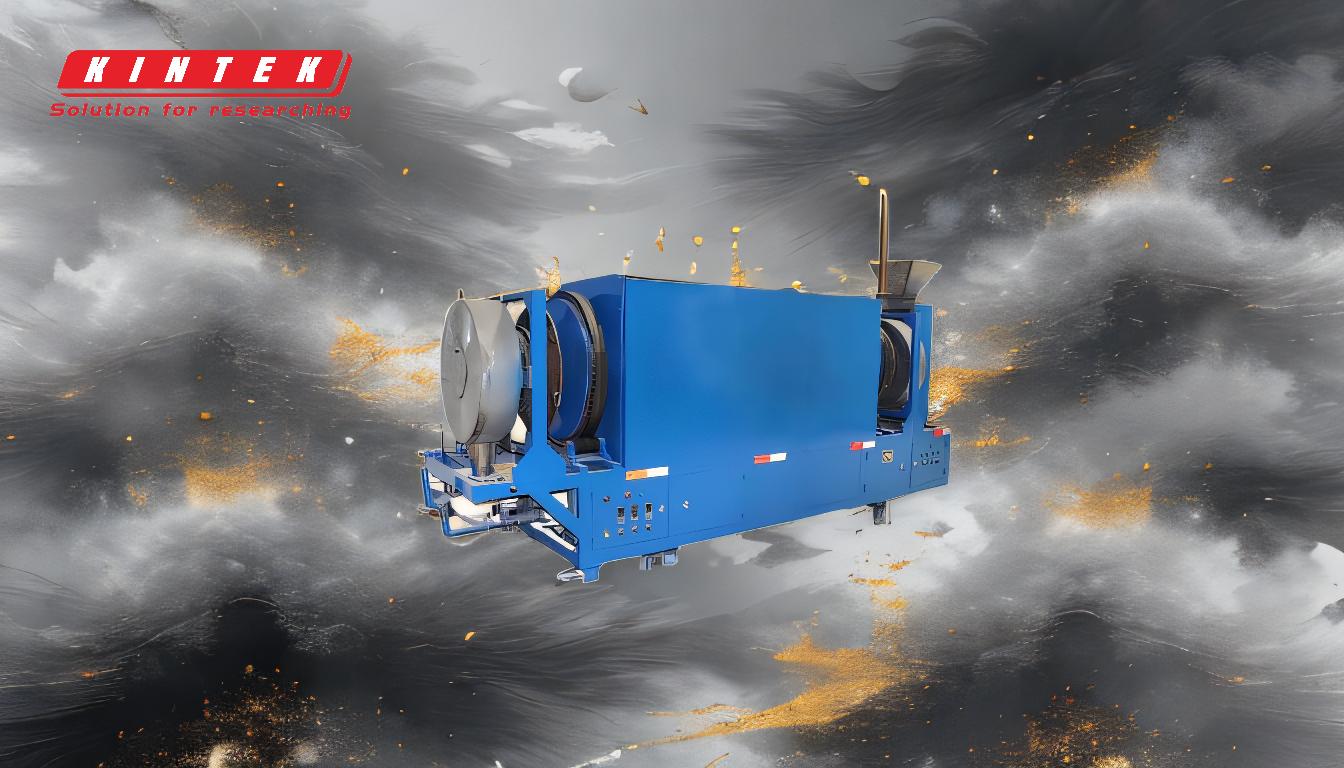
-
Basic Structure and Design:
- A rotary furnace is a barrel-shaped instrument that rotates around its central axis.
- It is slightly tilted to allow materials to move from one end to the other during rotation.
- The rotation can induce mixing or stirring of the materials, ensuring uniform heat treatment.
-
Material Transport and Heating:
- The mineral feed or process material is introduced into the reactor portion of the furnace.
- As the tube rotates, the materials are transported down its length.
- The materials are mixed and heated during this process, ensuring uniform exposure to heat.
-
Heat Transfer Mechanism:
- Heat is transferred from the heat source (gas or electric) to the rotating tube.
- The heat then transfers from the tube wall to the bed of material being processed.
- Hot gases pass through the chamber, typically in the opposite direction of the material flow, to perform the heat treatment.
-
Applications of Rotary Furnaces:
- Smelting and Heat Treatment: Used for smelting metals and heat-treating materials.
- Manufacturing Lenses and Mirrors: Utilized for creating lenses and mirrors using liquid metals like mercury or low-melting alloys like gallium.
- Continuous Thermal Systems: Indirect-fired rotary furnaces apply heat to incoming process material via multiple thermal control zones.
-
Operation and Control:
- The furnace can be operated by relatively unskilled workers.
- A batch is charged into the furnace, smelted for a given time period (4–6 hours), and then tapped for bullion and slag.
- The furnace can be controlled to maintain specific thermal zones, ensuring precise heat treatment.
-
Specialized Features:
- Centrifugal Force: In some applications, such as manufacturing lenses, the centrifugal force induced by spinning the furnace gives the melted material a specific shape (e.g., a paraboloid of revolution).
- Direction of Gas Flow: Hot gases can flow in the opposite direction of the material or in the same direction, depending on the application requirements.
-
Advantages of Rotary Furnaces:
- Efficient Heat Transfer: The rotating design ensures efficient heat transfer and uniform heating of materials.
- Versatility: Suitable for a wide range of applications, from smelting to manufacturing optical components.
- Ease of Operation: Can be operated by relatively unskilled workers, making it accessible for various industrial processes.
By understanding these key points, one can appreciate the versatility and efficiency of rotary furnaces in various industrial applications. The design and operation principles ensure that materials are uniformly heated and processed, making rotary furnaces an essential tool in many manufacturing and metallurgical processes.
Summary Table:
Key Feature | Description |
---|---|
Basic Structure | Barrel-shaped chamber rotating around its central axis with a slight tilt. |
Material Transport | Materials move from one end to the other, ensuring uniform heating and mixing. |
Heat Transfer | Heat flows from the source (gas/electric) to the tube, then to the materials. |
Applications | Smelting, heat treatment, manufacturing lenses/mirrors, and continuous systems. |
Operation | Suitable for batch or continuous processes, controlled by thermal zones. |
Advantages | Efficient heat transfer, versatility, and ease of operation. |
Discover how a rotary furnace can optimize your industrial processes—contact our experts today!