Physical Vapor Deposition (PVD) is a versatile technique used to deposit a wide range of materials onto substrates. The process involves converting a solid target material into a vapor phase, which then condenses onto the substrate to form a thin film. Materials commonly used in PVD include TiN, aluminides, MCrAlYs, Al2O3, ZrO2, ZrN, CrN, TiCN, TiAlN, and diamond-like coatings (DLCs). These materials are chosen for their specific properties, such as hardness, wear resistance, and thermal stability, making them suitable for various industrial applications.
Key Points Explained:
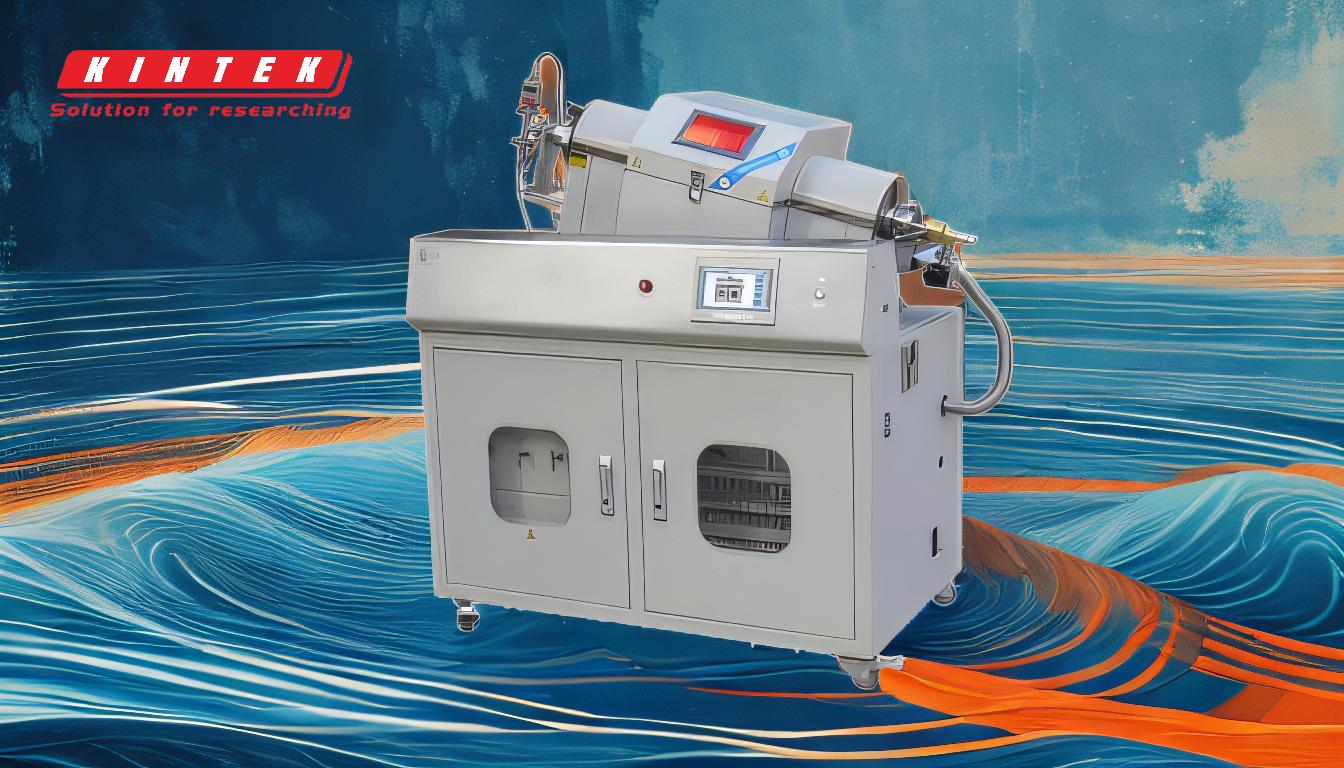
-
Materials Commonly Deposited via PVD:
- TiN (Titanium Nitride): Known for its hardness and gold-like appearance, TiN is widely used for wear-resistant coatings in cutting tools and decorative applications.
- Aluminides: These are used in high-temperature applications due to their excellent oxidation resistance.
- MCrAlYs: A family of alloys (where M stands for Ni, Co, or Fe) used in thermal barrier coatings for gas turbine components.
- Al2O3 (Aluminum Oxide): Provides excellent electrical insulation and corrosion resistance.
- ZrO2 (Zirconium Oxide): Used in thermal barrier coatings and as a dielectric material.
- ZrN (Zirconium Nitride): Offers high hardness and corrosion resistance, often used in decorative coatings.
- CrN (Chromium Nitride): Known for its wear and corrosion resistance, commonly used in tool coatings.
- TiCN (Titanium Carbonitride): Combines the properties of TiN and TiC, offering high hardness and wear resistance.
- TiAlN (Titanium Aluminum Nitride): Provides excellent thermal stability and oxidation resistance, making it ideal for high-speed machining applications.
- Diamond-Like Coatings (DLCs): These coatings mimic the properties of diamond, offering high hardness, low friction, and wear resistance.
-
PVD Process Overview:
- The PVD process involves converting a solid target material into a vapor phase. This is achieved through methods such as sputtering, evaporation, or arc vaporization. The vaporized material then condenses onto the substrate, forming a thin film. The choice of method depends on the specific material and application requirements.
-
Comparison with CVD:
- While PVD is primarily used for depositing metals and ceramics, Chemical Vapor Deposition (CVD) is often used for depositing materials like silicon dioxide (SiO2), silicon nitride (SiN), polysilicon, and silicon-oxynitride. CVD involves chemical reactions at the substrate surface, allowing for the deposition of complex materials with adjustable properties such as refractive index and stress. For example, microwave plasma chemical vapor deposition is a specialized form of CVD that uses microwave energy to generate plasma, enabling the deposition of high-quality thin films at lower temperatures.
-
Applications of PVD Materials:
- Cutting Tools: TiN, TiCN, and TiAlN coatings are extensively used to enhance the performance and lifespan of cutting tools.
- Aerospace: MCrAlYs and aluminides are used in thermal barrier coatings for turbine blades and other high-temperature components.
- Electronics: Al2O3 and ZrO2 are used as dielectric layers in electronic devices.
- Decorative Coatings: ZrN and TiN are popular for their aesthetic appeal and durability in decorative applications.
-
Advantages of PVD:
- High Purity: PVD allows for the deposition of high-purity materials with minimal contamination.
- Adhesion: The films deposited via PVD typically have excellent adhesion to the substrate.
- Versatility: PVD can deposit a wide range of materials, making it suitable for various industries.
In summary, PVD is a critical technology for depositing a wide array of materials with specific properties tailored to various industrial needs. The choice of material depends on the desired characteristics, such as hardness, wear resistance, and thermal stability, making PVD a versatile and essential process in modern manufacturing.
Summary Table:
Material | Key Properties | Common Applications |
---|---|---|
TiN (Titanium Nitride) | Hardness, wear resistance, gold-like appearance | Cutting tools, decorative coatings |
Aluminides | Oxidation resistance | High-temperature applications |
MCrAlYs | Thermal stability | Gas turbine components |
Al2O3 (Aluminum Oxide) | Electrical insulation, corrosion resistance | Electronics |
ZrO2 (Zirconium Oxide) | Thermal barrier, dielectric properties | Aerospace, electronics |
ZrN (Zirconium Nitride) | Hardness, corrosion resistance | Decorative coatings |
CrN (Chromium Nitride) | Wear and corrosion resistance | Tool coatings |
TiCN (Titanium Carbonitride) | High hardness, wear resistance | Cutting tools |
TiAlN (Titanium Aluminum Nitride) | Thermal stability, oxidation resistance | High-speed machining |
DLCs (Diamond-Like Coatings) | High hardness, low friction, wear resistance | Industrial coatings |
Unlock the potential of PVD for your industry—contact our experts today to learn more!