Refractory materials are essential in high-temperature applications, such as furnaces, due to their ability to withstand extreme heat without degrading. These materials are typically composed of oxides like alumina (Al₂O₃), silica (SiO₂), magnesia (MgO), and calcium oxide (CaO), as well as advanced compounds like silicon carbide (SiC). They are often used in multi-layer designs, incorporating lightweight alumina ceramic fibers and insulation boards to minimize heat loss and energy consumption. Refractories are designed to provide thermal insulation, structural integrity, and resistance to chemical corrosion, ensuring efficient and uniform process conditions in industrial applications.
Key Points Explained:
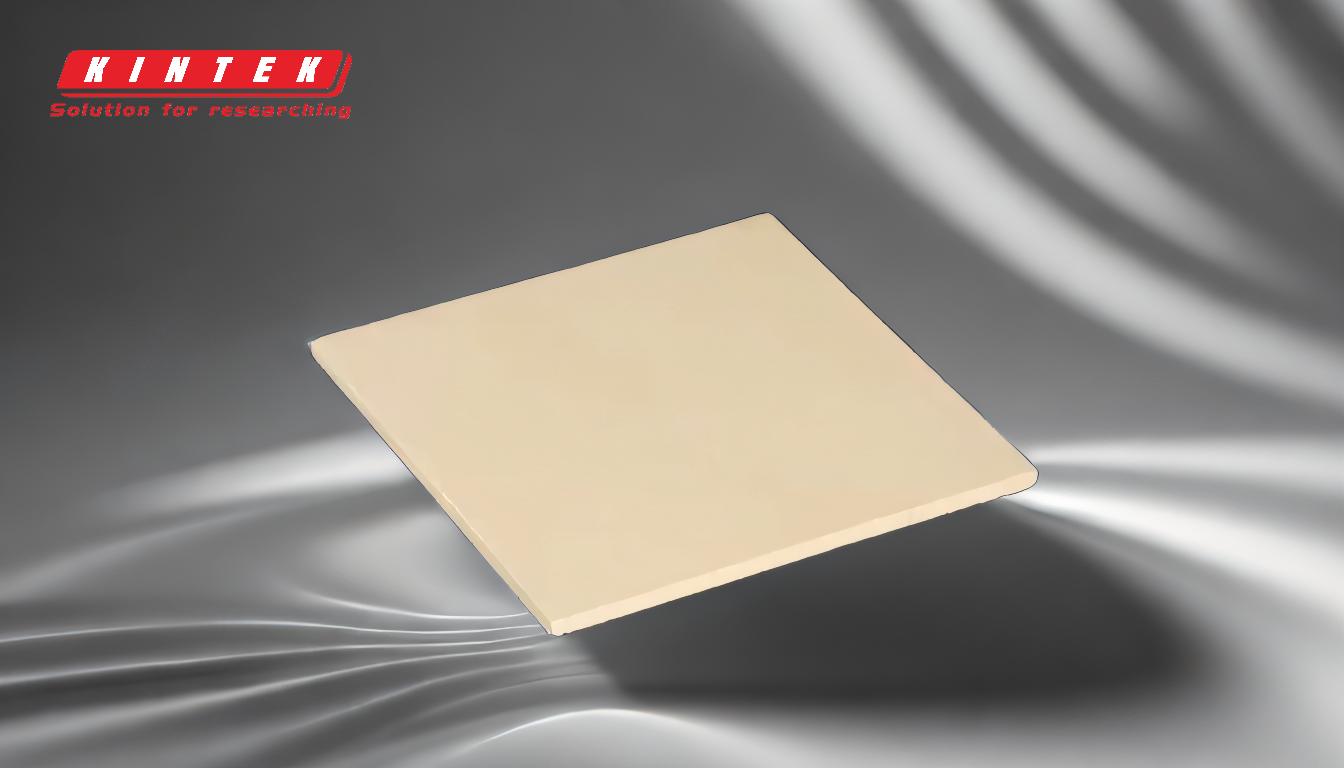
-
Primary Materials Used in Refractories:
- Alumina (Al₂O₃): A key oxide used in refractories due to its high melting point, excellent thermal stability, and resistance to chemical attack. It is commonly found in lightweight ceramic fibers and insulating firebricks.
- Silica (SiO₂): Known for its high-temperature resistance and low thermal expansion, silica is often used in refractory bricks and linings.
- Magnesia (MgO): Provides excellent resistance to basic slags and high-temperature environments, making it suitable for steelmaking and other high-heat processes.
- Calcium Oxide (CaO): Often used in combination with other oxides to improve refractory properties, particularly in applications requiring resistance to acidic environments.
- Silicon Carbide (SiC): An advanced ceramic material with exceptional thermal conductivity, mechanical strength, and resistance to oxidation, commonly used in high-performance refractory applications.
-
Multi-Layer Insulation Design:
- Refractory materials are often arranged in multi-layer configurations to optimize thermal insulation and energy efficiency.
- Lightweight alumina ceramic fibers are used in the inner layers to reduce heat loss and improve insulation.
- High-quality insulation boards provide structural backing, ensuring durability and stability under high temperatures.
-
Absence of Asbestos:
- Modern refractory materials are designed without asbestos, which is harmful to health. This ensures safer working environments and compliance with health and safety regulations.
-
Applications and Benefits:
- Refractories are used in furnaces, kilns, reactors, and other high-temperature industrial equipment.
- They ensure uniform heat distribution, reduce energy consumption, and extend the lifespan of equipment by protecting against thermal and chemical degradation.
By understanding the composition and design of refractory materials, purchasers can select the most suitable options for their specific high-temperature applications, ensuring optimal performance and cost-efficiency.
Summary Table:
Component | Properties | Applications |
---|---|---|
Alumina (Al₂O₃) | High melting point, thermal stability, chemical resistance | Lightweight ceramic fibers, insulating firebricks |
Silica (SiO₂) | High-temperature resistance, low thermal expansion | Refractory bricks, linings |
Magnesia (MgO) | Resistance to basic slags, high-temperature environments | Steelmaking, high-heat processes |
Calcium Oxide (CaO) | Improves refractory properties, acidic environment resistance | Acid-resistant applications |
Silicon Carbide (SiC) | Exceptional thermal conductivity, mechanical strength, oxidation resistance | High-performance refractory applications |
Need the right refractory materials for your high-temperature processes? Contact us today for expert guidance!