PVD (Physical Vapor Deposition) plating utilizes a wide range of materials, including metals, alloys, ceramics, and specialized compounds like carbides, nitrides, silicides, and borides. These materials are chosen for their unique properties, such as enhanced hardness, wear resistance, corrosion resistance, and aesthetic appeal. Common examples include titanium nitride (TiN), zirconium nitride (ZrN), chromium nitride (CrN), and diamond-like carbon (DLC), which are widely used in industries like aerospace, automotive, electronics, and decorative applications. The choice of material depends on the specific performance requirements of the application, such as durability, conductivity, or optical properties.
Key Points Explained:
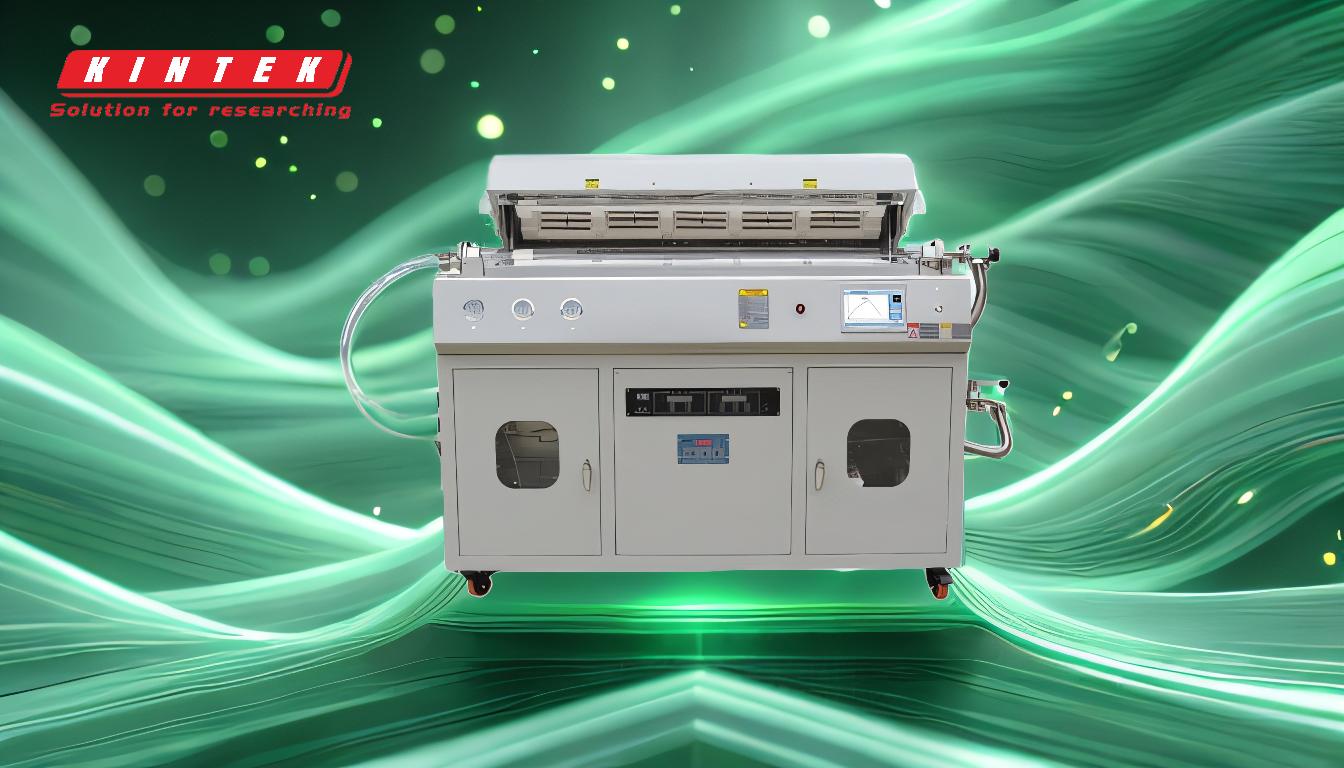
-
Types of Materials Used in PVD Plating:
- Metals: Titanium, zirconium, aluminum, stainless steel, and copper are commonly used in PVD coatings. These metals are selected for their mechanical and chemical properties, such as strength, conductivity, and corrosion resistance.
- Alloys: Combinations of metals like aluminum-chromium (AlCr) are used to enhance specific properties, such as extending the service life of tools and machine parts.
- Ceramics: Ceramic materials like titanium nitride (TiN), zirconium nitride (ZrN), and chromium nitride (CrN) are popular for their hardness and wear resistance.
- Specialized Compounds: Carbides, nitrides, silicides, and borides are used for specialized applications, particularly in demanding environments like aerospace and automotive industries.
-
Common PVD Coating Materials and Their Applications:
- Titanium Nitride (TiN): Widely used for decorative purposes (e.g., watches, jewellery, hardware parts) and functional applications due to its gold-like appearance and excellent wear resistance.
- Zirconium Nitride (ZrN): Known for its high hardness and corrosion resistance, ZrN is used in cutting tools and decorative coatings.
- Chromium Nitride (CrN): Offers superior corrosion resistance and is commonly used in industrial machinery and automotive components.
- Diamond-Like Carbon (DLC): Provides exceptional hardness and low friction, making it ideal for applications requiring wear resistance, such as automotive parts and medical devices.
- Indium Tin Oxide (ITO): A high-conductivity, high-hardness film used in electronic displays, including LCDs, plasma displays, and touch panels.
- Zinc Tin (ZnSn): Used as an optical coating in low-emissivity (low-e) windows and glass to improve energy efficiency.
-
Industry-Specific Applications:
- Aerospace: Gold coatings are frequently requested for aerospace electronics due to their excellent conductivity and corrosion resistance.
- Automotive: Materials like DLC and CrN are used to enhance the durability and performance of engine components and other critical parts.
- Electronics: ITO thin films are essential for manufacturing displays and touch panels, while TiN and ZrN are used for decorative and functional coatings on consumer electronics.
- Decorative Applications: TiN and Cr2N are popular for their aesthetic appeal, often used in watches, jewellery, and sanitary ware.
-
Substrates for PVD Coatings:
- PVD coatings can be applied to a variety of substrates, including metals (e.g., stainless steel, aluminum), plastics, glass, ceramics, and even nylon. The choice of substrate depends on the application and the desired properties of the final product.
-
Performance Characteristics:
- Hardness: Materials like TiN, ZrN, and DLC provide enhanced hardness, making them suitable for cutting tools and wear-resistant components.
- Wear Resistance: Coatings such as CrN and DLC are designed to withstand abrasive and frictional forces, extending the lifespan of tools and machinery.
- Corrosion Resistance: CrN and AlCr coatings are highly resistant to corrosion, making them ideal for harsh environments.
- Optical Properties: ZnSn and ITO are used for their optical characteristics, such as transparency and reflectivity, in applications like energy-efficient windows and electronic displays.
-
Versatility of PVD Materials:
- The versatility of PVD materials allows them to be tailored to meet the specific requirements of different industries. For example, aerospace components may require coatings with high conductivity and corrosion resistance, while decorative applications prioritize aesthetic qualities like color and finish.
By understanding the materials used in PVD plating and their unique properties, manufacturers and purchasers can make informed decisions to select the most suitable coatings for their specific applications.
Summary Table:
Material Type | Examples | Key Properties | Common Applications |
---|---|---|---|
Metals | Titanium, Zirconium, Aluminum | Strength, Conductivity, Corrosion Resistance | Aerospace, Automotive, Electronics |
Alloys | Aluminum-Chromium (AlCr) | Extended Service Life | Tools, Machine Parts |
Ceramics | TiN, ZrN, CrN | Hardness, Wear Resistance | Cutting Tools, Decorative Coatings |
Specialized Compounds | Carbides, Nitrides, Silicides | Enhanced Durability, Corrosion Resistance | Aerospace, Automotive |
Diamond-Like Carbon (DLC) | - | Exceptional Hardness, Low Friction | Automotive Parts, Medical Devices |
Indium Tin Oxide (ITO) | - | High Conductivity, Hardness | Electronic Displays, Touch Panels |
Zinc Tin (ZnSn) | - | Optical Properties | Low-Emissivity Windows, Glass |
Ready to enhance your products with PVD coatings? Contact us today to find the perfect solution for your needs!