To fire alumina (aluminum oxide, Al₂O₃), the temperature required depends on the desired properties of the final product, such as density, grain size, and mechanical strength. Based on the reference provided, firing pure alumina powder compacts at 1350 °C for 20 minutes achieves a high density (about 99% of the theoretical value) and a fine grain size of 1.2 μm. This temperature is suitable for achieving a dense and fine-grained microstructure, which is critical for applications requiring high mechanical strength and durability. However, firing temperatures can vary depending on the specific application, the type of alumina powder used, and the desired outcome.
Key Points Explained:
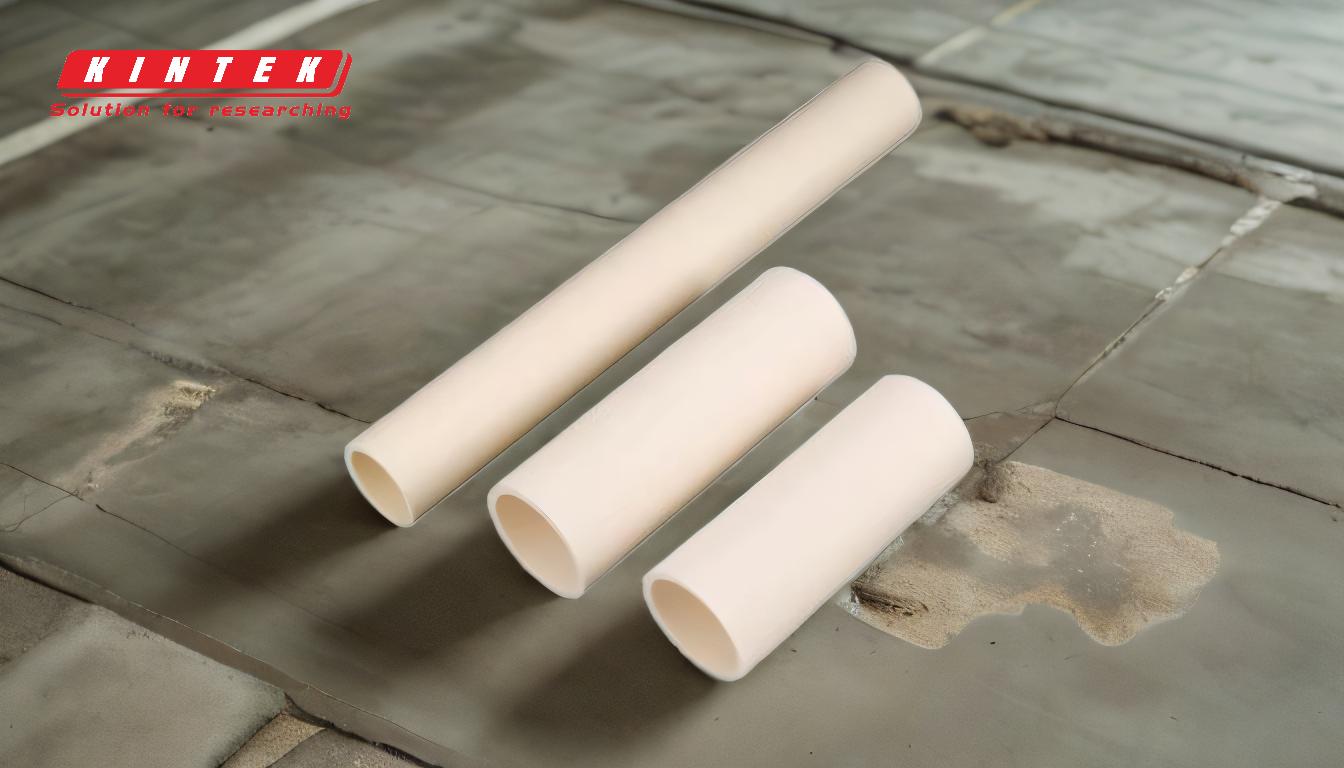
-
Firing Temperature for Alumina:
- The reference states that firing pure alumina powder compacts at 1350 °C for 20 minutes results in a density of about 99% of the theoretical value and a grain size of 1.2 μm.
- This temperature is ideal for achieving a dense and fine-grained microstructure, which is essential for high-performance applications.
-
Importance of Temperature Control:
- The firing temperature directly impacts the sintering process, which involves the consolidation of powder particles into a solid mass through heat.
- At 1350 °C, the alumina particles undergo sufficient diffusion to bond together, leading to high density and small grain size.
- Higher temperatures may lead to excessive grain growth, while lower temperatures may result in incomplete sintering and lower density.
-
Density and Grain Size:
- Achieving a density of 99% of the theoretical value indicates that the material has minimal porosity, which enhances its mechanical properties, such as hardness and fracture toughness.
- A grain size of 1.2 μm is considered fine, contributing to improved strength and wear resistance.
-
Factors Influencing Firing Temperature:
- Type of Alumina Powder: Pure alumina powders may require different firing temperatures compared to doped or composite alumina materials.
- Application Requirements: For applications requiring ultra-high density and fine grain size, a precise temperature like 1350 °C is recommended.
- Firing Time: The reference specifies a firing time of 20 minutes, which is relatively short but sufficient for achieving the desired properties.
-
Practical Considerations for Equipment and Consumables Purchasers:
- When selecting a furnace for firing alumina, ensure it can maintain a consistent temperature of 1350 °C with minimal fluctuations.
- Consider the thermal stability and energy efficiency of the furnace, as high temperatures can lead to significant energy consumption.
- For consumables, such as crucibles or setters, choose materials that can withstand high temperatures without reacting with alumina.
By understanding these key points, purchasers can make informed decisions about the equipment and consumables needed for firing alumina, ensuring optimal results for their specific applications.
Summary Table:
Parameter | Value |
---|---|
Firing Temperature | 1350 °C |
Firing Time | 20 minutes |
Density Achieved | 99% of theoretical value |
Grain Size | 1.2 μm |
Key Benefits | High density, fine grain size, enhanced mechanical strength |
Factors Influencing Temperature | Type of alumina powder, application requirements, firing time |
Need help selecting the right furnace for firing alumina? Contact our experts today for tailored solutions!