The temperature required to mold plastic depends on the type of plastic being used, as different polymers have distinct melting points and processing requirements. Generally, thermoplastics, which are the most commonly molded plastics, require heating to a temperature above their glass transition or melting point to become pliable. For example, common plastics like polyethylene (PE) and polypropylene (PP) typically require temperatures between 130°C and 300°C, while engineering plastics like polycarbonate (PC) or nylon may need higher temperatures, often exceeding 300°C. The exact temperature must be carefully controlled to avoid degradation, ensure proper flow, and achieve the desired properties in the final product.
Key Points Explained:
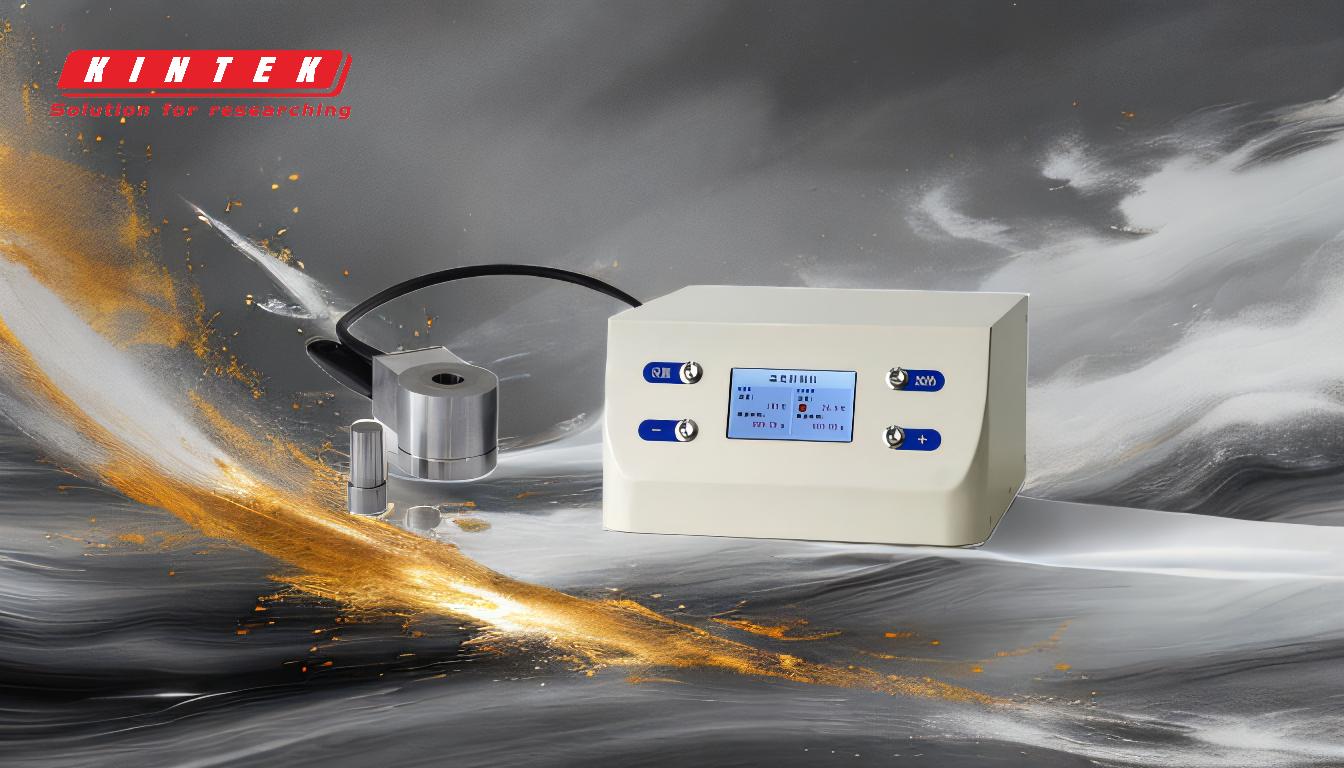
-
Types of Plastics and Their Temperature Requirements:
-
Thermoplastics: These plastics, such as polyethylene (PE), polypropylene (PP), and polycarbonate (PC), are the most commonly molded. They soften when heated and harden upon cooling, making them ideal for molding processes like injection molding. Each thermoplastic has a specific melting or glass transition temperature:
- Polyethylene (PE): 105°C to 135°C.
- Polypropylene (PP): 130°C to 170°C.
- Polycarbonate (PC): 220°C to 300°C.
- Thermosetting Plastics: These plastics, such as epoxy and phenolic resins, require heat to initiate a chemical reaction that hardens them permanently. Once set, they cannot be remelted. Their molding temperatures vary but are generally higher than thermoplastics.
-
Thermoplastics: These plastics, such as polyethylene (PE), polypropylene (PP), and polycarbonate (PC), are the most commonly molded. They soften when heated and harden upon cooling, making them ideal for molding processes like injection molding. Each thermoplastic has a specific melting or glass transition temperature:
-
Importance of Temperature Control:
- Preventing Degradation: Excessive heat can cause plastic to degrade, leading to discoloration, brittleness, or the release of harmful gases. For example, PVC can release hydrochloric acid if overheated.
- Ensuring Proper Flow: The plastic must reach a temperature where it flows easily into the mold cavity without causing defects like incomplete filling or air traps.
- Achieving Desired Properties: The temperature affects the crystallinity, strength, and surface finish of the final product. For instance, higher temperatures can improve surface gloss but may reduce mechanical strength.
-
Factors Influencing Molding Temperature:
- Polymer Type: Different polymers have unique thermal properties. For example, nylon requires higher temperatures due to its high melting point.
- Additives and Fillers: Materials like glass fibers or flame retardants can alter the processing temperature.
- Mold Design and Cooling Rate: The mold's design and cooling system affect how quickly the plastic solidifies, which in turn influences the required molding temperature.
-
Common Molding Processes and Their Temperature Ranges:
- Injection Molding: Typically used for thermoplastics, with temperatures ranging from 150°C to 300°C depending on the material.
- Blow Molding: Often used for making hollow objects like bottles, with temperatures similar to injection molding.
- Compression Molding: Common for thermosetting plastics, requiring higher temperatures to initiate curing.
-
Practical Considerations for Equipment:
- Heating Systems: Molding machines must have precise heating systems to maintain consistent temperatures. For example, barrel heaters in injection molding machines must evenly distribute heat to prevent cold spots.
- Cooling Systems: Efficient cooling is essential to solidify the plastic quickly and maintain cycle times. Water-cooled molds are commonly used.
- Temperature Monitoring: Sensors and controllers are critical for maintaining the correct temperature throughout the molding process.
-
Examples of Specific Plastics and Their Molding Temperatures:
- Polyethylene Terephthalate (PET): Used for bottles, requires temperatures around 260°C to 290°C.
- Acrylonitrile Butadiene Styrene (ABS): Commonly used in automotive parts, requires temperatures between 210°C and 250°C.
- Polystyrene (PS): Used for disposable cutlery, requires temperatures around 180°C to 240°C.
In summary, the temperature needed to mold plastic varies widely depending on the type of plastic, the molding process, and the desired properties of the final product. Careful control of temperature is essential to ensure high-quality, defect-free molded parts.
Summary Table:
Plastic Type | Temperature Range (°C) | Key Applications |
---|---|---|
Polyethylene (PE) | 105°C - 135°C | Packaging, containers |
Polypropylene (PP) | 130°C - 170°C | Automotive parts, textiles |
Polycarbonate (PC) | 220°C - 300°C | Electronics, eyewear |
PET | 260°C - 290°C | Bottles, food packaging |
ABS | 210°C - 250°C | Automotive, consumer goods |
Polystyrene (PS) | 180°C - 240°C | Disposable cutlery, toys |
Need help determining the right temperature for your plastic molding process? Contact our experts today for tailored advice!