Annealing and normalizing are both heat treatment processes used to alter the microstructure and properties of materials, particularly metals. The choice between annealing and normalizing depends on the desired outcome and specific application requirements. Annealing involves heating the material past its recrystallization temperature and then cooling it slowly in a controlled environment, which reduces hardness, increases ductility, and relieves internal stresses. Normalizing, on the other hand, also involves heating the material past its recrystallization temperature but allows it to cool at room temperature, resulting in a harder and stronger material compared to annealing. While annealing provides better ductility and stress relief, normalizing is more cost-effective and suitable for applications requiring improved strength and uniformity.
Key Points Explained:
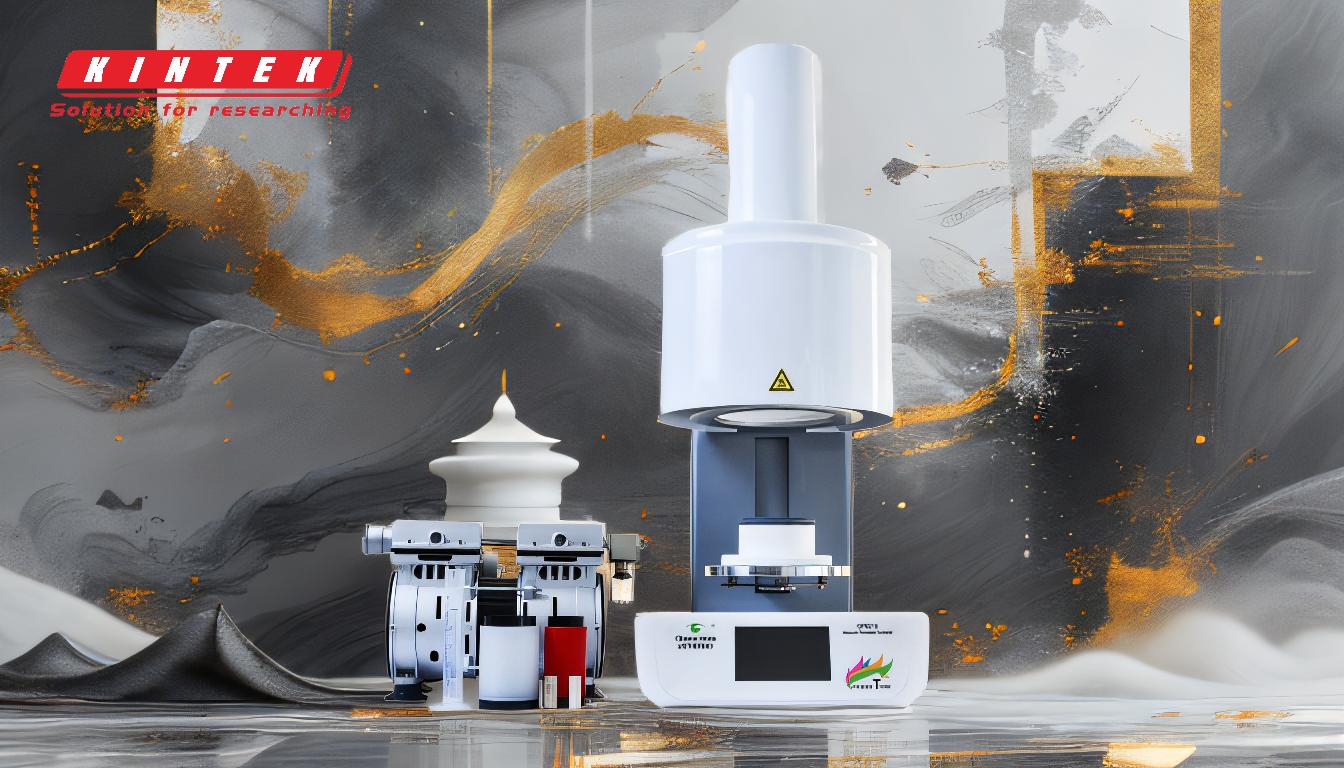
-
Purpose of Annealing and Normalizing:
- Annealing: Primarily used to soften materials, increase ductility, and relieve internal stresses. It is ideal for improving machinability and preparing materials for further processing.
- Normalizing: Used to refine the grain structure, improve mechanical properties, and achieve uniformity in the material. It is often employed to enhance strength and toughness.
-
Heating Process:
- Both processes involve heating the material above its recrystallization temperature. This allows the material's microstructure to reorganize, leading to changes in its mechanical properties.
-
Cooling Methods:
- Annealing: The material is cooled slowly in a controlled environment, typically inside an annealing furnace. This slow cooling process allows for the formation of a more uniform and softer microstructure.
- Normalizing: The material is cooled at room temperature, which results in faster cooling. This leads to a finer grain structure and increased hardness compared to annealing.
-
Effect on Material Properties:
- Annealing: Reduces hardness and increases ductility, making the material easier to work with. It also relieves internal stresses, which can improve the material's performance in certain applications.
- Normalizing: Increases hardness and strength while maintaining a reasonable level of ductility. It also improves the material's uniformity and resistance to deformation.
-
Energy and Cost Considerations:
- Annealing: Requires more energy due to the controlled cooling process, making it more expensive. However, it is necessary for applications where maximum ductility and stress relief are required.
- Normalizing: Less energy-intensive since it relies on natural cooling, making it a more cost-effective option. It is suitable for applications where improved strength and uniformity are more critical than maximum ductility.
-
Applications:
- Annealing: Commonly used in the manufacturing of components that require high levels of machinability, such as gears, bearings, and tools. It is also used in the production of wires and sheets where ductility is essential.
- Normalizing: Often used in the production of structural components, such as beams and plates, where strength and uniformity are important. It is also used in the automotive and construction industries.
-
Material Suitability:
- Annealing: Best suited for materials that need to be softened or have internal stresses relieved, such as low-carbon steels and non-ferrous metals.
- Normalizing: More appropriate for materials that require enhanced mechanical properties, such as medium to high-carbon steels.
In conclusion, the choice between annealing and normalizing depends on the specific requirements of the application. Annealing is better for achieving maximum ductility and stress relief, while normalizing is more cost-effective and suitable for applications requiring improved strength and uniformity. Both processes have their unique advantages and are chosen based on the desired outcome and material properties.
Summary Table:
Aspect | Annealing | Normalizing |
---|---|---|
Purpose | Softens materials, increases ductility, relieves internal stresses | Refines grain structure, improves strength, and achieves uniformity |
Cooling Method | Slow cooling in a controlled environment | Cooling at room temperature |
Effect on Properties | Reduces hardness, increases ductility, relieves stress | Increases hardness and strength, maintains ductility |
Cost | More expensive due to controlled cooling | More cost-effective due to natural cooling |
Applications | Gears, bearings, tools, wires, and sheets | Structural components, automotive, and construction industries |
Material Suitability | Low-carbon steels, non-ferrous metals | Medium to high-carbon steels |
Need help choosing the right heat treatment process? Contact our experts today for personalized advice!