High-temperature furnaces are essential for industrial and laboratory applications requiring extreme heat. Among these, electric furnaces stand out for their ability to generate the highest temperatures, with industrial arc furnaces reaching over 1800°C and laboratory units exceeding 3000°C. Other types of high-temperature furnaces include tube furnaces, vacuum furnaces, box furnaces, and muffle furnaces, each designed for specific applications. These furnaces are equipped with advanced heating elements and precise temperature control systems, making them ideal for processes like fusion, sintering, melting, and testing. The choice of furnace depends on the required temperature range, uniformity, and application-specific needs.
Key Points Explained:
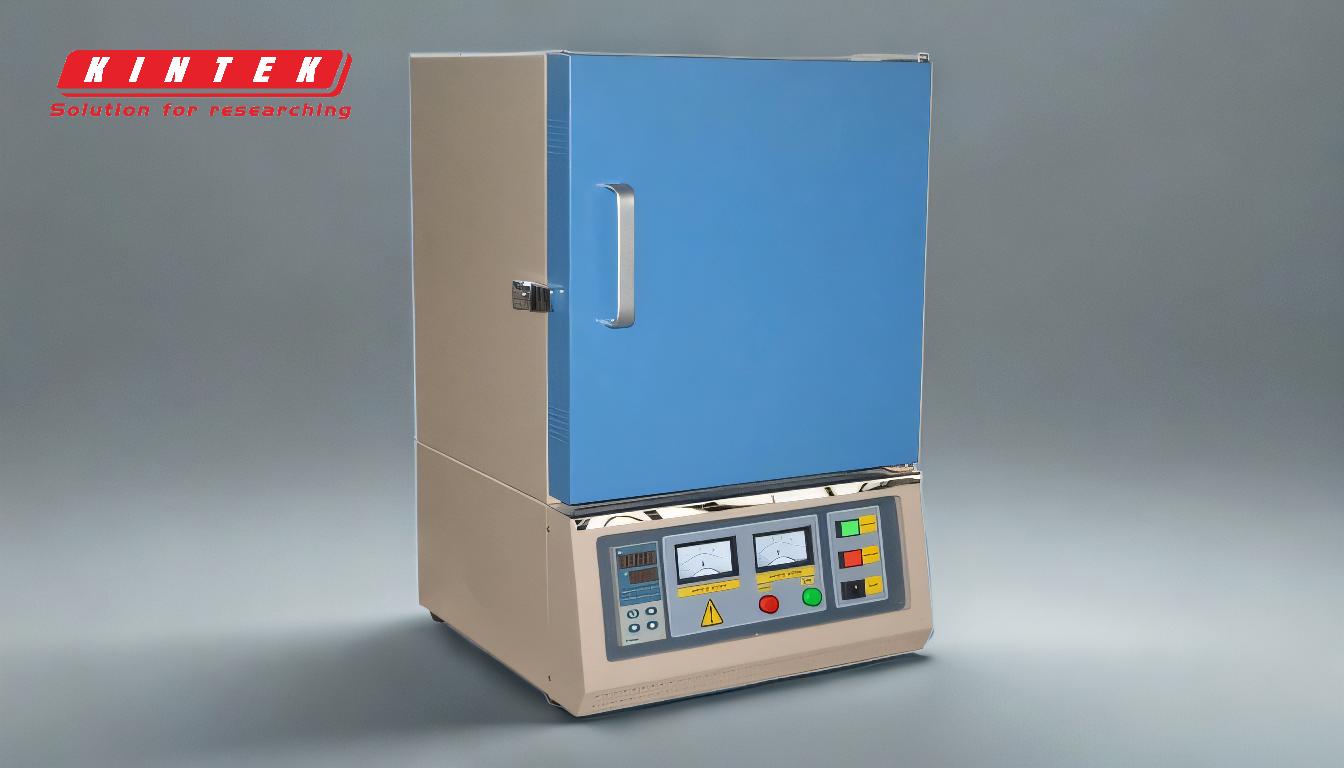
-
Electric Furnaces:
- Highest Temperature Capability: Electric furnaces, particularly industrial arc furnaces, can generate temperatures exceeding 1800°C, while specialized laboratory units can reach over 3000°C.
- Power Source: They rely on a constant supply of electricity, which ensures consistent and controllable heat output.
- Applications: Ideal for processes requiring extreme heat, such as metal melting, glass manufacturing, and advanced material testing.
-
High-Temperature Furnaces:
- Definition: High-temperature furnaces, also known as industrial furnaces, are designed to achieve higher temperatures than standard furnaces.
- Heating Elements: These furnaces feature radiant heating elements within a heat chamber, providing excellent temperature control and uniformity.
- Applications: Commonly used in processes like fusion, sintering, and high-temperature testing.
-
Types of High-Temperature Furnaces:
-
Tube Furnaces:
- Design: Cylindrical heating chamber with heating elements positioned around the tube.
- Temperature Range: Capable of reaching high temperatures, suitable for continuous processes.
- Applications: Used in material research, chemical vapor deposition, and thermal treatment of samples.
-
Vacuum Furnaces:
- Design: Operates in a vacuum environment to prevent oxidation and contamination.
- Temperature Range: High-temperature capabilities, often used in conjunction with inert gases.
- Applications: Ideal for processes like brazing, sintering, and heat treatment of metals in a controlled atmosphere.
-
Box Furnaces:
- Design: Rectangular heating chamber with heating elements on all sides.
- Temperature Range: Can achieve high temperatures with excellent uniformity.
- Applications: Suitable for batch processing, annealing, and curing of materials.
-
Muffle Furnaces:
- Design: Features a separate chamber (muffle) to isolate the heating elements from the sample.
- Temperature Range: High-temperature capabilities with precise control.
- Applications: Used in ashing, loss-on-ignition testing, and heat treatment of small samples.
-
Tube Furnaces:
-
Temperature Uniformity and Control:
- Importance: Uniform temperature distribution is critical for consistent results in high-temperature processes.
- Heating Element Placement: Strategically positioned heating elements ensure even heat distribution across the chamber.
- Control Systems: Advanced temperature control systems allow for precise regulation and monitoring of heat levels.
-
Applications of High-Temperature Furnaces:
- Industrial Applications: Metal processing, glass manufacturing, and ceramic production.
- Laboratory Applications: Material research, chemical synthesis, and thermal analysis.
- Specialized Processes: Fusion, sintering, melting, and high-temperature testing.
-
Selection Criteria:
- Temperature Requirements: Choose a furnace based on the maximum temperature needed for the application.
- Uniformity and Control: Consider the level of temperature control and uniformity required.
- Atmosphere Control: For processes sensitive to oxidation or contamination, vacuum or inert atmosphere furnaces are preferable.
- Sample Size and Type: The size and nature of the samples will influence the choice between tube, box, or muffle furnaces.
In conclusion, electric furnaces are the top choice for achieving the highest temperatures, while other high-temperature furnaces like tube, vacuum, box, and muffle furnaces offer specialized features for various industrial and laboratory applications. The selection of the appropriate furnace depends on the specific temperature requirements, process needs, and sample characteristics.
Summary Table:
Furnace Type | Key Features | Applications |
---|---|---|
Electric | Highest temperatures (up to 3000°C), precise control, consistent heat output | Metal melting, glass manufacturing, advanced material testing |
Tube | Cylindrical design, high-temperature range, continuous processes | Material research, chemical vapor deposition, thermal treatment |
Vacuum | Operates in a vacuum, prevents oxidation, inert gas compatibility | Brazing, sintering, heat treatment in controlled atmospheres |
Box | Rectangular chamber, high uniformity, batch processing | Annealing, curing, batch processing of materials |
Muffle | Separate chamber for sample isolation, precise temperature control | Ashing, loss-on-ignition testing, heat treatment of small samples |
Need help choosing the right high-temperature furnace? Contact our experts today!