Thin-film deposition processes, such as Physical Vapor Deposition (PVD) or Chemical Vapor Deposition (CVD), require a vacuum environment to ensure high-quality, pure, and defect-free films. The vacuum serves multiple critical purposes, including reducing contamination, enabling controlled particle movement, and facilitating precise material deposition. By creating a low-pressure environment, the vacuum minimizes unwanted interactions between vaporized atoms and residual gases, ensuring that the deposited film adheres well and maintains its desired properties. This is particularly vital in industries like semiconductor manufacturing, where even microscopic impurities can compromise product performance.
Key Points Explained:
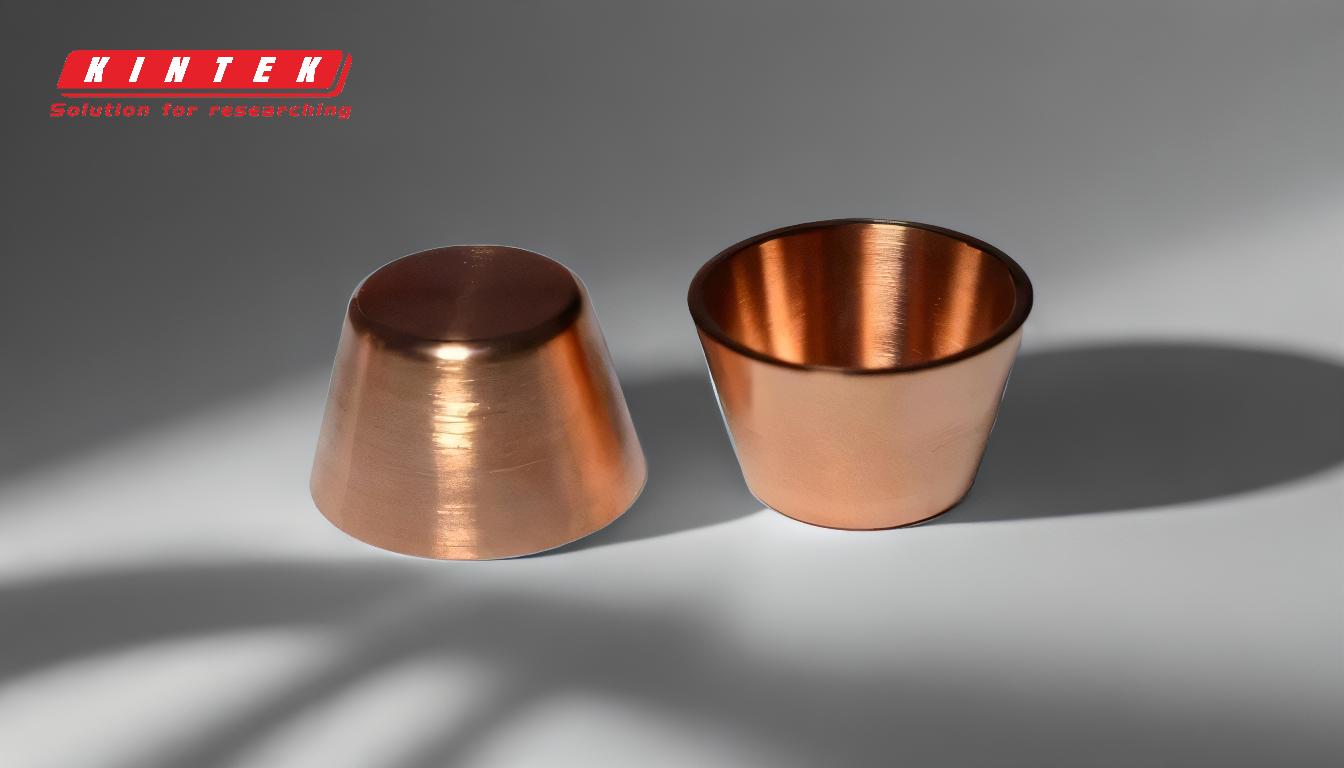
-
Reduction of Contamination:
- A vacuum environment significantly lowers the presence of impurities such as oxygen, nitrogen, carbon dioxide, and other gases that can react with the film material.
- These contaminants can weaken the film's adhesiveness, alter its chemical composition, or cause defects like oxidation or nitride formation.
- For example, in microchip manufacturing, even trace amounts of impurities can lead to circuit failures, making a high vacuum essential for maintaining purity.
-
Long Mean-Free Path for Vaporized Atoms:
- In a vacuum, the gas pressure is reduced, allowing vaporized atoms to travel longer distances without colliding with other particles.
- This long mean-free path ensures that the atoms reach the substrate uniformly, preventing nucleation in the vapor phase, which could otherwise form soot or uneven deposits.
- A controlled mean-free path is critical for achieving uniform film thickness and consistent material properties.
-
Control of Gas and Vapor Composition:
- A vacuum environment enables precise control over the composition of gases and vapors in the deposition chamber.
- This control is essential for processes like CVD, where specific chemical reactions are required to form the desired film.
- By minimizing unwanted gases, the vacuum ensures that only the intended reactions occur, leading to high-quality films.
-
Low-Pressure Plasma Environment:
- Many thin-film deposition techniques, such as sputtering, rely on plasma generation within the vacuum chamber.
- A low-pressure environment is necessary to sustain the plasma and ensure efficient ionization of the target material.
- This plasma environment enhances the energy and directionality of the vaporized atoms, improving film adhesion and density.
-
Thermal Evaporation Efficiency:
- In thermal evaporation processes, a vacuum reduces the density of atoms in the chamber, allowing for higher evaporation rates.
- Without a vacuum, the presence of air molecules would absorb energy from the evaporating material, reducing efficiency and potentially altering the film's properties.
- A high vacuum ensures that the material evaporates cleanly and deposits uniformly on the substrate.
-
Minimization of Gaseous Contamination:
- A vacuum environment minimizes the density of undesirable atoms, such as those from residual gases, which could otherwise incorporate into the film.
- This is particularly important for applications requiring high-purity films, such as optical coatings or semiconductor layers.
- By reducing gaseous contamination, the vacuum ensures that the film's optical, electrical, or mechanical properties meet stringent requirements.
-
Mass Flow Control:
- A vacuum allows for precise control of mass flow into the processing chamber, ensuring that the correct amount of material is deposited.
- This control is critical for achieving the desired film thickness and uniformity, especially in multi-layer deposition processes.
- Without a vacuum, fluctuations in gas pressure could lead to inconsistent film quality.
-
Applications Requiring High Vacuum:
- Industries such as semiconductor manufacturing, optical coating, and data storage (e.g., CDs and DVDs) rely on high-vacuum environments to produce defect-free products.
- In these applications, even nanometer-scale defects can render the product unusable, making a vacuum indispensable for maintaining quality and performance.
In summary, a vacuum is essential for thin-film deposition because it creates a controlled, contaminant-free environment that enables precise material deposition, uniform film formation, and high-quality results. Whether for microelectronics, optics, or data storage, the vacuum ensures that the deposited films meet the stringent requirements of modern technology.
Summary Table:
Key Benefit | Explanation |
---|---|
Reduction of Contamination | Minimizes impurities like oxygen and nitrogen, ensuring film purity. |
Long Mean-Free Path | Allows uniform atom travel, preventing uneven deposits. |
Control of Gas Composition | Ensures precise chemical reactions for high-quality films. |
Low-Pressure Plasma | Enhances plasma generation for better film adhesion and density. |
Thermal Evaporation Efficiency | Increases evaporation rates and ensures uniform deposition. |
Minimization of Gaseous Contamination | Reduces residual gases for high-purity films. |
Mass Flow Control | Enables precise material deposition for consistent film thickness. |
Applications | Vital for semiconductors, optical coatings, and data storage. |
Need a vacuum solution for thin-film deposition? Contact our experts today to ensure high-quality results!