Cold working and hot working are two fundamental metal-forming processes, each with distinct advantages and disadvantages. Cold working, performed below the recrystallization temperature of the metal, offers several benefits over hot working, which occurs above this temperature. These benefits include improved mechanical properties, better surface finish, tighter dimensional tolerances, and reduced material waste. However, cold working also has limitations, such as increased deformation resistance and the need for intermediate annealing in some cases. Understanding the differences between these processes helps in selecting the appropriate method for specific applications.
Key Points Explained:
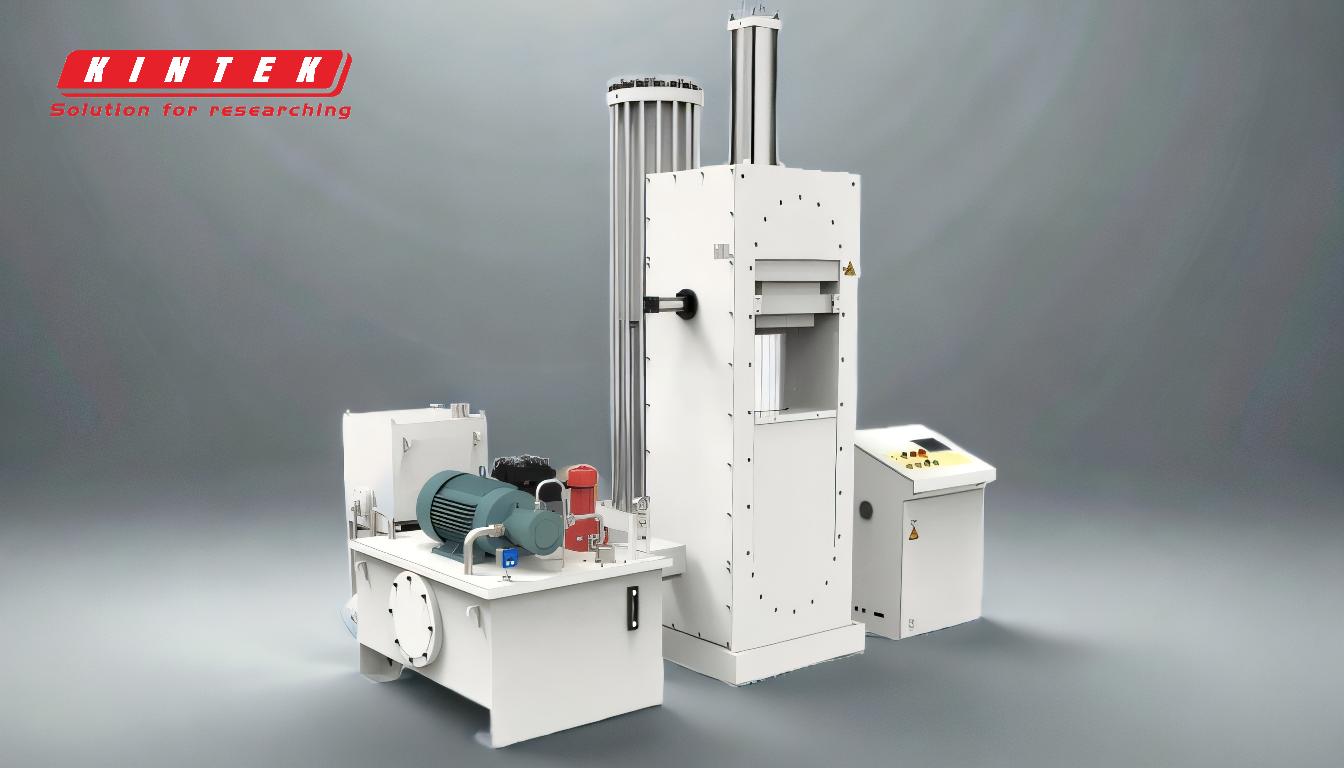
-
Improved Mechanical Properties:
- Cold working enhances the mechanical properties of metals, such as strength and hardness, due to strain hardening. This process involves the dislocation of metal atoms, which increases resistance to further deformation.
- Hot working, on the other hand, does not significantly improve mechanical properties because the metal recrystallizes during the process, eliminating strain hardening effects.
-
Better Surface Finish:
- Cold working produces a smoother and more precise surface finish compared to hot working. This is because cold working avoids oxidation and scale formation, which are common in hot working processes.
- The absence of high temperatures in cold working also reduces the risk of surface defects, making it ideal for applications requiring high-quality finishes.
-
Tighter Dimensional Tolerances:
- Cold working allows for tighter dimensional control, as the metal does not expand or contract significantly during the process. This precision is crucial for manufacturing components with strict dimensional requirements.
- Hot working, due to thermal expansion and contraction, often results in less precise dimensions, requiring additional machining or finishing steps.
-
Reduced Material Waste:
- Cold working minimizes material waste because it does not involve high temperatures that can lead to oxidation and scaling. This efficiency is particularly beneficial for expensive or scarce materials.
- Hot working, while capable of producing large deformations, often results in material loss due to oxidation and scaling, increasing overall production costs.
-
Limitations of Cold Working:
- Despite its advantages, cold working has limitations, such as higher deformation resistance, which necessitates more powerful equipment. Additionally, some metals may require intermediate annealing to restore ductility and prevent cracking.
- Hot working, while less precise, is better suited for shaping large or complex parts that require significant deformation.
In summary, cold working is often preferred over hot working for applications requiring high strength, precision, and surface quality. However, the choice between these processes depends on the specific requirements of the application, including material properties, desired dimensions, and production constraints.
Summary Table:
Aspect | Cold Working | Hot Working |
---|---|---|
Mechanical Properties | Enhances strength and hardness through strain hardening. | Does not significantly improve mechanical properties due to recrystallization. |
Surface Finish | Smoother and more precise; avoids oxidation and scaling. | Prone to oxidation and scaling, resulting in a rougher finish. |
Dimensional Tolerances | Tighter control; minimal expansion or contraction. | Less precise due to thermal expansion and contraction. |
Material Waste | Reduced waste; no oxidation or scaling. | Higher waste due to oxidation and scaling. |
Limitations | Higher deformation resistance; may require intermediate annealing. | Better for large or complex parts requiring significant deformation. |
Need help choosing the right metal-forming process for your application? Contact our experts today!