Physical Vapor Deposition (PVD) is conducted at low pressure primarily to create a controlled and clean environment that ensures the efficient transfer of material from the source to the substrate. Low pressure minimizes unwanted gas phase reactions, reduces contamination, and increases the uniformity of the deposited material. It also allows for a longer mean free path of atoms, enabling higher energy transfer and better adhesion of the material to the substrate. Additionally, a vacuum environment is crucial for applications requiring high precision, such as microchip manufacturing, where even minor contaminants can cause significant defects.
Key Points Explained:
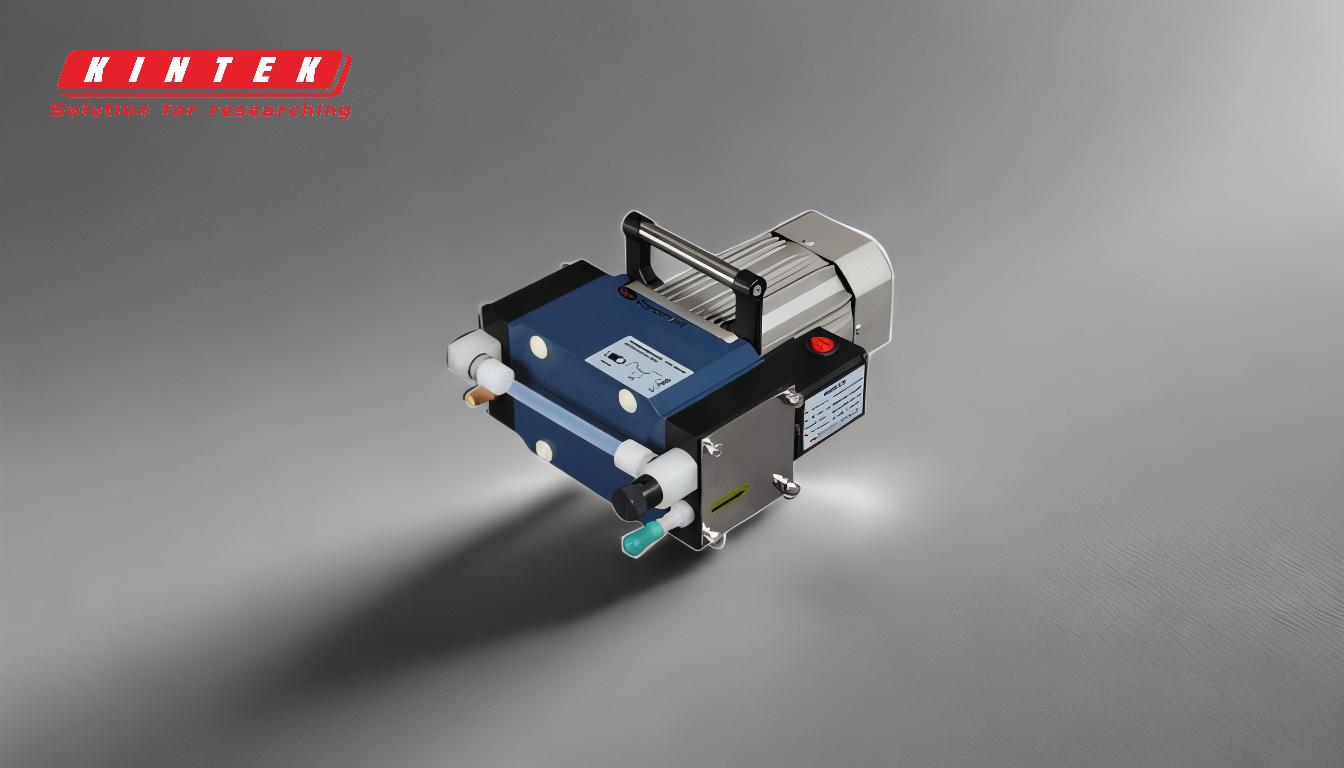
-
Minimization of Unwanted Gas Phase Reactions:
- Low pressure reduces the likelihood of unwanted chemical reactions between the vaporized material and residual gases in the chamber.
- This ensures that the deposited material remains pure and adheres to the substrate without forming unintended compounds.
-
Increased Uniformity Across the Substrate:
- A low-pressure environment allows for a more uniform distribution of the vaporized material across the substrate.
- This uniformity is critical for applications requiring consistent thickness and properties, such as in semiconductor manufacturing.
-
Enhanced Material Transfer and Adhesion:
- In a vacuum, the vaporized material encounters less resistance from air or other gases, allowing it to travel more efficiently to the substrate.
- The increased energy of the particles results in stronger adhesion to the substrate, improving the durability and quality of the coating.
-
Reduction of Contamination:
- A high vacuum environment minimizes the presence of contaminants, such as dust or moisture, which can adversely affect the quality of the deposition.
- This is particularly important in industries like microelectronics, where even tiny particles can lead to significant defects.
-
Controlled and Repeatable Deposition Process:
- Low pressure provides a stable and predictable environment, enabling precise control over the deposition process.
- This repeatability is essential for producing consistent results in high-precision applications.
-
Longer Mean Free Path of Atoms:
- In a vacuum, the mean free path of atoms (the average distance an atom travels before colliding with another atom) is significantly increased.
- This allows atoms to travel directly to the substrate without being scattered, ensuring a more efficient and directed deposition process.
-
High Thermal Evaporation Rate:
- Low pressure facilitates a higher rate of thermal evaporation, which is necessary for vaporizing the source material.
- This ensures that the material is efficiently transferred to the substrate in a timely manner.
-
Prevention of Gaseous Contamination:
- By maintaining a low-pressure environment, the density of undesirable atoms or molecules is minimized.
- This reduces the risk of incorporating impurities into the deposited material, ensuring a cleaner and higher-quality coating.
-
Flexibility in Initiating Chemical Reactions:
- While PVD typically avoids chemical reactions, the introduction of reactive gases (like oxygen) in a controlled manner can be used to create specific coatings, such as oxides.
- This flexibility allows for the customization of material properties to meet specific application requirements.
-
Critical for High-Precision Applications:
- Industries such as microelectronics, optics, and data storage (e.g., CDs, DVDs) require extremely clean and controlled environments to produce defect-free products.
- The low-pressure conditions in PVD are essential for meeting the stringent quality standards of these industries.
By understanding these key points, it becomes clear why low pressure is a fundamental requirement for successful PVD processes. It ensures high-quality, uniform, and contamination-free coatings, which are essential for a wide range of industrial applications.
Summary Table:
Key Benefit | Explanation |
---|---|
Minimized Gas Phase Reactions | Reduces unwanted chemical reactions, ensuring pure material deposition. |
Uniform Coating Distribution | Ensures consistent thickness and properties across the substrate. |
Enhanced Material Adhesion | Increases particle energy for stronger, more durable coatings. |
Reduced Contamination | Minimizes dust, moisture, and impurities for cleaner coatings. |
Controlled Deposition Process | Provides a stable environment for repeatable, high-precision results. |
Longer Mean Free Path of Atoms | Allows efficient, direct material transfer to the substrate. |
High Thermal Evaporation Rate | Facilitates faster vaporization and material transfer. |
Prevention of Gaseous Contamination | Reduces impurities, ensuring high-quality coatings. |
Flexibility in Chemical Reactions | Enables customization of coatings with reactive gases. |
Critical for High-Precision Applications | Essential for industries like microelectronics and optics requiring defect-free products. |
Need a PVD solution tailored to your needs? Contact our experts today to learn more!