A vacuum furnace is a highly specialized piece of equipment designed to heat materials in a vacuum environment, offering numerous advantages over traditional furnaces. Its primary benefits include the prevention of oxidation and contamination, precise temperature control, uniform heating, rapid cooling, and environmental friendliness. These features make it ideal for advanced heat treatment processes, particularly in industries requiring high-quality, contamination-free results. Vacuum furnaces are energy-efficient, programmable, and capable of achieving extremely high temperatures, making them a cornerstone of modern industrial heat treatment.
Key Points Explained:
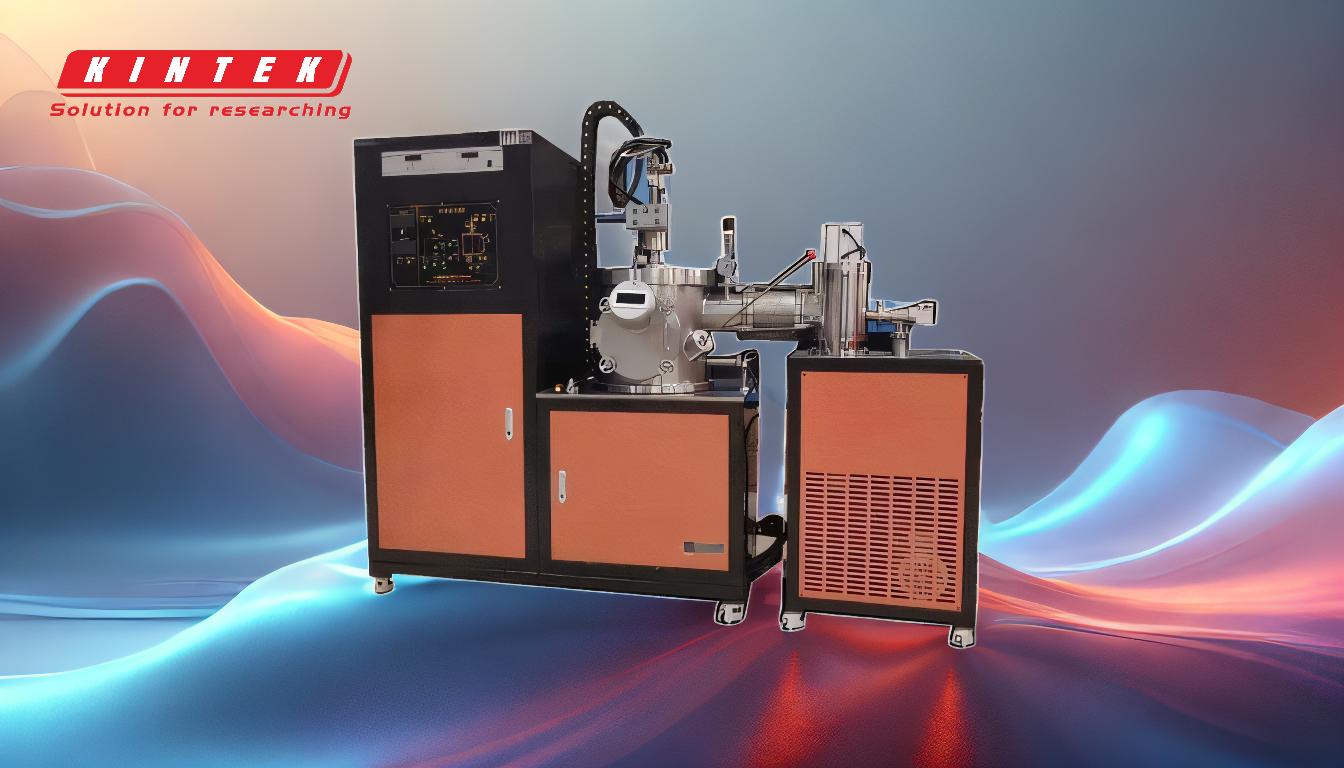
-
Prevention of Oxidation and Contamination
- The vacuum environment eliminates air and gases, preventing oxidation and decarburization of materials.
- This ensures a clean, bright, and contamination-free surface on the product, which is critical for high-precision applications like aerospace and medical devices.
- The absence of reactive gases like oxygen and carbon minimizes surface defects and improves material integrity.
-
Precise Temperature Control
- Vacuum furnaces offer highly accurate temperature control within a small heating zone.
- This precision is essential for achieving consistent metallurgical properties and repeatable results in heat treatment processes.
- Computer-controlled systems allow for programmable operations, reducing human error and ensuring process consistency.
-
Uniform Temperature Distribution
- Heat transfer in vacuum furnaces occurs primarily through radiation, ensuring uniform heating across the product.
- This uniformity is critical for processes like annealing, brazing, and sintering, where inconsistent temperatures can lead to defects.
- The ability to maintain uniform temperatures over a wide range (800–3,000°C or 1,500–5,400°F) makes vacuum furnaces versatile for various applications.
-
Rapid Cooling (Quenching)
- Vacuum furnaces can achieve quick cooling rates, which are essential for processes like quenching.
- Rapid cooling helps shorten process cycle times, improving efficiency and productivity.
- This feature is particularly beneficial for hardening metals and alloys without compromising their structural integrity.
-
Environmental Friendliness
- Vacuum furnaces do not emit waste gases or water during operation, making them environmentally friendly.
- They align with modern industrial green requirements, reducing the carbon footprint of heat treatment processes.
- The absence of harmful emissions also improves workplace safety and reduces the need for additional pollution control equipment.
-
Energy Efficiency and Resource Savings
- Vacuum furnaces are designed to minimize energy consumption while delivering high operating power.
- Their efficient design prevents excessive power usage, making them cost-effective in the long run.
- High electromechanical integration further reduces resource waste, contributing to sustainable manufacturing practices.
-
Versatility in High-Temperature Applications
- Vacuum furnaces can achieve extremely high temperatures and pressures, making them suitable for advanced heat treatment processes.
- They are widely used in industries such as aerospace, automotive, electronics, and medical device manufacturing.
- Their ability to handle a wide range of materials and processes makes them indispensable in modern industrial settings.
-
Metallurgical Repeatability
- The computer-controlled processes in vacuum furnaces ensure consistent and repeatable results.
- This repeatability is crucial for maintaining product quality and meeting stringent industry standards.
- It also reduces the risk of defects and rework, saving time and resources.
In summary, vacuum furnaces are a superior choice for heat treatment due to their ability to prevent contamination, provide precise and uniform heating, and offer rapid cooling capabilities. Their environmental benefits, energy efficiency, and versatility make them a vital tool in modern manufacturing, ensuring high-quality results while meeting sustainability goals.
Summary Table:
Advantage | Key Benefit |
---|---|
Prevention of Oxidation | Eliminates air and gases, ensuring contamination-free surfaces. |
Precise Temperature Control | Accurate heating for consistent metallurgical properties. |
Uniform Heating | Ensures even temperature distribution for defect-free results. |
Rapid Cooling (Quenching) | Shortens process cycles and improves efficiency. |
Environmental Friendliness | No harmful emissions, aligning with green manufacturing practices. |
Energy Efficiency | Minimizes power usage while delivering high performance. |
Versatility | Suitable for high-temperature applications across industries. |
Metallurgical Repeatability | Ensures consistent, high-quality results with computer-controlled processes. |
Upgrade your heat treatment processes with a vacuum furnace—contact us today to learn more!