The Evolution of Isostatic Pressing Process
Table of Contents
- The Evolution of Isostatic Pressing Process
- The origin of isostatic pressing process in the mid-1950's
- Transition from a research curiosity to a viable production tool
- Wide application in industries for consolidation of powders or defect healing of castings
- Used for a range of materials including ceramics, metals, composites, plastics, and carbon
- Working Principle of Isostatic Pressing
- Types of Isostatic Pressing
- Isostatic Pressing in Pharmaceutical Industry
- Operational Mechanism of Isostatic Press
- Advantages of Isostatic Press
- Working of Isostatic Press
- Common Applications of Isostatic Press
The origin of isostatic pressing process in the mid-1950's
The isostatic pressing process was pioneered in the mid-1950s and has steadily grown from a research curiosity to a viable production tool.
Transition from a research curiosity to a viable production tool
Many industries apply this technique for the consolidation of powders or defect healing of castings. The process is used for a range of materials, including ceramics, metals, composites, plastics, and carbon.
Wide application in industries for consolidation of powders or defect healing of castings
Isostatic pressing applies a uniform, equal force over the entire product, regardless of shape or size. It thus offers unique benefits for ceramic and refractory applications. The ability to form product shapes to precise tolerances (reducing costly machining) has been a major driving force for its commercial development.
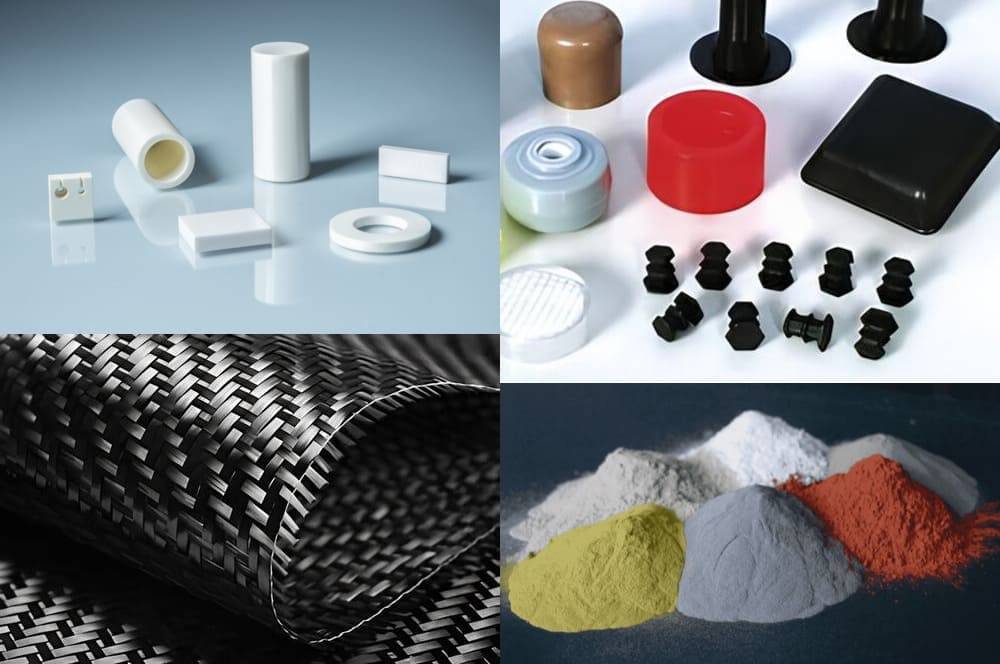
Used for a range of materials including ceramics, metals, composites, plastics, and carbon
The isostatic pressing process is used for a range of materials, including ceramics, metals, composites, plastics, and carbon. It has found wide application in industries for the consolidation of powders or defect healing of castings. This process offers unique benefits for ceramic and refractory applications, allowing for the formation of product shapes to precise tolerances and reducing the need for costly machining.
Working Principle of Isostatic Pressing
Isostatic pressing is a process that applies a uniform, equal force over the entire product, regardless of its shape or size. This technique has become widely used in various industries, including ceramics, metals, composites, plastics, and carbon.
Uniform, equal force application over the entire product
Isostatic pressing offers unique benefits for ceramic and refractory applications. By applying the same pressure from all directions, it ensures that the force is distributed evenly throughout the product. This uniform force application helps in reducing porosity and achieving high and uniform density in the final product.
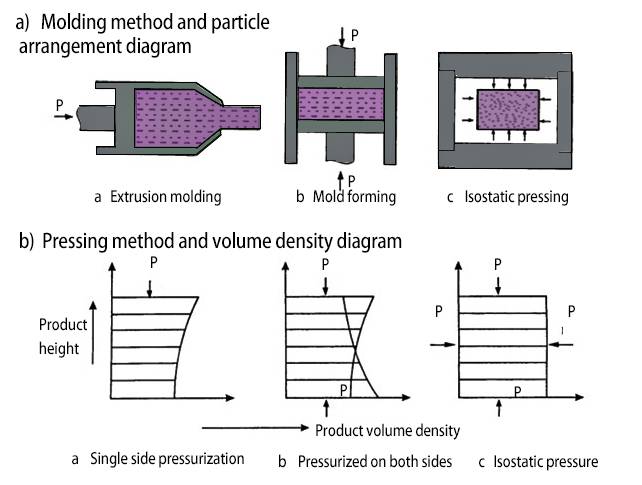
Ability to form product shapes to precise tolerances
One of the major advantages of isostatic pressing is its ability to form product shapes to precise tolerances. Unlike other forming processes, isostatic pressing removes many of the constraints that limit the geometry of parts compacted unidirectionally in rigid dies. This reduces the need for costly machining operations, resulting in cost savings and improved efficiency.
Predominant use for ceramic and refractory applications
Isostatic pressing has found predominant use in ceramic and refractory applications. The process allows for the consolidation of powders and defect healing of castings. It is particularly suitable for difficult-to-compact and expensive materials such as superalloys, titanium, tool steels, stainless steel, and beryllium. Isostatic pressing ensures highly efficient material utilization, leading to cost-effective production.
In summary, isostatic pressing is a versatile process that applies uniform, equal force over the entire product, allowing for the production of materials with precise tolerances. It has become an essential technique in industries requiring high-quality and cost-effective manufacturing of ceramic and refractory products.
Types of Isostatic Pressing
Cold Isostatic Pressing (CIP) for consolidating ceramic or refractory powders
Cold Isostatic Pressing (CIP) is a powder-compacting process used to consolidate ceramic or refractory powders. In this process, the powders are loaded into elastomeric bags and subjected to equal pressure from all directions. CIP is mainly used to obtain parts that are 60 to 80% theoretically dense and ready for sintering. The good green strength obtained with CIP allows for premachining before sintering without causing breakage.
Warm Isostatic Pressing (WIP) pressed at warm temperature up to 100°C
Warm Isostatic Pressing (WIP) is a variant of Cold Isostatic Pressing (CIP) that involves pressing shapes at warm temperatures, typically up to 100°C. WIP utilizes warm water or a similar medium to apply uniform pressure to powdered products from all directions. This cutting-edge technology enables isostatic pressing at temperatures that do not exceed the boiling point of the liquid medium. Flexible materials are used as a jacket mold, and hydraulic pressure is applied as a pressure medium to shape and press the powder material.
The WIP process typically involves heating the liquid medium first and continuously injecting it into a sealed pressing cylinder through a booster source. To ensure precise temperature control, the pressing cylinder is equipped with a heating element.
Hot Isostatic Pressing (HIP) for obtaining fully dense parts with temperature and pressure applied simultaneously
Hot Isostatic Pressing (HIP) is a process that involves applying high temperature and high pressure simultaneously to obtain fully dense parts. HIP is used mainly for engineered ceramics that require optimum properties for high-performance applications. In the HIP process, the material is heated in an inert gas, usually argon, which applies "isostatic" pressure uniformly in all directions. This causes voids to collapse under the differential pressure, effectively eliminating defects and achieving near theoretical density. HIP improves the mechanical properties of the parts, such as investment castings, by eliminating internal microporosity.
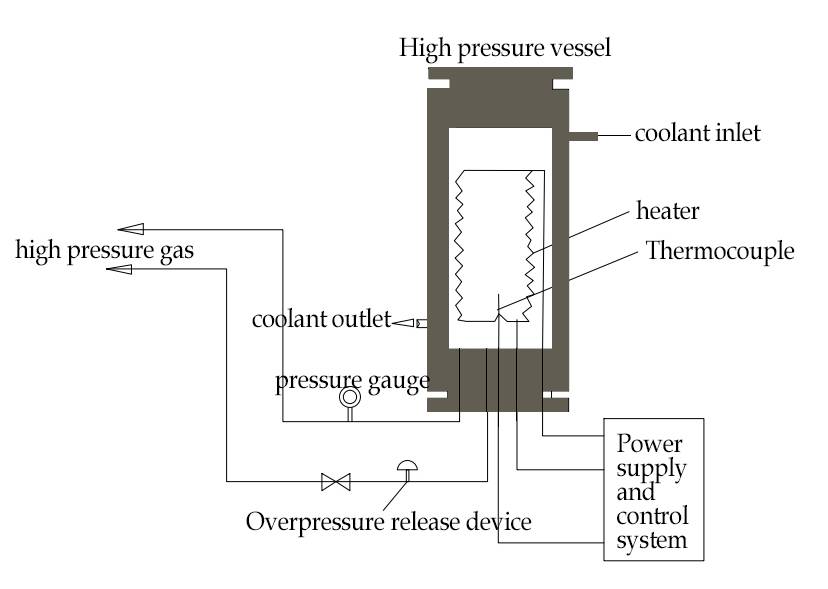
Hot isostatic pressing equipment consists of a high-pressure vessel, heating furnace, compressor, vacuum pump, storage tank, cooling system, and computer control system. The high-pressure vessel is the key device of the whole equipment.
Isostatic pressing, whether it is Cold Isostatic Pressing (CIP), Warm Isostatic Pressing (WIP), or Hot Isostatic Pressing (HIP), offers unique benefits for various industries. It allows for the consolidation of powders, defect healing of castings, and the production of fully dense parts with precise tolerances. This process is used in industries such as ceramics, metals, composites, plastics, and carbon. Isostatic pressing is a versatile and effective technique that continues to evolve and find new applications in manufacturing and production processes.
Isostatic Pressing in Pharmaceutical Industry
Isostatic pressing is a widely used technique in the pharmaceutical industry for compressing pharmaceutical particles and raw materials into pre-determined shapes. This process ensures a uniform compaction pressure throughout the powder mass and a homogeneous density distribution in the final product.
Usage for compressing pharmaceutical particles and raw material into pre-determined shapes
Isostatic pressing is an effective method for shaping pharmaceutical particles and raw materials. It applies equal force over the entire product, regardless of shape or size. This uniform compaction pressure helps in achieving high and uniform density, without the need for any lubricant. As a result, the final product has consistent quality and performance.
Ensures uniform compaction pressure and homogeneous density distribution in the final product
One of the advantages of isostatic pressing is its ability to ensure uniform compaction pressure and homogeneous density distribution in the final product. This is achieved by applying the same pressure in all directions during the pressing process. As a result, the powder is compacted with consistency, leading to a product with uniform density throughout.
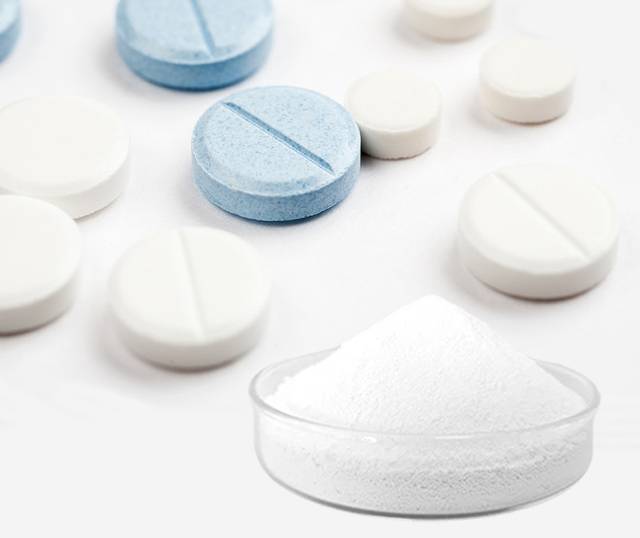
Isostatic pressing is widely used in the pharmaceutical industry due to its numerous advantages. It allows for the compression of difficult-to-compact and expensive materials such as superalloys, titanium, tool steels, stainless steel, and beryllium, with highly efficient material utilization. Additionally, it removes many of the constraints that limit the geometry of parts compacted unidirectionally in rigid dies.
The isostatic pressing process involves three basic types: cold isostatic pressing (CIP), warm isostatic pressing (WIP), and hot isostatic pressing (HIP). These types differ based on the temperature and pressure applied during the pressing process. While CIP is applied to consolidate ceramic or refractory powders loaded into elastomeric bags, WIP involves pressing shapes at warm temperatures. HIP, on the other hand, is used for engineered ceramics requiring optimum properties for high-performance applications.
In the pharmaceutical industry, isostatic presses are essential for achieving precise shapes and densities in pharmaceutical products. By using this pressurizing system, manufacturers can ensure a uniform compaction pressure throughout the powder mass, resulting in a final product with a homogeneous density distribution. Isostatic presses are one of the most widely used pharmaceutical processing machines.
Overall, isostatic pressing plays a crucial role in the pharmaceutical industry by providing a reliable and efficient method for compressing pharmaceutical particles and raw materials into pre-determined shapes. Its ability to ensure uniform compaction pressure and homogeneous density distribution makes it an indispensable tool for pharmaceutical manufacturing.
Operational Mechanism of Isostatic Press
Production of various types of materials from powder compacts by reducing porosity
Isostatic pressing is a process that allows for the production of various types of materials from powder compacts by reducing their porosity. This process involves the application of equal pressure from all directions to the compacted powder, resulting in optimal density and microstructure uniformity.
The powder mixture is first compacted and encapsulated using isostatic pressure. The press applies pressure equally from all directions, which helps to reduce porosity and increase the density of the powder compact. This uniform pressure distribution also eliminates die-wall friction, resulting in more uniform densities.
One of the advantages of isostatic pressing is the ability to achieve high and uniform density without the need for lubricants. This process is particularly useful for difficult-to-compact and expensive materials such as superalloys, titanium, tool steels, stainless steel, and beryllium. Isostatic pressing offers efficient material utilization and can produce parts with complex geometries.
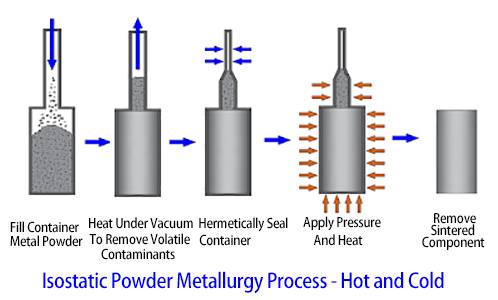
Compaction and encapsulation of powder mixture using isostatic pressure
Isostatic pressing involves the compaction and encapsulation of a powder mixture using isostatic pressure. The powder mixture is placed within a flexible membrane or hermetic container, which acts as a pressure barrier between the powder and the pressurizing medium.
The pressurizing medium can be a liquid or a gas, depending on the specific application. The pressure is applied equally from all directions, ensuring uniform compaction of the powder mixture. This process helps to reduce porosity and increase the density of the resulting material.
Isostatic pressing offers several advantages over other compaction methods. It allows for the production of parts with low distortion and consistent shrinkage during firing. It also enables the production of parts without the need for drying, and it allows for lower levels of binder in the powder. Additionally, isostatic pressing can be used to produce parts with internal shapes, threads, splines, serrations, and tapers.
Use of flexible membrane or hermetic container as pressure barrier
In isostatic pressing, a flexible membrane or hermetic container is used as a pressure barrier between the powder and the pressurizing medium. This barrier prevents the powder from escaping and ensures that the pressure is applied uniformly from all directions.
The flexible membrane or hermetic container is designed to withstand the pressure exerted during the pressing process. It acts as a barrier that separates the powder from the surrounding pressurizing medium, which can be a liquid or a gas.
The use of a flexible membrane or hermetic container allows for the application of equal pressure to the powder compact, resulting in uniform compaction and improved density. This mechanism is key to the success of isostatic pressing in producing materials with optimal properties.
Overall, the operational mechanism of isostatic press involves the production of various materials from powder compacts by reducing porosity through the compaction and encapsulation of the powder mixture using isostatic pressure. The use of a flexible membrane or hermetic container ensures the uniform application of pressure from all directions, resulting in high and uniform density. Isostatic pressing offers advantages such as the ability to produce parts with complex geometries and the efficient utilization of materials.
Advantages of Isostatic Press
Isostatic pressing offers several advantages over other manufacturing methods. Let's take a look at some of the key benefits:
Achievement of high and uniform density with same pressure in all directions
One of the main advantages of isostatic pressing is the ability to achieve high and uniform density in the compacted piece. This means that the resulting component will have consistent shrinkage during sintering or hot isostatic pressing, with little to no warpage. The powder is compacted with the same pressure in all directions, resulting in a high and uniform density.
Applicable to difficult-to-compact and expensive materials
Isostatic pressing is particularly suitable for difficult-to-compact and expensive materials such as superalloys, titanium, tool steels, stainless steel, and beryllium. These materials often pose challenges in terms of achieving high density and uniformity. However, with isostatic pressing, these materials can be efficiently compacted and utilized, resulting in high-quality components.
Efficient material utilization
Isostatic pressing enables highly efficient material utilization. The process removes many of the constraints that limit the geometry of parts compacted unidirectionally in rigid dies. This means that complex shapes and dimensions that are difficult or impossible to produce by other methods can be easily achieved through isostatic pressing. This ultimately leads to reduced material waste and increased cost-effectiveness.
Isostatic pressing offers a range of advantages, including uniform density, shape flexibility, component size adaptability, low tooling cost, enhanced alloying possibilities, reduced lead times, and cost savings in terms of material and machining. It is a versatile and efficient manufacturing method that finds applications in various industries, including pharmaceuticals, explosives, chemicals, food, nuclear fuel, and ferrites.
To better understand the working of isostatic press, let's take a look at how the process functions.
Working of Isostatic Press
Isostatic pressing is a process used to produce various types of materials from powder compacts by reducing the porosity of the powder mixture. The powder mixture is compacted and encapsulated using isostatic pressure, which is pressure equally applied from all directions. This is achieved by confining the metal powder within a flexible membrane or hermetic container, which acts as a pressure barrier between the powder and the pressurizing medium, which can be a liquid or gas.
The use of isostatic pressure allows for the achievement of high and uniform density in the compacted powder. Since no lubricant is needed in the process, the resulting density is consistent throughout the component. This makes isostatic pressing particularly effective in achieving high-quality components with uniform properties.
Isostatic pressing is a versatile and efficient manufacturing method that offers numerous advantages. It enables the achievement of high and uniform density, allows for the production of complex shapes and dimensions, and is applicable to difficult-to-compact and expensive materials. With its efficient material utilization and cost-effectiveness, isostatic pressing is a valuable technique in various industries.
Common Applications of Isostatic Press
Isostatic pressing is a versatile manufacturing process that is widely used in various industries. It offers several advantages over traditional compaction methods and can be applied to a range of materials. Let's explore some of the common applications of the isostatic press.
Pharmaceutical Industry
In the pharmaceutical industry, isostatic pressing is utilized for the production of tablets and other solid dosage forms. The process allows for the uniform compaction of powdered drugs, ensuring consistent drug release and efficacy. Isostatic pressing is particularly suitable for manufacturing complex-shaped tablets and achieving high-density compaction.
Explosives
Isostatic pressing plays a crucial role in the production of explosives. The process enables the precise shaping and compaction of explosive materials, ensuring uniformity and reliability. Isostatically pressed explosives exhibit improved performance characteristics, such as increased stability and enhanced detonation properties.
Chemicals
Isostatic pressing is employed in the chemical industry for the production of various chemical products and components. The process allows for the fabrication of complex-shaped parts with high density and uniformity. Isostatically pressed chemical components exhibit improved mechanical properties and chemical resistance.
Food Industry
Isostatic pressing finds applications in the food industry, particularly in food processing and preservation. The process is used for pasteurization and sterilization, where food products are subjected to uniform pressure from all directions. Isostatic pressing preserves the nutritional value, natural colorings, and flavorings of food products while deactivating microorganisms and enzymes.
Nuclear Fuel Ferrites
Isostatic pressing is employed in the production of nuclear fuel ferrites. The process allows for the fabrication of high-density, high-purity ferrite materials used as fuel pellets in nuclear reactors. Isostatically pressed nuclear fuel ferrites exhibit excellent thermal and mechanical properties, ensuring safe and efficient operation of nuclear power plants.
Other industries, such as aerospace, automotive, and electronics, also utilize isostatic pressing for various applications. The process enables the production of complex-shaped components with high precision and material efficiency. Isostatic pressing offers numerous advantages, including uniform compaction, efficient material utilization, and the ability to process difficult-to-compact materials like superalloys and titanium.
Both cold isostatic presses (CIP) and hot isostatic presses (HIP) are used in isostatic pressing. CIP operates at room temperature, while HIP functions at elevated temperatures. The choice of press depends on the specific requirements of the application.
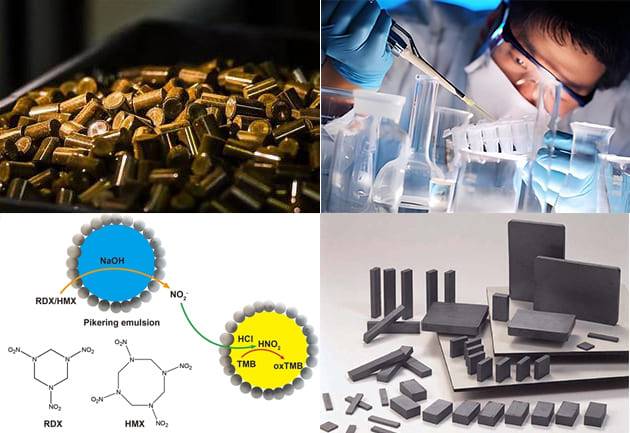
In conclusion, isostatic pressing is a versatile manufacturing process with a wide range of applications. It offers numerous advantages over traditional compaction methods and is utilized in industries such as pharmaceuticals, explosives, chemicals, food processing, and nuclear fuel production. Isostatic pressing enables the production of high-quality, complex-shaped components with uniform density and material efficiency.
If you are interested in this product you can browse our company website:https://kindle-tech.com/product-categories/isostatic-press, as an industry-leading laboratory equipment manufacturer, we are committed to providing the most advanced and high-quality laboratory equipment solutions. Whether you are engaged in scientific research, teaching or industrial production, our products will meet your needs for accurate and reliable laboratory equipment.
CONTACT US FOR A FREE CONSULTATION
KINTEK LAB SOLUTION's products and services have been recognized by customers around the world. Our staff will be happy to assist with any inquiry you might have. Contact us for a free consultation and talk to a product specialist to find the most suitable solution for your application needs!