Melting different metals in the same crucible is generally not recommended due to the risk of contamination, which can compromise the quality of the castings. The type of crucible used depends on the metal being melted, as each metal has specific requirements for temperature, chemical interaction, and thermal shock resistance. For instance, silicon carbide crucibles are ideal for copper-based alloys due to their high thermal shock resistance. Using the same crucible for multiple metals can lead to cross-contamination, making it difficult to achieve pure, high-quality melts. Therefore, it is best practice to use separate crucibles for different metals to ensure optimal results.
Key Points Explained:
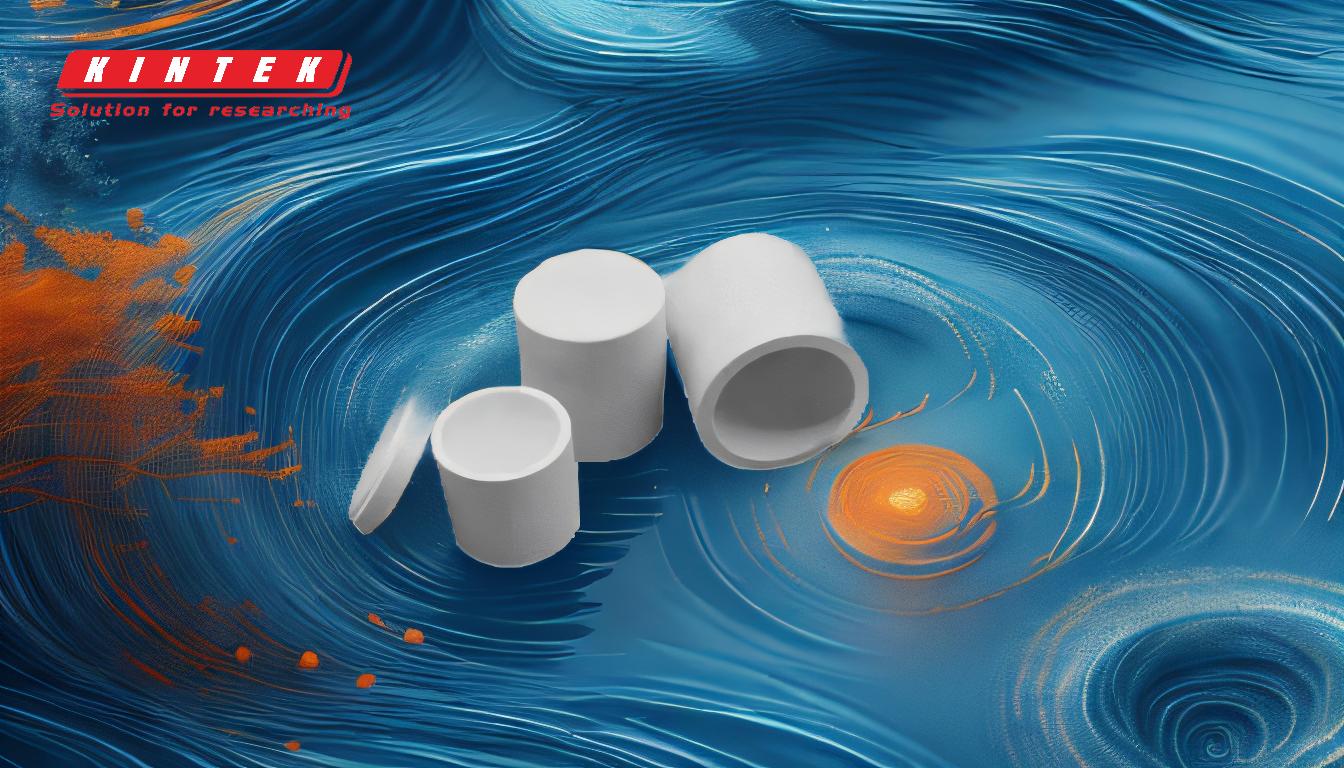
-
Risk of Contamination:
- Melting different metals in the same crucible can lead to contamination. Even trace amounts of one metal can significantly affect the properties of another metal.
- For example, melting aluminum after brass in the same crucible can introduce zinc or copper into the aluminum, altering its composition and potentially causing defects in the final casting.
-
Crucible Material Compatibility:
- Different metals require different crucible materials due to varying melting points and chemical interactions.
- Silicon carbide crucibles are often used for copper-based alloys because they can withstand high temperatures and resist thermal shock, whereas graphite crucibles might be better suited for aluminum.
-
Thermal and Chemical Resistance:
- The crucible must be able to withstand the maximum temperature required to melt the metal without degrading.
- Chemical resistance is crucial to prevent reactions between the crucible material and the molten metal, which could lead to contamination or crucible failure.
-
Thermal Shock Resistance:
- Some metals require rapid heating and cooling, necessitating a crucible with high thermal shock resistance.
- Silicon carbide crucibles are preferred for metals like copper and brass because they can handle rapid temperature changes without cracking.
-
Best Practices:
- Always use a separate crucible for each type of metal to avoid cross-contamination.
- Ensure the crucible is appropriately sized for the furnace and the amount of metal being melted.
- Regularly inspect crucibles for signs of wear or damage, as a compromised crucible can lead to contamination or even dangerous failures.
By adhering to these guidelines, you can ensure the purity and quality of your metal castings, avoiding the pitfalls of contamination and crucible failure.
Summary Table:
Key Consideration | Details |
---|---|
Risk of Contamination | Melting different metals in the same crucible can lead to cross-contamination. |
Crucible Material | Use silicon carbide for copper alloys, graphite for aluminum, etc. |
Thermal Shock Resistance | Essential for metals requiring rapid heating/cooling (e.g., copper, brass). |
Best Practices | Use separate crucibles for each metal and inspect regularly for wear. |
Ensure your metal casting quality—contact our experts today for the right crucible solutions!