Quenching and tempering are critical heat treatment processes used to achieve desired mechanical properties in steel, such as strength, hardness, and toughness. The process begins with austenitizing the steel at high temperatures (around 900 °C – 1000 °C), followed by rapid cooling (quenching) to form a martensitic structure. Tempering is then performed to reduce brittleness and improve toughness, ensuring the material is suitable for its intended application. This sequence is essential for optimizing the balance between strength and toughness in steel components.
Key Points Explained:
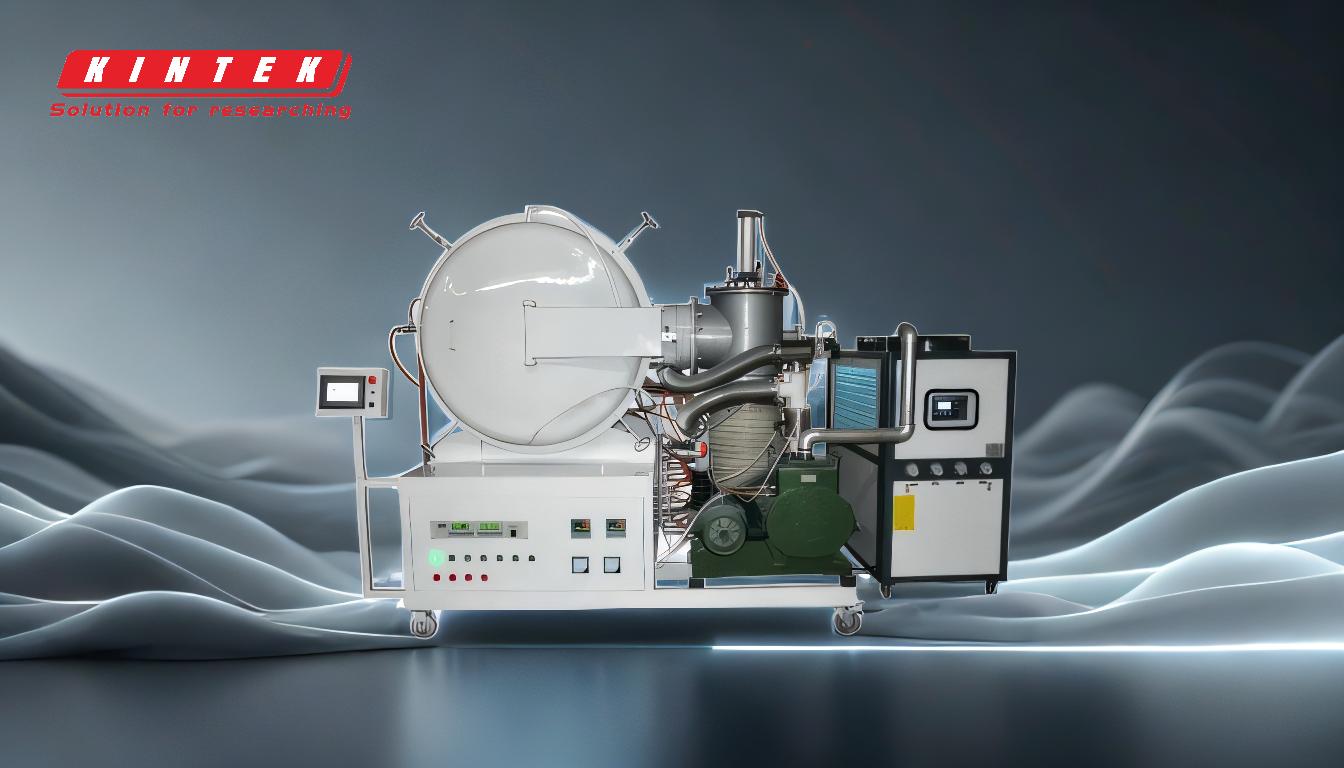
-
Austenitizing and Quenching:
- Austenitizing involves heating the steel to a high temperature (typically 900 °C – 1000 °C) to transform its microstructure into austenite, a phase that allows for uniform carbon distribution.
- Quenching follows, where the steel is rapidly cooled, usually in water, oil, or air, to form martensite. This phase is extremely hard but brittle, making the steel unsuitable for many applications without further treatment.
-
Formation of Martensite:
- Martensite is a hard, brittle microstructure formed during rapid cooling. While it provides high strength and hardness, it lacks the toughness required for most engineering applications.
- The quenching process ensures the formation of martensite, which is a prerequisite for the subsequent tempering step.
-
Purpose of Tempering:
- Tempering involves reheating the quenched steel to a temperature below the austenitizing range (typically 150 °C – 650 °C) and holding it for a specific time before cooling.
- This process reduces the brittleness of martensite, improves toughness, and adjusts the material's mechanical properties, such as strength and hardness, to meet application requirements.
-
Sequence of Quenching and Tempering:
- Quenching must always precede tempering. Quenching creates the martensitic structure, which is then tempered to achieve the desired balance of properties.
- Skipping quenching would mean the steel does not form martensite, making tempering ineffective for improving toughness and reducing brittleness.
-
Importance of Quench Testing:
- Quench testing is used to evaluate the hardenability of steel, which is its ability to form martensite during quenching.
- This testing helps manufacturers select the appropriate steel grade and heat treatment parameters to minimize risks such as distortion, cracking, and residual stresses during production.
-
Applications of Quenched and Tempered Steel:
- Quenched and tempered steels are widely used in industries requiring high strength and toughness, such as automotive, aerospace, and construction.
- Examples include gears, shafts, and structural components that must withstand high stresses and impacts.
In summary, quenching before tempering is a fundamental step in heat treatment to achieve the desired mechanical properties in steel. The process ensures the formation of martensite, which is then tempered to enhance toughness and reduce brittleness, making the material suitable for demanding applications.
Summary Table:
Step | Description |
---|---|
Austenitizing | Heat steel to 900 °C – 1000 °C to form austenite, ensuring uniform carbon distribution. |
Quenching | Rapidly cool steel to form martensite, a hard but brittle microstructure. |
Tempering | Reheat to 150 °C – 650 °C to reduce brittleness and improve toughness. |
Quench Testing | Evaluate hardenability to minimize risks like distortion and cracking. |
Applications | Used in automotive, aerospace, and construction for gears, shafts, and structural components. |
Discover how quenching and tempering can optimize your steel's performance—contact our experts today!