Coating chambers, particularly those used in vacuum deposition processes, are sophisticated systems designed to apply thin, durable, and protective layers onto various surfaces. These chambers operate under vacuum conditions to vaporize solid metallic materials, allowing the vaporized atoms to penetrate and bond with the product's surface, forming a protective coating. The process involves several key components, each contributing to the overall functionality and efficiency of the coating process. Understanding how these components work together provides insight into the complex yet precise nature of vacuum coating technology.
Key Points Explained:
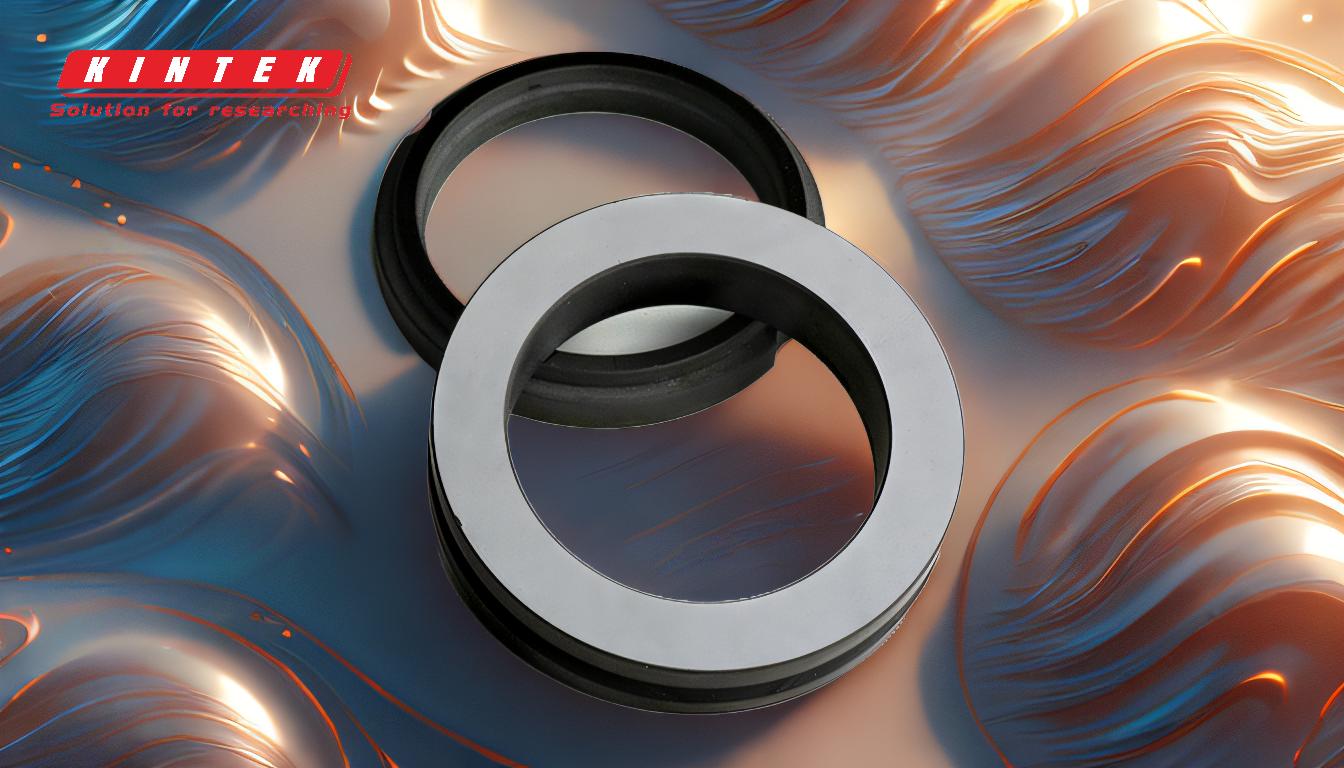
-
Vacuum Chamber and Coating Equipment:
- The vacuum chamber is the core component where the coating process takes place. It is designed to maintain a high vacuum environment, which is essential for the vaporization and deposition of materials.
- The chamber is typically made of materials that can withstand high temperatures and pressures, ensuring a stable environment for the coating process.
- Inside the chamber, the product to be coated is placed, and the vaporized material is directed towards it to form the protective layer.
-
Vacuum Obtaining Part:
- This component is responsible for creating and maintaining the vacuum inside the chamber. It includes pumps and valves that remove air and other gases from the chamber.
- The vacuum is crucial as it prevents contamination and allows the vaporized material to travel unimpeded to the product's surface.
-
Vacuum Measurement Part:
- Accurate measurement of the vacuum level is essential for controlling the coating process. This part includes gauges and sensors that monitor the pressure inside the chamber.
- Maintaining the correct vacuum level ensures the quality and consistency of the coating.
-
Power Supply Part:
- The power supply provides the necessary energy to vaporize the solid metallic material. This can include high-voltage power supplies for sputtering or evaporation sources.
- The power supply must be stable and controllable to ensure precise deposition of the coating material.
-
Process Gas Input System:
- In some coating processes, specific gases are introduced into the chamber to enhance the deposition process or modify the properties of the coating.
- The gas input system controls the flow and composition of these gases, which can influence the coating's adhesion, density, and other characteristics.
-
Mechanical Transmission Part:
- This part includes mechanisms for moving and positioning the product within the chamber. It ensures that the product is evenly coated and that the vaporized material is uniformly distributed.
- Precision in movement is crucial for achieving a consistent coating thickness and quality.
-
Heating and Temperature Measurement Equipment:
- Temperature control is vital in the coating process. Heating elements and temperature sensors ensure that the chamber and the product are maintained at the optimal temperature for deposition.
- Proper temperature management affects the rate of vaporization and the quality of the coating.
-
Ion Evaporation and Sputtering Source:
- These sources are used to vaporize the solid material. Ion evaporation involves heating the material until it vaporizes, while sputtering uses high-energy ions to knock atoms off the target material.
- The choice of source depends on the material being used and the desired properties of the coating.
-
Water Cooling System:
- The coating process generates significant heat, which must be managed to prevent damage to the equipment and ensure consistent process conditions.
- The water cooling system circulates water through the chamber and other components to dissipate heat and maintain a stable operating temperature.
In summary, coating chambers are complex systems that integrate various components to achieve precise and high-quality coatings. Each component plays a specific role in creating the vacuum environment, vaporizing the coating material, and ensuring even deposition on the product's surface. Understanding these components and their functions is essential for optimizing the coating process and achieving the desired protective and functional properties of the coating.
Summary Table:
Component | Function |
---|---|
Vacuum Chamber & Coating Equipment | Maintains a high vacuum environment for material vaporization and deposition. |
Vacuum Obtaining Part | Creates and maintains vacuum conditions to prevent contamination. |
Vacuum Measurement Part | Monitors and controls vacuum levels for consistent coating quality. |
Power Supply Part | Provides energy for vaporizing solid materials. |
Process Gas Input System | Introduces gases to enhance deposition or modify coating properties. |
Mechanical Transmission Part | Ensures even coating by precisely positioning the product. |
Heating & Temperature Measurement | Maintains optimal temperatures for vaporization and coating quality. |
Ion Evaporation & Sputtering Source | Vaporizes materials for deposition using heat or high-energy ions. |
Water Cooling System | Dissipates heat to maintain stable operating conditions. |
Optimize your coating process with advanced vacuum deposition systems—contact our experts today!