An Inductotherm furnace operates on the principle of electromagnetic induction to melt metals efficiently. The process begins with converting standard 50Hz AC power into medium-frequency AC (300Hz to 1000Hz) using a power supply device. This medium-frequency current flows through a capacitor and induction coil, creating a high-density magnetic field. When a conductive metal is placed inside the coil, the magnetic field induces eddy currents within the metal, generating heat through the Joule effect. This heat melts the metal without direct contact between the coil and the material, ensuring precise temperature control and energy efficiency. The furnace is widely used for melting various metals, including steel, copper, and aluminum, and is valued for its compact design, rapid melting, and minimal heat loss.
Key Points Explained:
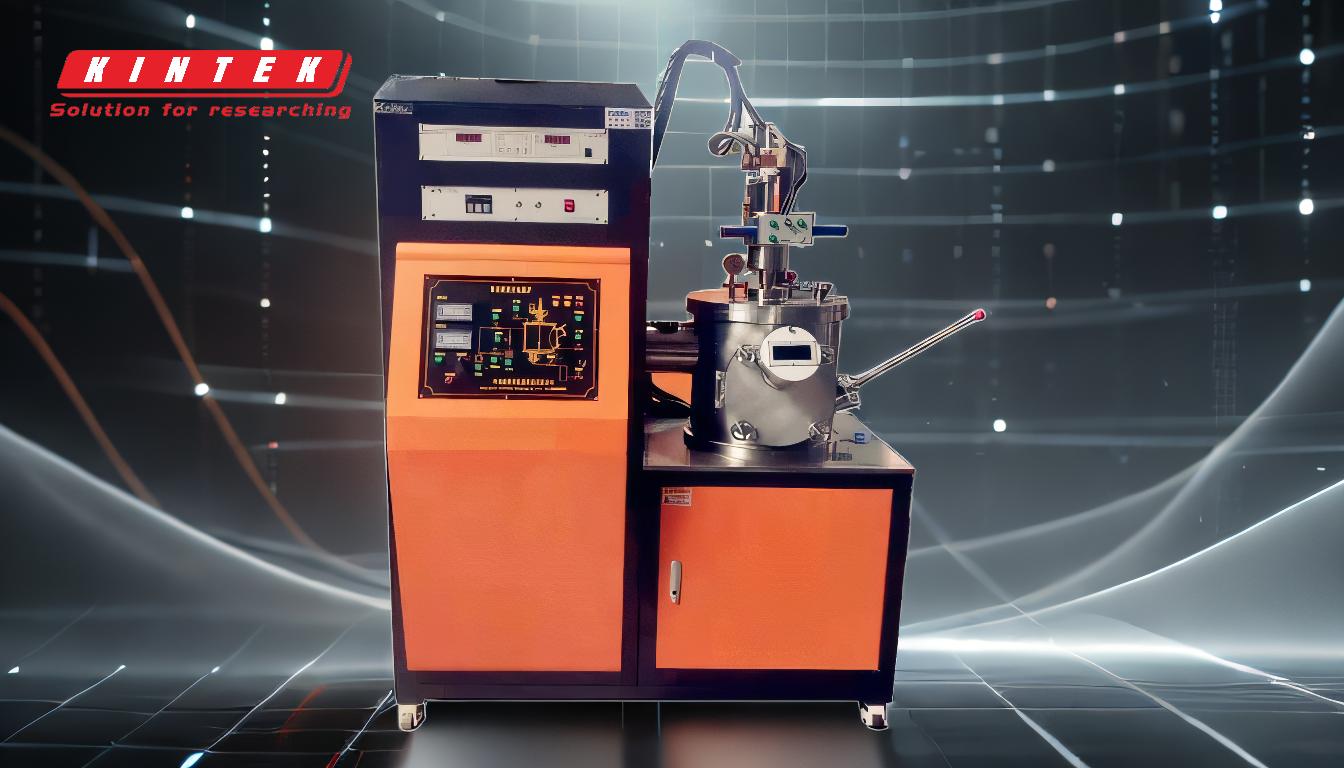
-
Power Conversion and Medium-Frequency Current Generation:
- The furnace starts by converting standard 50Hz AC power into medium-frequency AC (300Hz to 1000Hz). This is achieved through a power supply device that first rectifies the AC into DC and then inverts it back into adjustable medium-frequency AC.
- This conversion is crucial because higher frequencies allow for more efficient heat generation in the metal.
-
Electromagnetic Induction and Eddy Currents:
- The medium-frequency AC flows through an induction coil, creating a high-density magnetic field. When a conductive metal is placed within this coil, the magnetic field induces eddy currents within the metal.
- These eddy currents are circular electric currents that flow within the metal, generating heat due to the metal's electrical resistance (Joule effect).
-
Non-Contact Heating:
- The induction coil does not physically touch the metal being melted. Instead, the heat is generated internally within the metal through electromagnetic induction.
- This non-contact method ensures minimal contamination and precise temperature control, making it ideal for high-purity applications.
-
Efficient Heat Generation and Melting:
- The heat generated by the eddy currents is sufficient to melt the metal, with temperatures reaching up to 1370°C (2500°F) for materials like steel.
- The process is highly efficient because the heat is generated directly within the metal, reducing energy loss compared to traditional heating methods.
-
Cooling and System Design:
- The induction coil is typically cooled by circulating water to prevent overheating and maintain system efficiency.
- The furnace's compact and lightweight design, combined with its high productivity and energy efficiency, makes it a preferred choice for industrial metal melting.
-
Applications and Advantages:
- Inductotherm furnaces are versatile and can melt a wide range of metals, including carbon steel, alloy steel, copper, aluminum, lead, and zinc.
- Advantages include rapid melting, precise temperature control, energy efficiency, and minimal heat loss, making them suitable for both large-scale industrial and specialized applications.
By combining these principles, the Inductotherm furnace provides a reliable, efficient, and precise method for melting metals, meeting the needs of various industries requiring high-quality metal processing.
Summary Table:
Key Feature | Description |
---|---|
Power Conversion | Converts 50Hz AC to medium-frequency AC (300Hz–1000Hz) for efficient heating. |
Electromagnetic Induction | Generates eddy currents in metals for non-contact, contamination-free heating. |
Heat Generation | Joule effect heats metals internally, reaching up to 1370°C (2500°F). |
Cooling System | Water-cooled induction coil prevents overheating and maintains efficiency. |
Applications | Melts steel, copper, aluminum, and more with rapid melting and minimal heat loss. |
Learn how an Inductotherm furnace can revolutionize your metal melting process—contact us today for expert guidance!