Chemical vapor deposition (CVD) is a widely used method for synthesizing carbon nanotubes (CNTs) due to its cost-effectiveness, scalability, and ability to control the structural properties of the nanotubes. The process involves the decomposition of gaseous carbon-containing precursors on a substrate, often assisted by a catalyst, to form CNTs. CVD operates under controlled temperature and pressure conditions, enabling precise control over the growth process. This method has become the dominant commercial technique for CNT production, surpassing traditional methods like laser ablation and arc discharge. Additionally, advancements in CVD, such as plasma-enhanced CVD (PECVD), have further improved the efficiency and environmental sustainability of the process.
Key Points Explained:
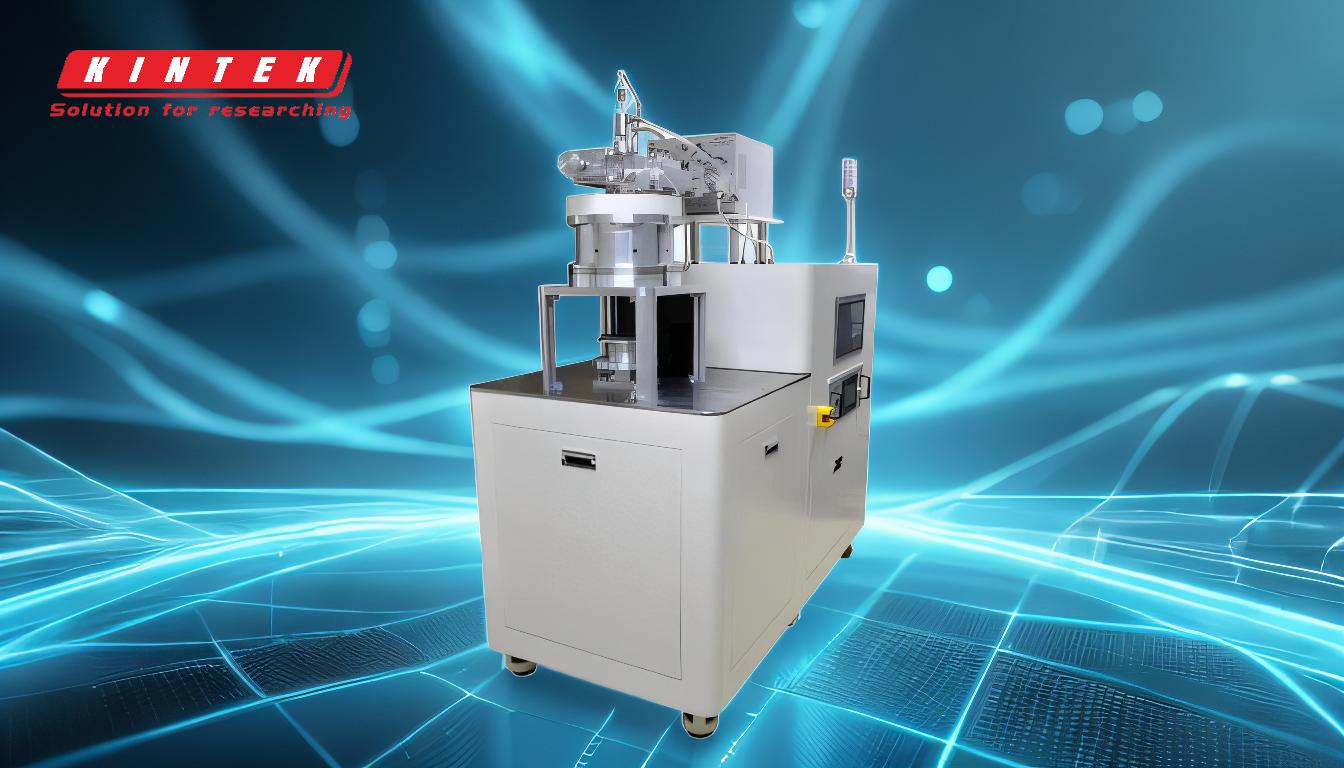
-
Basic Mechanism of CVD for CNT Synthesis:
- CVD involves the introduction of gaseous carbon-containing precursors (e.g., methane, ethylene, or carbon monoxide) into a reaction chamber.
- These precursors decompose at high temperatures (typically 500–1000°C) in the presence of a catalyst (e.g., iron, cobalt, or nickel nanoparticles) deposited on a substrate.
- The decomposition leads to the formation of carbon atoms, which then assemble into CNTs on the catalyst surface.
-
Role of Catalysts in CVD:
- Catalysts play a crucial role in controlling the growth of CNTs. They determine the diameter, length, and chirality of the nanotubes.
- The catalyst nanoparticles act as nucleation sites for CNT growth, and their size and composition influence the structural properties of the resulting nanotubes.
-
Types of CVD for CNT Synthesis:
- Thermal CVD: The most common method, where heat is used to decompose the precursors and initiate CNT growth.
- Plasma-Enhanced CVD (PECVD): Uses plasma to excite the precursor gases, allowing CNT growth at lower temperatures. This method is energy-efficient and reduces thermal stress on the substrate.
- Catalytic CVD (CCVD): A variant of CVD that emphasizes the use of catalysts to enhance control over CNT properties. It is the mainstream method due to its cost-effectiveness and scalability.
-
Environmental and Economic Considerations:
- CVD is favored for its ability to produce high-quality CNTs with minimal environmental impact compared to traditional methods.
- The synthesis process is optimized to reduce material and energy consumption, as well as greenhouse gas emissions, making it a more sustainable option.
-
Advantages of CVD for CNT Production:
- Scalability: CVD can be scaled up for industrial production, making it suitable for commercial applications.
- Structural Control: The process allows precise control over the diameter, length, and alignment of CNTs, which is critical for specific applications.
- Cost-Effectiveness: CVD is more economical than methods like laser ablation and arc discharge, especially for large-scale production.
-
Challenges and Future Directions:
- One of the challenges in CVD is achieving uniform CNT growth over large areas, which requires precise control of process parameters.
- Emerging trends include the use of green or waste feedstocks, such as carbon dioxide captured by electrolysis or methane pyrolysis, to further enhance the sustainability of CNT production.
By leveraging the principles of chemical vapor deposition, researchers and manufacturers can produce carbon nanotubes with tailored properties for applications in electronics, energy storage, and materials science, while minimizing environmental impact.
Summary Table:
Aspect | Details |
---|---|
Mechanism | Decomposition of carbon-containing gases on a catalyst-coated substrate. |
Catalysts | Iron, cobalt, or nickel nanoparticles control CNT diameter and structure. |
Types of CVD | Thermal CVD, Plasma-Enhanced CVD (PECVD), Catalytic CVD (CCVD). |
Advantages | Scalable, cost-effective, precise control over CNT properties. |
Sustainability | Reduces energy consumption and greenhouse gas emissions. |
Challenges | Uniform CNT growth over large areas requires precise parameter control. |
Discover how CVD can revolutionize your carbon nanotube production—contact our experts today for tailored solutions!