Induction in a vacuum operates similarly to induction in other environments, but the absence of air or other gases eliminates factors like air resistance and oxidation, making it more efficient for certain applications. Induction relies on electromagnetic fields to generate heat or motion in conductive materials. In a vacuum, the process is cleaner and more controlled, as there are no atmospheric particles to interfere with the electromagnetic fields or the material being processed. This makes vacuum induction ideal for applications like melting metals, semiconductor manufacturing, and other high-precision processes where contamination must be minimized.
Key Points Explained:
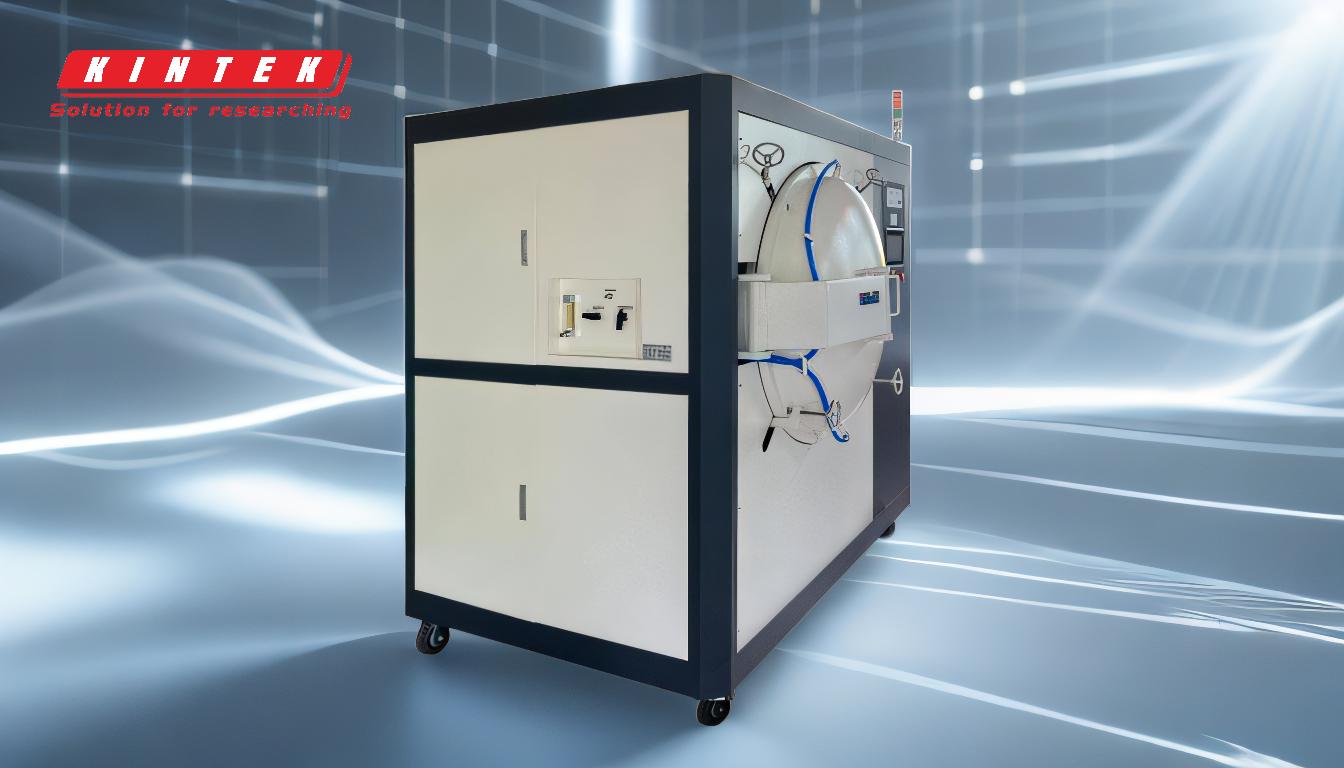
-
Fundamentals of Induction:
- Induction works by creating a fluctuating electromagnetic field around a conductive material, which induces eddy currents within the material.
- These eddy currents generate heat due to the material's electrical resistance, a phenomenon known as Joule heating.
- In a vacuum, the absence of air means there is no medium to dissipate heat through convection, so heat transfer occurs primarily through radiation and conduction within the material itself.
-
Advantages of Vacuum Environment:
- Contamination Control: A vacuum eliminates the presence of oxygen and other reactive gases, preventing oxidation and other chemical reactions that could degrade the material being processed.
- Precision and Purity: Vacuum induction is widely used in industries like aerospace and electronics, where material purity is critical. For example, vacuum induction melting (VIM) is used to produce high-purity metals and alloys.
- Energy Efficiency: Without air resistance, the electromagnetic fields can interact more directly with the material, reducing energy losses and improving efficiency.
-
Applications of Vacuum Induction:
- Metal Melting and Casting: Vacuum induction furnaces are used to melt and cast metals like titanium, nickel, and stainless steel, which are prone to oxidation in air.
- Semiconductor Manufacturing: Vacuum induction is used in processes like chemical vapor deposition (CVD) and physical vapor deposition (PVD) to create thin films with high precision.
- Research and Development: Vacuum environments are ideal for studying material properties under controlled conditions, free from atmospheric interference.
-
Challenges and Considerations:
- Cost and Complexity: Creating and maintaining a vacuum requires specialized equipment, which can be expensive and technically challenging.
- Heat Management: In a vacuum, heat dissipation is slower, so careful thermal management is required to prevent overheating or damage to equipment.
- Material Compatibility: Not all materials are suitable for vacuum induction, as some may vaporize or degrade under vacuum conditions.
-
Comparison with Non-Vacuum Induction:
- In non-vacuum environments, induction processes are often limited by factors like oxidation, contamination, and energy losses due to air resistance.
- Vacuum induction offers a cleaner, more controlled alternative, but it comes with higher operational costs and complexity.
In summary, induction in a vacuum leverages the principles of electromagnetic induction while eliminating the drawbacks associated with atmospheric interference. This makes it a powerful tool for high-precision, high-purity applications, though it requires specialized equipment and careful process management.
Summary Table:
Aspect | Details |
---|---|
Fundamentals | Electromagnetic fields induce eddy currents, generating heat via Joule heating. |
Advantages | Contamination control, precision, purity, and energy efficiency. |
Applications | Metal melting, semiconductor manufacturing, and R&D. |
Challenges | High cost, heat management, and material compatibility. |
Comparison | Cleaner and more controlled than non-vacuum induction but more complex. |
Learn more about how vacuum induction can revolutionize your processes—contact our experts today!