Sintering is a critical process in materials science and manufacturing, where powdered materials are transformed into a solid mass through the application of heat and pressure, without reaching the material's melting point. This process involves several stages, including powder preparation, compaction, heating in a sintering furnace, and cooling, leading to the formation of a dense, cohesive structure. The sintering process is essential for producing components with specific mechanical properties, such as strength and durability, and is widely used in industries ranging from metallurgy to ceramics.
Key Points Explained:
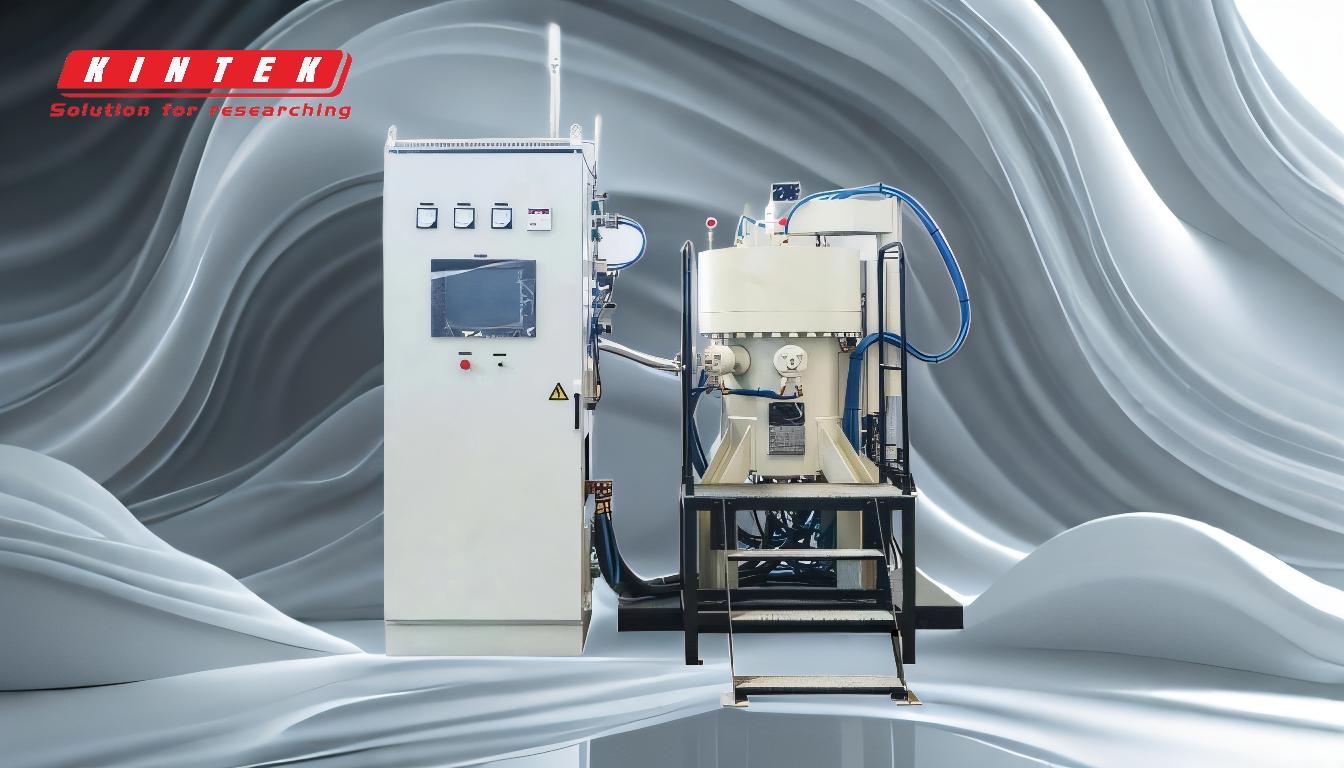
-
Preparation of Powder Compact:
- The sintering process begins with the preparation of a powder compact. This involves mixing primary materials with coupling agents to ensure uniformity.
- The powder is then compressed using pressing tools or other methods to form a specific shape. This step is crucial for achieving the desired geometry and density of the final product.
-
Compaction:
- After the powder is prepared, it is compacted under pressure to eliminate voids and ensure uniformity. This step helps in achieving a consistent density throughout the material, which is essential for the subsequent stages of sintering.
-
Heating in a Sintering Furnace:
- The compacted material is then subjected to controlled heating in a sintering furnace. The temperature is carefully regulated to facilitate particle bonding without causing complete melting.
- During this stage, atoms diffuse across particle boundaries, leading to neck formation and densification. This is where the material starts to fuse together, reducing porosity and increasing strength.
-
Cooling and Solidification:
- After the heating process, the material is allowed to cool gradually. This cooling stage is critical as it allows the material to solidify into a rigid and cohesive structure.
- The controlled cooling process ensures that the final product has the desired mechanical properties and dimensional stability.
-
Post-Sintering Treatments:
- In some cases, sintered parts may undergo additional treatments such as calibration or other post-sintering processes to achieve the desired specifications.
- Calibration involves placing the piece back in the press and adjusting it using a calibration die. This ensures that the final product meets the required tolerances and quality standards.
-
Vacuum and Gas Control:
- In certain sintering processes, a vacuum pump is used to remove air from the furnace chamber, creating a vacuum. Once the desired vacuum level is achieved, a protective or working gas is introduced to maintain the required working pressure.
- This step is crucial for preventing oxidation and other unwanted chemical reactions during the sintering process.
-
Walking-Beam Mechanism:
- Some sintering furnaces use a walking-beam mechanism to transport the material through the furnace. This mechanism involves lifting, pushing forward, and lowering the material, effectively "walking" it through the heating and cooling zones.
- This method ensures uniform heating and cooling, which is essential for producing high-quality sintered products.
-
Liquid Phase Sintering (LPS):
- In some cases, a liquid phase may be introduced during the sintering process to accelerate particle merging and densification. This technique, known as Liquid Phase Sintering (LPS), can significantly enhance the properties of the final product.
By understanding these key points, one can appreciate the complexity and precision involved in the sintering process. Each stage plays a crucial role in determining the final properties of the sintered material, making it a vital process in modern manufacturing.
Summary Table:
Stage | Description |
---|---|
Powder Preparation | Mixing primary materials with coupling agents for uniformity. |
Compaction | Compressing powder under pressure to eliminate voids and ensure uniformity. |
Heating in Furnace | Controlled heating to bond particles without melting, forming a dense structure. |
Cooling | Gradual cooling to solidify the material into a rigid, cohesive structure. |
Post-Sintering | Additional treatments like calibration to meet final specifications. |
Vacuum & Gas Control | Removing air and introducing protective gases to prevent oxidation. |
Walking-Beam Mechanism | Transporting material through the furnace for uniform heating and cooling. |
Liquid Phase Sintering | Introducing a liquid phase to accelerate particle merging and densification. |
Discover how sintering can enhance your manufacturing process—contact our experts today!