Sintering is a critical manufacturing process used to transform powdery materials into dense, solid bodies by applying heat and pressure without reaching the material's melting point. This process is widely used in industries such as powder metallurgy and ceramics. The sintering process typically involves several stages, including powder preparation, compaction, heating, and cooling. During heating, particles densify and merge, forming a unified mass with improved mechanical properties. The process can be enhanced using techniques like liquid phase sintering (LPS) or by adding binders and additives to fill pores and improve material strength. Sintering is particularly useful for materials with high melting points, such as tungsten and molybdenum, and is essential for creating durable, high-performance components.
Key Points Explained:
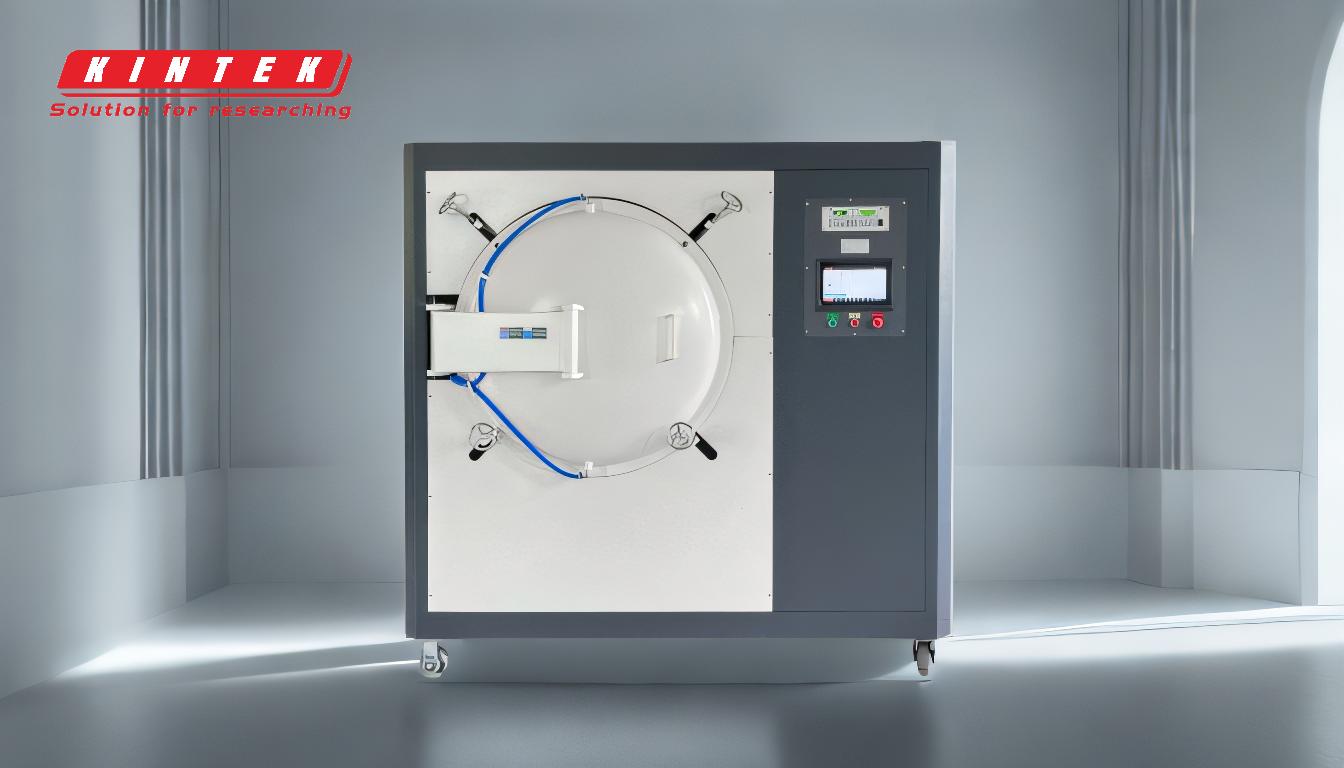
-
Definition and Purpose of Sintering:
- Sintering is a process that transforms powdery materials into dense, solid bodies by applying heat and pressure below the material's melting point.
- It is used in industries like powder metallurgy and ceramics to create durable, high-performance components.
- The process is particularly useful for materials with extremely high melting points, such as tungsten and molybdenum.
-
Stages of the Sintering Process:
-
Powder Preparation:
- Involves mixing raw materials, binders, and additives to create a uniform powder or slurry.
- For ceramics, this may include mixing water, deflocculant, binder, and unfired ceramic powder to form a spray-dried slurry.
-
Powder Compaction:
- The powder is mechanically densified using cold or hot pressing techniques to form a "green part" (a pre-sintered shape).
- Compaction ensures the powder particles are closely packed, reducing porosity.
-
Heating and Consolidation:
- The green part is heated to just below the material's melting point, allowing particles to bond through atomic diffusion.
- This stage activates martensitic crystalline microstructures and densifies the material.
-
Cooling and Solidification:
- The material cools and solidifies into a unified mass with improved mechanical properties.
-
Powder Preparation:
-
Key Mechanisms in Sintering:
-
Atomic Diffusion:
- Atoms diffuse across particle boundaries, fusing particles together to form a solid piece.
-
Liquid Phase Sintering (LPS):
- A liquid phase (e.g., a binder or additive) is introduced to accelerate particle merging and fill remaining pores.
-
Particle Densification:
- Particles densify and merge, reducing porosity and increasing material strength.
-
Atomic Diffusion:
-
Factors Influencing Sintering:
-
Temperature Control:
- Precise control of heating temperature is crucial to avoid melting while ensuring proper particle bonding.
-
Pressure Application:
- Pressure is applied during compaction to ensure uniform particle packing and reduce porosity.
-
Additives and Binders:
- Elements like copper powder or cemented carbides, along with binders, enhance sintering by filling pores and improving material flow.
-
Atmosphere Control:
- A controlled atmosphere (e.g., inert gas) prevents oxidation and contamination during sintering.
-
Temperature Control:
-
Applications of Sintering:
-
Powder Metallurgy:
- Used to produce metal components with complex shapes and high strength, such as gears, bearings, and automotive parts.
-
Ceramic Manufacturing:
- Used to create ceramic components like tiles, insulators, and cutting tools.
-
High-Melting-Point Materials:
- Essential for processing materials like tungsten and molybdenum, which are difficult to melt and shape using traditional methods.
-
Powder Metallurgy:
-
Advantages of Sintering:
-
Improved Material Properties:
- Sintered materials exhibit higher strength, hardness, and durability compared to non-sintered materials.
-
Cost-Effectiveness:
- Sintering allows for near-net-shape manufacturing, reducing the need for extensive machining and material waste.
-
Versatility:
- The process can be adapted for a wide range of materials and applications, from metals to ceramics.
-
Improved Material Properties:
-
Challenges in Sintering:
-
Porosity Control:
- Achieving low porosity while maintaining material strength can be challenging, especially in complex shapes.
-
Dimensional Accuracy:
- Shrinkage during sintering can affect dimensional accuracy, requiring careful design and process control.
-
Material Limitations:
- Not all materials are suitable for sintering, particularly those with poor diffusion properties or low melting points.
-
Porosity Control:
By understanding these key points, equipment and consumable purchasers can make informed decisions about selecting sintering materials, additives, and equipment to achieve desired material properties and performance.
Summary Table:
Aspect | Details |
---|---|
Definition | Transforms powdery materials into dense solids using heat and pressure. |
Key Stages | Powder preparation, compaction, heating, and cooling. |
Mechanisms | Atomic diffusion, liquid phase sintering (LPS), and particle densification. |
Applications | Powder metallurgy, ceramic manufacturing, high-melting-point materials. |
Advantages | Improved strength, cost-effectiveness, and versatility. |
Challenges | Porosity control, dimensional accuracy, and material limitations. |
Discover how sintering can enhance your manufacturing process—contact us today for expert guidance!