The temperature that metal can reach depends on the type of metal and its properties, such as melting point, thermal conductivity, and resistance to oxidation. Metals like tungsten can withstand extremely high temperatures, up to 3,422°C (6,192°F), before melting, while others like aluminum melt at much lower temperatures, around 660°C (1,220°F). The maximum temperature a metal can endure is also influenced by its environment, such as exposure to oxygen or other reactive substances, which can cause oxidation or degradation. Understanding these factors is crucial for applications in industries like aerospace, manufacturing, and energy, where metals are subjected to extreme conditions.
Key Points Explained:
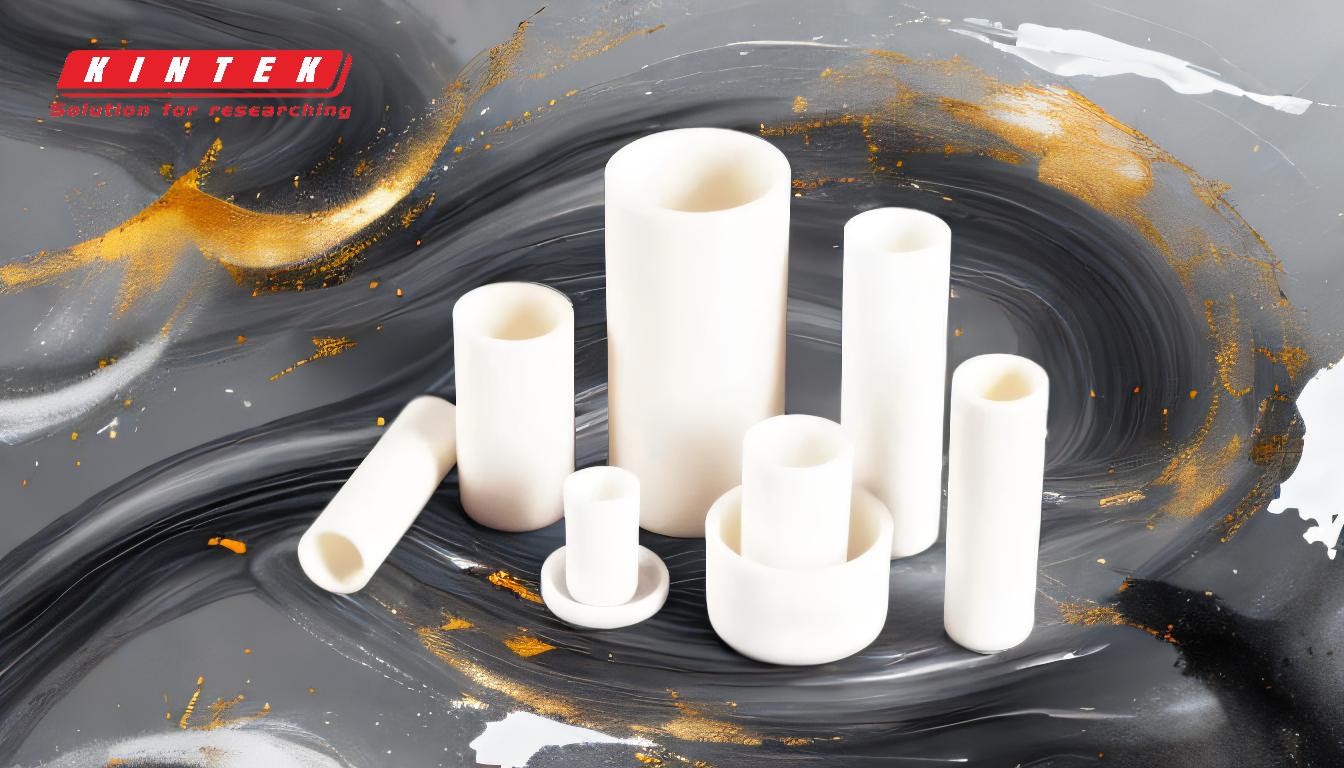
-
Melting Points of Common Metals
- Metals have varying melting points, which determine how hot they can get before transitioning from solid to liquid.
- Tungsten: 3,422°C (6,192°F) – one of the highest melting points among metals.
- Iron: 1,538°C (2,800°F).
- Aluminum: 660°C (1,220°F).
- Copper: 1,085°C (1,985°F).
- These melting points are critical for selecting metals in high-temperature applications.
- Metals have varying melting points, which determine how hot they can get before transitioning from solid to liquid.
-
Factors Influencing Maximum Temperature
- Thermal Conductivity: Metals with high thermal conductivity, like copper, can dissipate heat more effectively, allowing them to withstand higher temperatures for longer periods.
- Oxidation Resistance: Metals like stainless steel or nickel alloys resist oxidation at high temperatures, making them suitable for use in environments with oxygen exposure.
- Mechanical Strength: At high temperatures, some metals lose their structural integrity. For example, steel becomes less rigid as it approaches its melting point.
-
Applications in Extreme Environments
- Aerospace: Metals like titanium and nickel-based superalloys are used in jet engines and spacecraft due to their ability to withstand extreme heat and stress.
- Energy: In nuclear reactors, metals like zirconium are chosen for their high melting points and resistance to radiation.
- Manufacturing: Furnaces and kilns often use refractory metals like tungsten or molybdenum to handle high-temperature processes.
-
Limitations and Degradation
- Even below their melting points, metals can experience thermal expansion, creep (deformation under stress), and oxidation, which can limit their usability.
- Protective coatings or alloys are often used to enhance a metal's performance at high temperatures. For example, chromium is added to steel to improve its oxidation resistance.
-
Experimental and Theoretical Limits
- In laboratory settings, metals can be subjected to temperatures approaching their theoretical limits using specialized equipment like arc furnaces or plasma torches.
- However, practical applications often require metals to operate well below their melting points to ensure safety and longevity.
Understanding the thermal properties of metals is essential for selecting the right material for specific applications, ensuring both performance and durability under extreme conditions.
Summary Table:
Metal | Melting Point (°C) | Melting Point (°F) | Key Properties |
---|---|---|---|
Tungsten | 3,422 | 6,192 | Highest melting point, durable |
Iron | 1,538 | 2,800 | High strength, widely used |
Aluminum | 660 | 1,220 | Lightweight, good conductivity |
Copper | 1,085 | 1,985 | Excellent thermal and electrical conductivity |
Need help selecting the right metal for high-temperature applications? Contact our experts today!