The lifespan of a heating element depends on several factors, including material type, operating conditions, maintenance, and usage patterns. For instance, silicon carbide heating elements are influenced by furnace atmosphere, watt density, operating temperature, and whether they are used continuously or intermittently. On average, oven heating elements can last between 5 to 15 years, but this varies widely based on factors like maintenance, usage frequency, and environmental conditions. Manufacturers typically only warrant against manufacturing defects, as operational variables like rapid heating/cooling cycles or reducing atmospheres significantly impact longevity. Proper material selection, maintenance, and adherence to operational guidelines are critical for maximizing the lifespan of heating elements.
Key Points Explained:
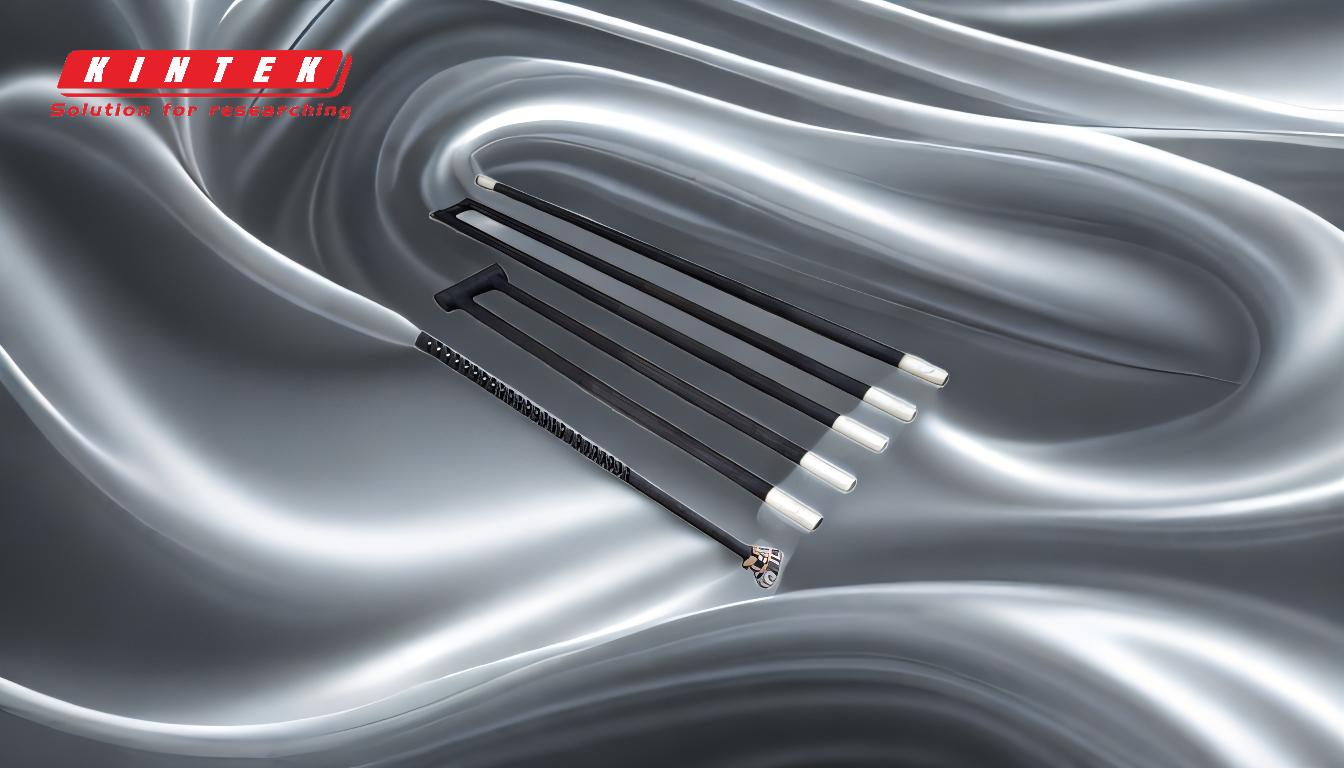
-
Material Type and Properties:
- The lifespan of a heating element is heavily influenced by the material used. For example, silicon carbide heating elements are known for their durability but are still affected by factors like furnace atmosphere and watt density.
- Materials must be chosen based on their temperature ratings, cost, and suitability for specific applications. Reactivity to oxygen is also a critical factor, as some materials can tolerate high temperatures in the presence of oxygen, while others require protective atmospheres.
-
Operational Conditions:
- Temperature: Operating at higher temperatures can reduce the lifespan of a heating element. Silicon carbide elements, for instance, are sensitive to extreme temperatures.
- Atmosphere: The furnace atmosphere plays a significant role. Reducing atmospheres or environments with reactive gases can accelerate wear and tear.
- Watt Density: Higher watt densities can lead to faster degradation of the heating element.
- Heating/Cooling Cycles: Rapid heating and cooling cycles can cause thermal stress, leading to premature failure.
-
Usage Patterns:
- Continuous vs. Intermittent Use: Elements used continuously may wear out faster than those used intermittently. However, frequent on/off cycles can also cause thermal stress.
- Maintenance Frequency: Regular maintenance can extend the lifespan of a heating element. Neglecting maintenance can lead to faster degradation.
-
Manufacturer Warranty and Defects:
- Manufacturers typically only warrant against manufacturing defects, as operational variables are beyond their control. This highlights the importance of proper installation, operation, and maintenance to ensure longevity.
-
Average Lifespan:
- For oven heating elements, the average lifespan ranges from 5 to 15 years. However, this is highly variable and depends on the factors mentioned above.
- Silicon carbide elements, while durable, have their lifespan influenced by specific operational conditions.
-
Maximizing Lifespan:
- Proper Material Selection: Choose materials that are suitable for the specific application and environmental conditions.
- Adherence to Operational Guidelines: Follow manufacturer recommendations for temperature, watt density, and atmosphere.
- Regular Maintenance: Perform routine inspections and maintenance to identify and address issues early.
- Avoid Rapid Cycling: Minimize rapid heating and cooling cycles to reduce thermal stress.
In summary, the lifespan of a heating element is not fixed and depends on a combination of material properties, operational conditions, and maintenance practices. By understanding and managing these factors, users can maximize the longevity of their heating elements.
Summary Table:
Factor | Impact on Lifespan |
---|---|
Material Type | Durability varies; silicon carbide is durable but sensitive to atmosphere and watt density. |
Operational Conditions | High temperatures, reactive atmospheres, and rapid heating/cooling cycles reduce lifespan. |
Usage Patterns | Continuous use or frequent on/off cycles can cause wear and thermal stress. |
Maintenance | Regular maintenance extends lifespan; neglect accelerates degradation. |
Average Lifespan | Oven heating elements last 5–15 years; silicon carbide varies based on conditions. |
Need help choosing or maintaining heating elements? Contact our experts today for tailored solutions!