The frequency of replacing heating elements depends on their type, usage, and maintenance. Generally, heating elements in electric tank water heaters last 10–15 years, while those in tankless water heaters can last up to 20 years. Replacement is typically only necessary when the element fails due to malfunction, wear, or damage. Regular maintenance, such as descaling, can extend their lifespan. Heating elements can be replaced individually, so only the failed ones need attention, not the entire system.
Key Points Explained:
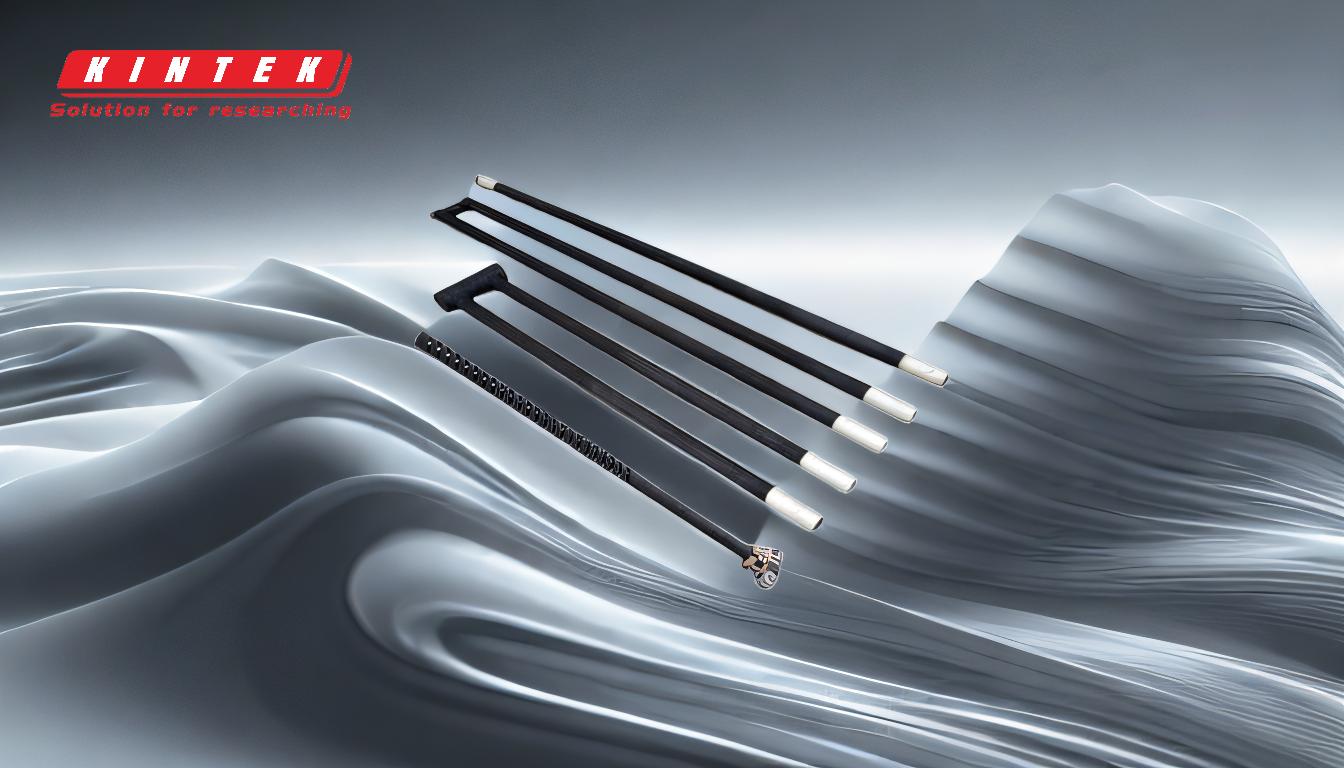
-
Lifespan of Heating Elements:
- Electric Tank Water Heaters: Heating elements typically last 10–15 years, aligning with the lifespan of the water heater itself.
- Tankless Water Heaters: Heating elements can last up to 20 years due to their design and operational efficiency.
-
When to Replace Heating Elements:
- Heating elements only need replacement when they fail. Common reasons for failure include:
- Malfunction: Electrical or mechanical issues can cause premature failure.
- Wear and Tear: Over time, continuous use can degrade the element.
- Damage: Physical damage or corrosion due to hard water can shorten lifespan.
- Heating elements only need replacement when they fail. Common reasons for failure include:
-
Replacement Process:
- Heating elements can be replaced individually. If one element fails in a system with multiple elements, only the faulty one needs replacement, reducing costs and downtime.
-
Maintenance to Extend Lifespan:
- Regular maintenance, such as descaling to remove mineral buildup, can prevent corrosion and extend the life of heating elements.
- Monitoring water quality and addressing hard water issues can also help.
-
Signs of a Failing Heating Element:
- Inconsistent Heating: Water may not heat evenly or may take longer to heat.
- No Hot Water: A complete failure of the heating element will result in no hot water.
- Unusual Noises: Banging or popping sounds may indicate mineral buildup or element issues.
By understanding these factors, equipment and consumable purchasers can make informed decisions about maintenance schedules and replacement timelines, ensuring optimal performance and cost-efficiency.
Summary Table:
Key Aspect | Details |
---|---|
Lifespan | - Electric Tank: 10–15 years - Tankless: Up to 20 years |
Replacement Trigger | Failure due to malfunction, wear, or damage |
Replacement Process | Individual replacement of faulty elements |
Maintenance Tips | Regular descaling, monitoring water quality |
Signs of Failure | Inconsistent heating, no hot water, unusual noises |
Need help with heating element maintenance or replacement? Contact our experts today for personalized advice!