Annealing is a heat treatment process that involves heating a metal to a specific temperature, holding it at that temperature for a certain period, and then cooling it slowly. This process is used to soften the metal, reduce internal stresses, refine its grain structure, and improve its ductility, making it easier to machine or further process. The temperature and cooling rate depend on the type of metal and the desired outcome. There are different types of annealing, such as full annealing, process annealing, and spheroidizing, each suited for specific applications. The process is widely used for both ferrous and non-ferrous alloys.
Key Points Explained:
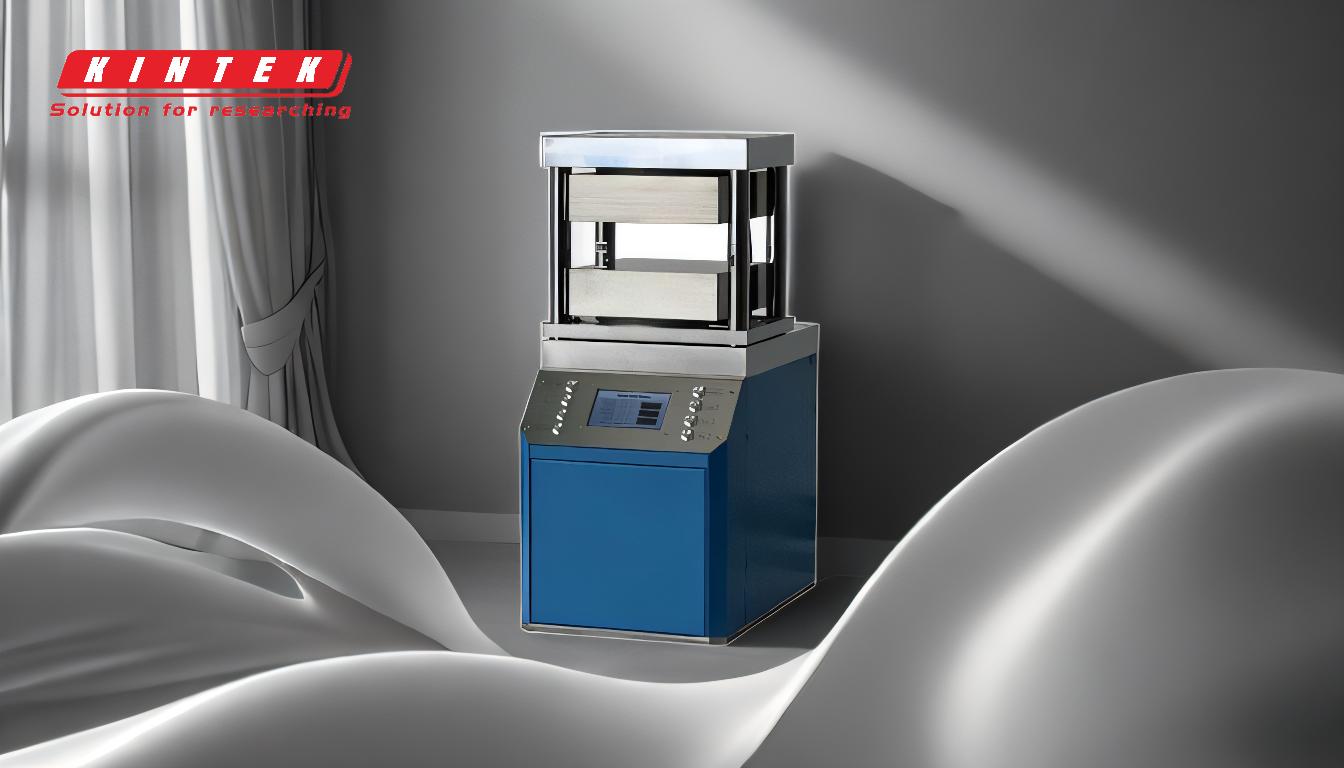
-
Purpose of Annealing:
- Softening the Metal: Annealing makes the metal softer, which is essential for further machining or forming processes.
- Stress Relief: It eliminates internal stresses that may have developed during previous manufacturing processes like casting, welding, or cold working.
- Grain Structure Refinement: The process refines the grain microstructure, making it more uniform and improving the material's ductility.
- Improved Machinability: By softening the metal and reducing internal stresses, annealing makes the material easier to machine.
-
Temperature and Heating:
- Recrystallization Temperature: The metal is heated above its recrystallization temperature but below its melting point. This temperature varies depending on the type of metal.
- Holding Time: The metal is held at this temperature for a specific period to allow the crystalline structure to become fluid, enabling defects to repair themselves.
-
Cooling Process:
- Slow Cooling: After heating, the metal is cooled slowly, often in the furnace itself, to room temperature. This slow cooling rate is crucial for achieving the desired soft and ductile structure.
- Controlled Cooling: The cooling rate must be carefully controlled to avoid the reintroduction of stresses or the formation of undesirable microstructures.
-
Types of Annealing:
- Full Annealing: Involves heating the metal to a temperature above its upper critical temperature, holding it there, and then slowly cooling it. This process is used to achieve maximum softness and ductility.
- Process Annealing: Used primarily for low-carbon steels, this process involves heating the metal to a temperature below the lower critical temperature and then cooling it. It is often used to relieve stresses in cold-worked metals.
- Spheroidizing: This type of annealing is used to produce a spheroidal or globular form of carbide in steel, improving its machinability and reducing hardness.
-
Applications:
- Ferrous Alloys: Commonly used for steels to improve machinability, reduce hardness, and prepare the material for further heat treatment.
- Non-Ferrous Alloys: Used for metals like aluminum, copper, and brass to improve ductility and reduce internal stresses.
-
Equipment:
- Annealing Furnaces: These are specially designed furnaces that can precisely control the heating and cooling rates. They are essential for achieving the desired material properties.
- Temperature Control: Accurate temperature control is critical to ensure the metal reaches the correct temperature and is held there for the appropriate amount of time.
-
Benefits:
- Improved Workability: Annealing makes the metal easier to work with, whether through machining, forming, or other processes.
- Enhanced Ductility: The process increases the metal's ability to deform without breaking, which is crucial for many manufacturing processes.
- Stress Reduction: By eliminating internal stresses, annealing reduces the risk of cracking or failure during subsequent processing.
-
Considerations:
- Material Type: The specific annealing process and parameters will vary depending on the type of metal being treated.
- Desired Outcome: The goals of the annealing process (e.g., softening, stress relief, grain refinement) will influence the choice of annealing type and parameters.
- Cooling Rate: The cooling rate must be carefully controlled to achieve the desired material properties without introducing new stresses.
In summary, annealing is a critical heat treatment process that involves precise control of heating and cooling to achieve specific material properties. It is widely used in the manufacturing industry to prepare metals for further processing, improve their workability, and enhance their performance characteristics.
Summary Table:
Aspect | Details |
---|---|
Purpose | Softens metal, relieves stress, refines grain structure, improves machinability. |
Temperature & Heating | Heated above recrystallization temperature, held for specific time. |
Cooling Process | Slow, controlled cooling to achieve desired properties. |
Types | Full annealing, process annealing, spheroidizing. |
Applications | Ferrous (steel) and non-ferrous alloys (aluminum, copper, brass). |
Equipment | Annealing furnaces with precise temperature control. |
Benefits | Improved workability, enhanced ductility, stress reduction. |
Considerations | Material type, desired outcome, cooling rate. |
Ready to optimize your metal processing with annealing? Contact our experts today for tailored solutions!