Brazing is a versatile joining process used across various industries due to its ability to create strong, leak-proof, and durable joints between dissimilar materials. It is particularly valued in applications where high precision, thermal resistance, and electrical conductivity are required. Below, we explore key examples of where brazing is utilized, highlighting its importance in industries such as aerospace, automotive, electronics, and HVAC.
Key Points Explained:
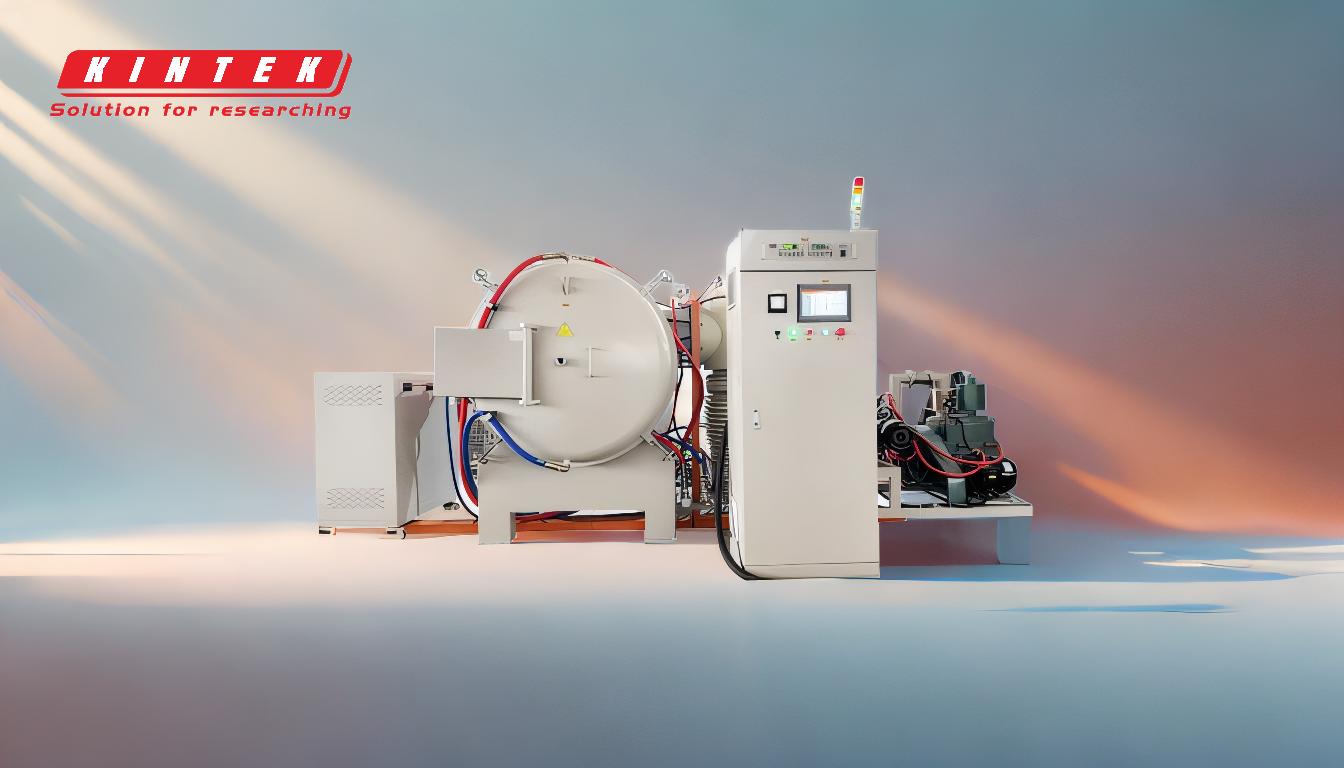
-
Aerospace Industry
- Brazing is widely used in the aerospace sector for joining critical components such as turbine blades, heat exchangers, and fuel systems.
- The process ensures high-strength joints that can withstand extreme temperatures and mechanical stresses.
- For example, brazing is used to assemble honeycomb structures in jet engines, which require lightweight yet robust materials.
-
Automotive Industry
- In automotive manufacturing, brazing is employed to join components like radiators, air conditioning systems, and exhaust systems.
- The process is ideal for creating leak-proof seals in cooling systems and ensuring durability in high-temperature environments.
- For instance, aluminum brazing is commonly used in heat exchangers and evaporators due to its excellent thermal conductivity and corrosion resistance.
-
Electronics and Electrical Industry
- Brazing is crucial in the production of electrical components, such as connectors, switches, and circuit breakers.
- The process provides strong, conductive joints that are essential for reliable electrical connections.
- For example, copper brazing is often used in power distribution systems to ensure efficient current flow and minimal energy loss.
-
HVAC (Heating, Ventilation, and Air Conditioning) Systems
- Brazing is extensively used in HVAC systems to join copper tubing and other components in refrigeration and air conditioning units.
- The process ensures leak-free connections that are vital for maintaining system efficiency and performance.
- For instance, brazing is used to assemble evaporator coils and condenser coils, which are critical for heat transfer in HVAC systems.
-
Medical Equipment
- In the medical field, brazing is used to manufacture precision instruments and devices, such as surgical tools and imaging equipment.
- The process allows for the joining of small, intricate parts with high accuracy and cleanliness.
- For example, brazing is employed in the production of MRI machines and X-ray components, where reliability and precision are paramount.
-
Industrial Machinery
- Brazing is used in the fabrication of industrial machinery, such as pumps, valves, and compressors.
- The process ensures durable joints that can withstand harsh operating conditions, including high pressure and corrosive environments.
- For instance, brazing is used to join stainless steel components in chemical processing equipment, where resistance to corrosion is essential.
-
Renewable Energy Systems
- Brazing plays a role in the assembly of components for renewable energy systems, such as solar panels and wind turbines.
- The process is used to join materials like aluminum and copper, which are commonly used in these systems.
- For example, brazing is used in the production of heat exchangers for solar thermal systems, ensuring efficient energy transfer.
-
Household Appliances
- Brazing is used in the manufacturing of household appliances, such as refrigerators, ovens, and water heaters.
- The process ensures strong, leak-proof joints that enhance the durability and performance of these appliances.
- For instance, brazing is used to join copper tubing in refrigerators, ensuring efficient cooling and long-term reliability.
By understanding these applications, it becomes clear that brazing is a critical process in modern manufacturing, offering unique advantages in terms of strength, precision, and versatility. Whether in high-tech aerospace components or everyday household appliances, brazing ensures the reliability and performance of a wide range of products.
Summary Table:
Industry | Applications |
---|---|
Aerospace | Turbine blades, heat exchangers, fuel systems, honeycomb structures in jet engines |
Automotive | Radiators, air conditioning systems, exhaust systems, heat exchangers |
Electronics & Electrical | Connectors, switches, circuit breakers, power distribution systems |
HVAC | Copper tubing, evaporator coils, condenser coils in refrigeration systems |
Medical Equipment | Surgical tools, MRI machines, X-ray components |
Industrial Machinery | Pumps, valves, compressors, chemical processing equipment |
Renewable Energy Systems | Solar panels, wind turbines, heat exchangers for solar thermal systems |
Household Appliances | Refrigerators, ovens, water heaters, copper tubing in cooling systems |
Need brazing solutions for your industry? Contact us today to learn more!