Chemical vapor deposition (CVD) is a highly advantageous technique used in various industries for depositing thin films and coatings. It offers a wide range of benefits, including the ability to deposit high-purity materials, excellent control over film properties, and the capacity to coat complex surfaces uniformly. CVD is versatile, cost-effective, and environmentally friendly, making it a preferred choice for applications requiring precise and durable coatings. Its ability to produce high-quality films with tailored properties by adjusting process parameters further enhances its appeal in advanced manufacturing and research.
Key Points Explained:
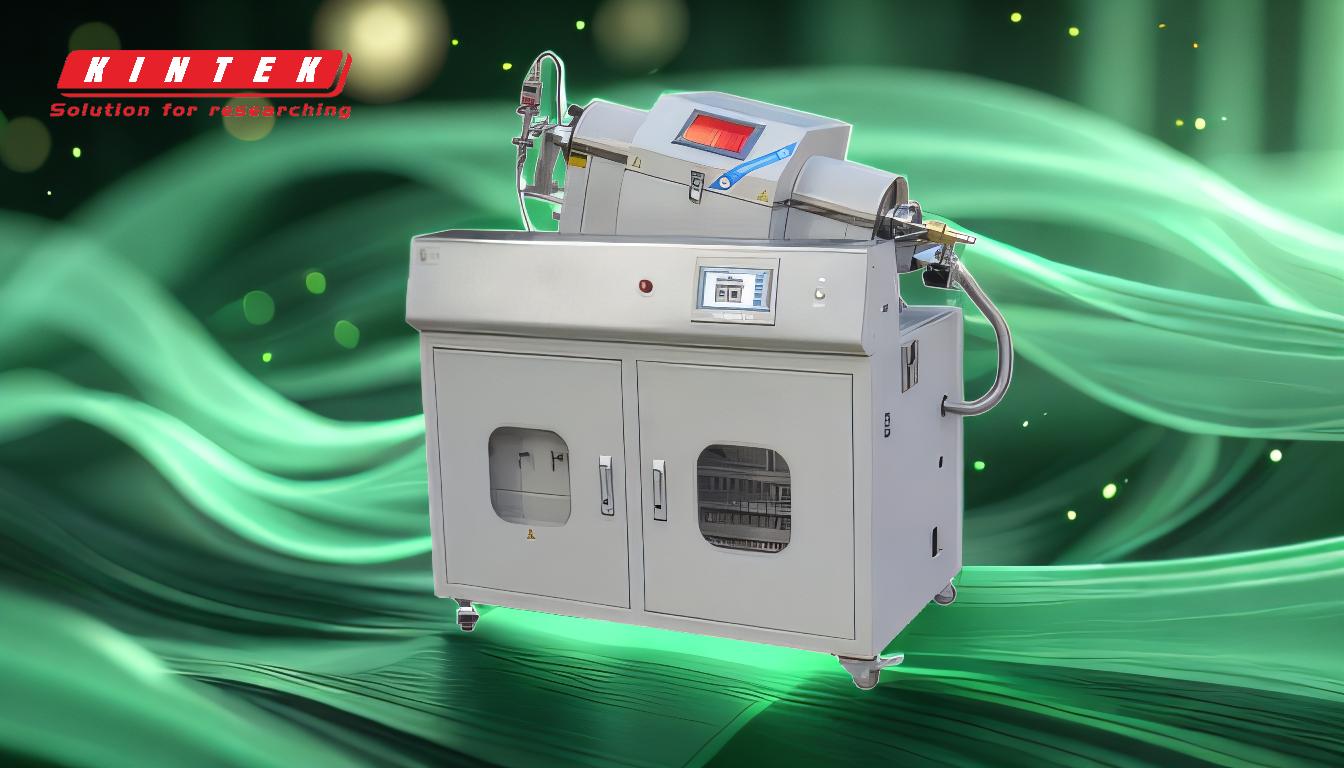
-
Versatility in Material Deposition:
- CVD can deposit a wide variety of materials, including ceramics, metals, and glass, making it suitable for diverse applications.
- It allows for the synthesis of both pure and complex materials at desired purity levels, enabling the creation of high-performance coatings.
-
Uniform and High-Quality Coatings:
- The process provides uniform coating, even on complex and precision surfaces, due to its non-line-of-sight nature.
- Films produced by CVD are dense, high-purity, and exhibit excellent adhesion, ensuring durability and reliability.
-
Control Over Film Properties:
- CVD allows precise control over the chemical and physical properties of the deposited films by adjusting parameters such as temperature, pressure, gas flow rate, and gas concentration.
- This control enables the production of films with tailored properties, such as improved electrical and thermal conductivity, corrosion resistance, and abrasion resistance.
-
High Deposition Rates and Scalability:
- CVD offers high deposition rates, making it efficient for large-scale production.
- The process is simple to scale up, ensuring high manufacturing yield and cost-effectiveness.
-
Environmental and Performance Benefits:
- CVD produces smoother surfaces and better thickness control compared to other deposition technologies, such as pitch coating.
- It has a reduced CO2 footprint, making it an environmentally friendly option for advanced manufacturing.
-
Durability in Extreme Conditions:
- Coatings produced by CVD are durable and can withstand high-stress environments, extreme temperatures, and temperature variations.
- This makes CVD ideal for applications requiring long-lasting performance under challenging conditions.
-
Ease of Operation and Maintenance:
- CVD equipment is relatively simple to operate and maintain, reducing operational costs and downtime.
- The process is versatile and adaptable, making it accessible for a wide range of industries and applications.
In summary, chemical vapor deposition stands out as a highly effective and versatile technique for producing high-quality coatings and thin films. Its ability to deliver precise control, uniform coatings, and durable performance, combined with its environmental and economic benefits, makes it a preferred choice in advanced manufacturing and research.
Summary Table:
Advantage | Description |
---|---|
Versatility in Material Deposition | Deposits ceramics, metals, and glass for diverse applications. |
Uniform and High-Quality Coatings | Provides dense, high-purity films with excellent adhesion. |
Control Over Film Properties | Adjust parameters for tailored electrical, thermal, and corrosion resistance. |
High Deposition Rates | Efficient for large-scale production with scalable processes. |
Environmental Benefits | Reduced CO2 footprint and smoother surfaces compared to other methods. |
Durability in Extreme Conditions | Withstands high stress, extreme temperatures, and temperature variations. |
Ease of Operation and Maintenance | Simple to operate and maintain, reducing costs and downtime. |
Ready to enhance your manufacturing process with CVD? Contact us today to learn more!