Heat treatment is a critical process in metallurgy and materials science, used to alter the physical and sometimes chemical properties of materials, primarily metals. The three main stages of the heat treatment process are heating, soaking, and cooling. Each stage plays a vital role in achieving the desired material properties, such as hardness, toughness, and ductility. The process involves carefully controlled heating to specific temperatures, holding the material at that temperature for a set period to allow uniform heat distribution (soaking), and then cooling it at a controlled rate. These stages are meticulously planned based on the material's composition and the intended application, ensuring the final product meets the required specifications.
Key Points Explained:
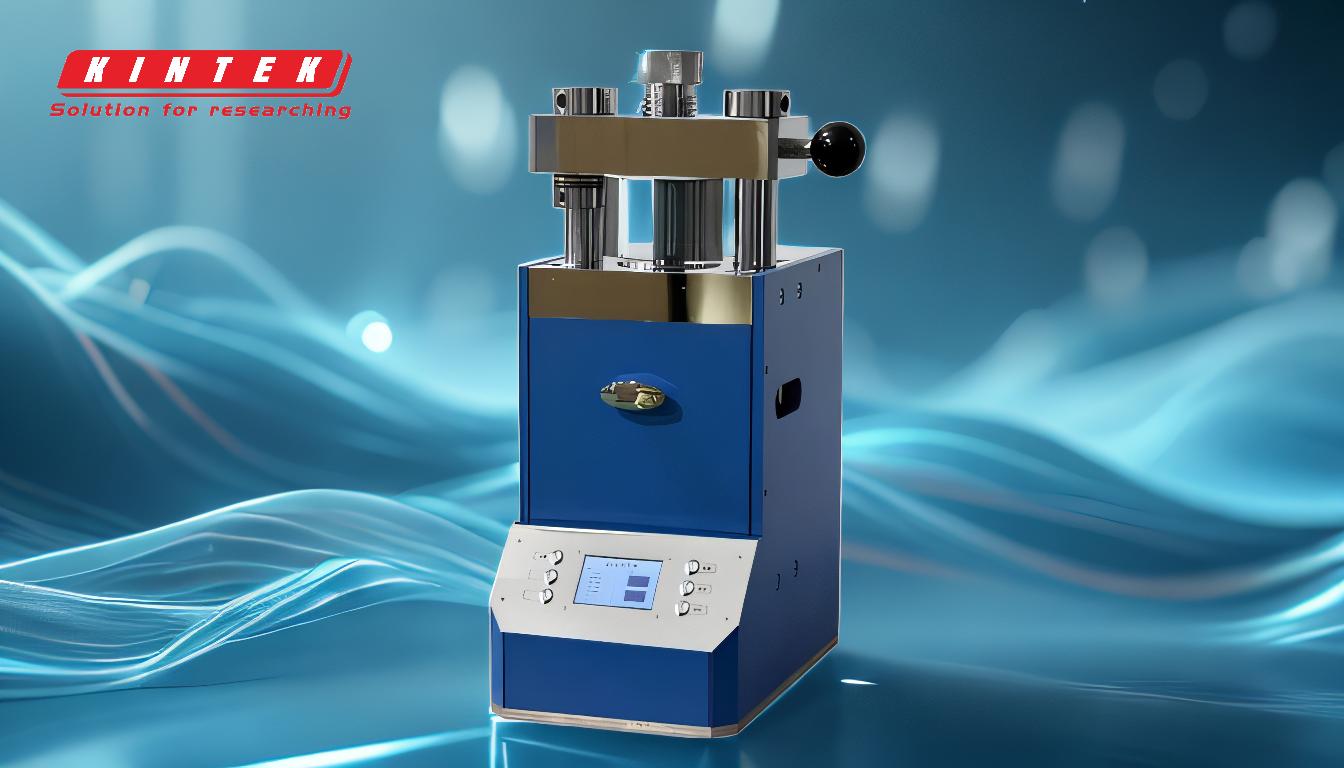
-
Heating Stage:
- Purpose: The primary goal of the heating stage is to raise the temperature of the material to a specific level where the desired structural changes can occur. This temperature varies depending on the material and the type of heat treatment being applied.
- Process: The material is heated in a controlled environment, often using furnaces, to ensure uniform temperature distribution. The rate of heating is crucial; too fast can cause thermal stresses, while too slow may not achieve the desired effect.
- Considerations: The heating rate and final temperature are determined by the material's properties, such as its thermal conductivity and the specific phase transformations required.
-
Soaking Stage:
- Purpose: Soaking, also known as holding, ensures that the entire material reaches the desired temperature uniformly. This stage allows for the necessary microstructural changes to occur throughout the material.
- Process: The material is held at the target temperature for a specific duration. The soaking time depends on the material's thickness, composition, and the desired outcome.
- Considerations: Proper soaking is essential to achieve uniform properties throughout the material. Inadequate soaking can lead to inconsistent hardness or other mechanical properties.
-
Cooling Stage:
- Purpose: Cooling is the final stage where the material is brought back to room temperature. The rate of cooling significantly affects the material's final properties.
- Process: Cooling can be done in various ways, such as air cooling, oil quenching, or water quenching. The method chosen depends on the material and the desired properties. For example, rapid cooling (quenching) can increase hardness, while slower cooling (annealing) can improve ductility.
- Considerations: The cooling rate must be carefully controlled to avoid issues like cracking or warping. Different cooling methods can lead to different microstructures, such as martensite formation in steels during rapid cooling.
Each of these stages is interdependent, and the success of the heat treatment process relies on precise control and understanding of the material's behavior at each stage. By carefully managing the heating, soaking, and cooling processes, manufacturers can tailor the mechanical properties of metals to meet specific application requirements, ensuring optimal performance and durability.
Summary Table:
Stage | Purpose | Process | Considerations |
---|---|---|---|
Heating | Raise material temperature for structural changes | Controlled heating using furnaces for uniform temperature distribution | Heating rate and final temperature depend on material properties and phase changes |
Soaking | Ensure uniform temperature for microstructural changes | Hold material at target temperature for a specific duration | Soaking time depends on material thickness, composition, and desired outcome |
Cooling | Control cooling rate to achieve desired material properties | Air, oil, or water quenching based on material and desired properties | Cooling rate must avoid cracking or warping; affects microstructure formation |
Optimize your heat treatment process with expert guidance—contact us today!