The sintering process is a widely used manufacturing technique that offers numerous advantages, such as the ability to produce complex shapes, improved mechanical properties, and cost-effectiveness. However, it also has some disadvantages, including surface roughness, porosity, and potential shrinkage during cooling. This process involves multiple stages, from powder composition to high-temperature firing, and significantly influences the material's microstructure and properties. Understanding the pros and cons of sintering is crucial for optimizing its application in various industries.
Key Points Explained:
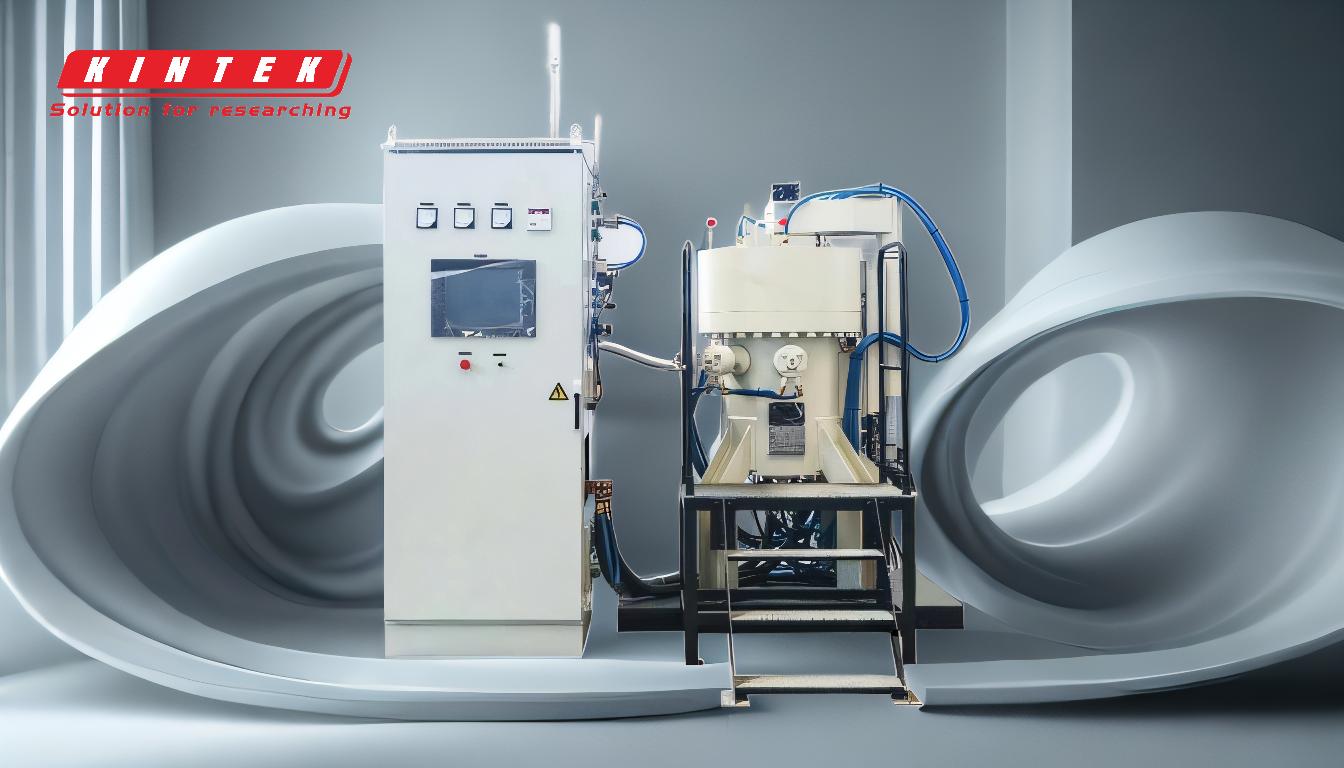
-
Advantages of Sintering:
- Complex Shapes and Intricate Designs: Sintering allows for the production of components with intricate geometries that might be difficult or impossible to achieve with other manufacturing methods. This is particularly beneficial in industries like aerospace and medical devices where complex parts are often required.
- Improved Mechanical Properties: The process enhances the strength, durability, and other mechanical properties of the material by influencing the grain size, pore size, and grain boundary distribution in the microstructure.
- Cost-Effectiveness: Sintering can be more economical than other manufacturing processes, especially for large volumes of parts. It reduces the need for additional machining and minimizes material waste.
- Versatility in Material Selection: Sintering can be applied to a wide range of materials, including metals, ceramics, and polymers, making it a versatile option for various applications.
- High Dimensional Precision: The process results in parts with high dimensional accuracy, which is crucial for components that require tight tolerances.
- Elimination of Lubricants: Sintering can eliminate the need for lubricants in the compacted powder, reducing surface oxygen and improving the part's properties.
-
Disadvantages of Sintering:
- Surface Roughness and Porosity: One of the main drawbacks of sintering is the rough and porous surface finish of the final product. This can be a limitation for applications requiring smooth surfaces.
- Shrinkage During Cooling: The post-processing cooling phase can lead to shrinkage, which may affect the dimensional accuracy and overall quality of the part.
- Micro-Porosity: Even though sintering reduces porosity, some micro-porosity may still remain, which can impact the material's strength and durability.
- High-Temperature Requirements: The process requires very high temperatures, which can be energy-intensive and may limit the types of materials that can be sintered.
-
Stages of the Sintering Process:
- Composing the Sintering Powder: The first stage involves preparing the powder mixture, which may include various elements like nickel, copper, and graphite to enhance the material's properties.
- Packing and Pressing: The powder is then packed and pressed into the desired shape. This green body is fragile and requires careful handling.
- Heating in a Sintering Furnace: The green body is placed in a sintering furnace and fired at high temperatures. This stage increases the density and strength of the part while reducing its porosity and volume.
-
Influence on Material Properties:
- Grain Size and Pore Size: The sintering process directly affects the grain size and pore size, which in turn influence the material's strength and durability.
- Grain Boundary Shape and Distribution: The shape and distribution of grain boundaries are also altered during sintering, impacting the overall mechanical properties of the material.
-
Applications and Productivity:
- Complex Shapes and Reduced Machining: The high level of control in the sintering process allows for the creation of complex shapes, reducing the need for further machining and thus increasing productivity.
- Faster Startups and Fewer Interruptions: The process results in fewer interruptions and faster startups, which can significantly enhance production efficiency.
In summary, the sintering process offers numerous benefits, including the ability to produce complex and high-precision parts with improved mechanical properties. However, it also has some limitations, such as surface roughness, porosity, and potential shrinkage. Understanding these advantages and disadvantages is essential for effectively utilizing sintering in various industrial applications.
Summary Table:
Aspect | Advantages | Disadvantages |
---|---|---|
Complex Shapes | Produces intricate geometries, ideal for aerospace and medical industries | Rough and porous surface finish |
Mechanical Properties | Enhances strength, durability, and grain structure | Potential shrinkage during cooling |
Cost-Effectiveness | Economical for large volumes, reduces machining and material waste | High-temperature requirements, energy-intensive |
Material Versatility | Works with metals, ceramics, and polymers | Micro-porosity may remain, affecting strength |
Dimensional Precision | High accuracy for tight-tolerance components | - |
Lubricant Elimination | Reduces surface oxygen, improving part properties | - |
Discover how sintering can optimize your manufacturing process—contact our experts today for tailored solutions!