Field-assisted sintering (FAST/SPS) offers significant advantages over traditional sintering methods, particularly in terms of processing efficiency, material properties, and cost-effectiveness. This advanced technique leverages electrical currents and mechanical pressure to achieve rapid densification of materials at lower temperatures and shorter times compared to conventional sintering. The benefits include enhanced control over microstructure, improved mechanical and thermal properties, and the ability to process difficult materials. Below, we explore the key advantages of field-assisted sintering in detail.
Key Points Explained:
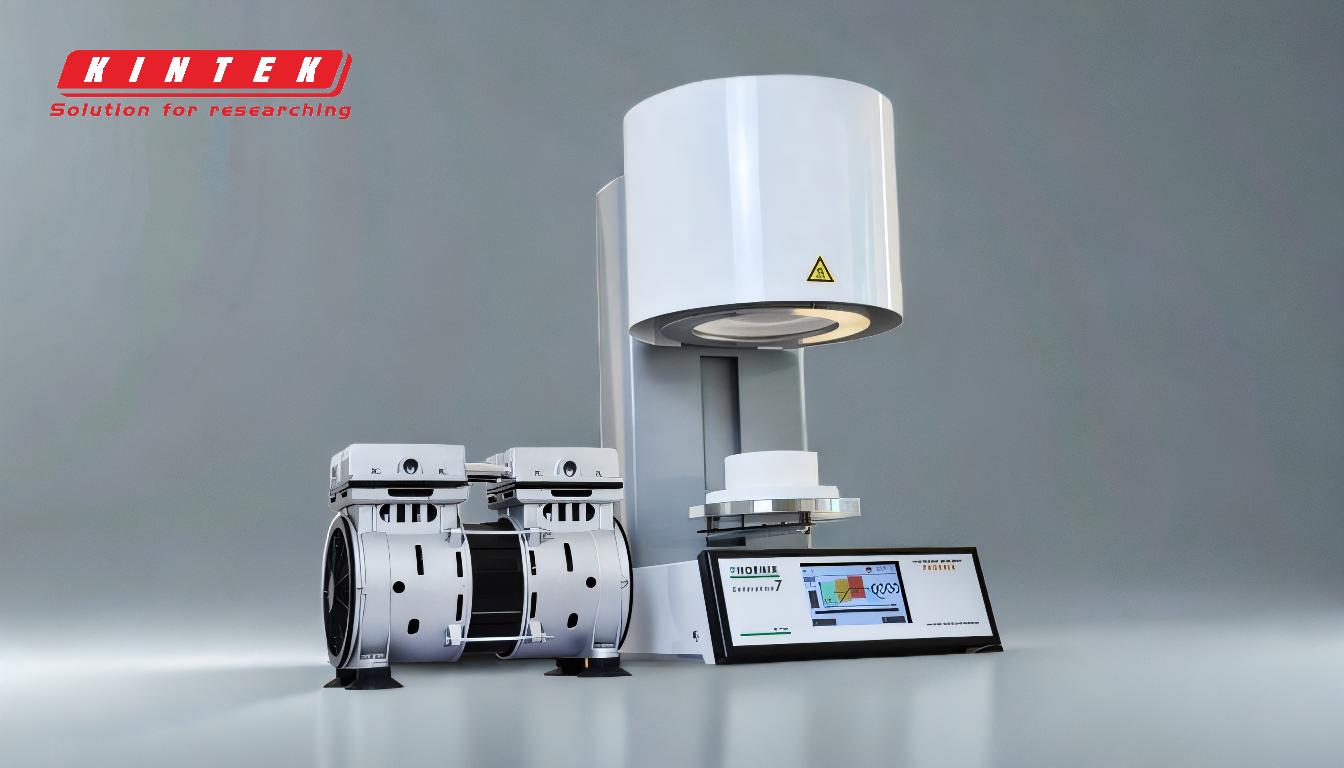
-
Lower Processing Temperatures and Shorter Times
- FAST/SPS significantly reduces the required sintering temperature and time, enabling faster production cycles and energy savings.
- This is particularly beneficial for materials with high melting points, such as refractory metals and ceramics, which are challenging to process using conventional methods.
- The reduced thermal exposure minimizes grain growth, preserving fine-grained microstructures that enhance material strength and durability.
-
Enhanced Control Over Microstructure
- Field-assisted sintering allows precise control over the densification process, resulting in uniform and fine-grained microstructures.
- This level of control improves material properties such as strength, hardness, and wear resistance, making it ideal for high-performance applications like turbine blades and cutting tools.
- The technique also enables the creation of non-equilibrium microstructures, which can exhibit unique properties not achievable through traditional sintering.
-
Improved Mechanical and Thermal Properties
- FAST/SPS produces materials with superior mechanical properties, including higher strength, toughness, and fatigue resistance.
- The process enhances thermal and electrical conductivity by reducing porosity and improving particle bonding, making it suitable for applications in electronics and thermal management.
- The uniform densification achieved through FAST/SPS ensures consistent material performance across large-scale production batches.
-
Energy Efficiency and Environmental Friendliness
- The reduced processing temperatures and shorter sintering times translate to lower energy consumption, making FAST/SPS a more sustainable option.
- The process minimizes oxidation and contamination, improving product quality and reducing the need for post-processing treatments.
- These environmental benefits align with the growing demand for eco-friendly manufacturing practices.
-
Versatility in Material Processing
- FAST/SPS is capable of processing a wide range of materials, including metals, ceramics, composites, and nanomaterials.
- It is particularly effective for difficult-to-sinter materials, such as those with high melting points or low diffusion rates.
- The technique can also be used to create complex, near-net-shape components, reducing material waste and machining costs.
-
Cost-Effectiveness and Simplicity
- The use of simple equipment and lower energy requirements makes FAST/SPS a cost-effective alternative to traditional sintering methods.
- The ability to achieve high-quality results with minimal processing steps reduces overall production costs.
- The technique's scalability makes it suitable for both small-scale research and large-scale industrial applications.
-
Applications in High-Performance Industries
- FAST/SPS is widely used in industries requiring high-performance materials, such as aerospace, automotive, electronics, and biomedical engineering.
- Examples include the production of turbine blades, cutting tools, heat sinks, and medical implants, where superior material properties are critical.
- The technique's ability to produce materials with tailored properties opens up new possibilities for advanced material design and innovation.
In summary, field-assisted sintering (FAST/SPS) offers a compelling combination of efficiency, precision, and versatility, making it a superior choice for modern material processing. Its ability to produce high-quality materials with enhanced properties at lower costs and environmental impact positions it as a key technology in the advancement of materials science and manufacturing.
Summary Table:
Advantage | Key Benefits |
---|---|
Lower Processing Temperatures & Times | Faster production, energy savings, minimized grain growth |
Enhanced Microstructure Control | Uniform, fine-grained structures; improved strength, hardness, and wear resistance |
Improved Mechanical & Thermal Properties | Higher strength, toughness, and thermal/electrical conductivity |
Energy Efficiency & Sustainability | Lower energy consumption, reduced oxidation, and contamination |
Versatility in Material Processing | Processes metals, ceramics, composites, and nanomaterials effectively |
Cost-Effectiveness & Simplicity | Lower equipment and energy costs, scalable for research and industrial use |
High-Performance Applications | Aerospace, automotive, electronics, and biomedical engineering |
Ready to enhance your material processing with FAST/SPS? Contact us today to learn more!