Low Pressure Chemical Vapor Deposition (LPCVD) offers several advantages over conventional CVD and other deposition techniques. These include improved film uniformity, enhanced conformability, and the ability to operate at lower temperatures, which is particularly beneficial when working with temperature-sensitive materials. LPCVD also reduces unwanted gas-phase reactions, leading to higher-quality films. Additionally, it provides excellent trench coverage filling capability and can produce a wide range of materials, from silicon-based films to advanced materials like graphene and carbon nanotubes. These benefits make LPCVD a versatile and efficient method for thin-film deposition in various industrial applications.
Key Points Explained:
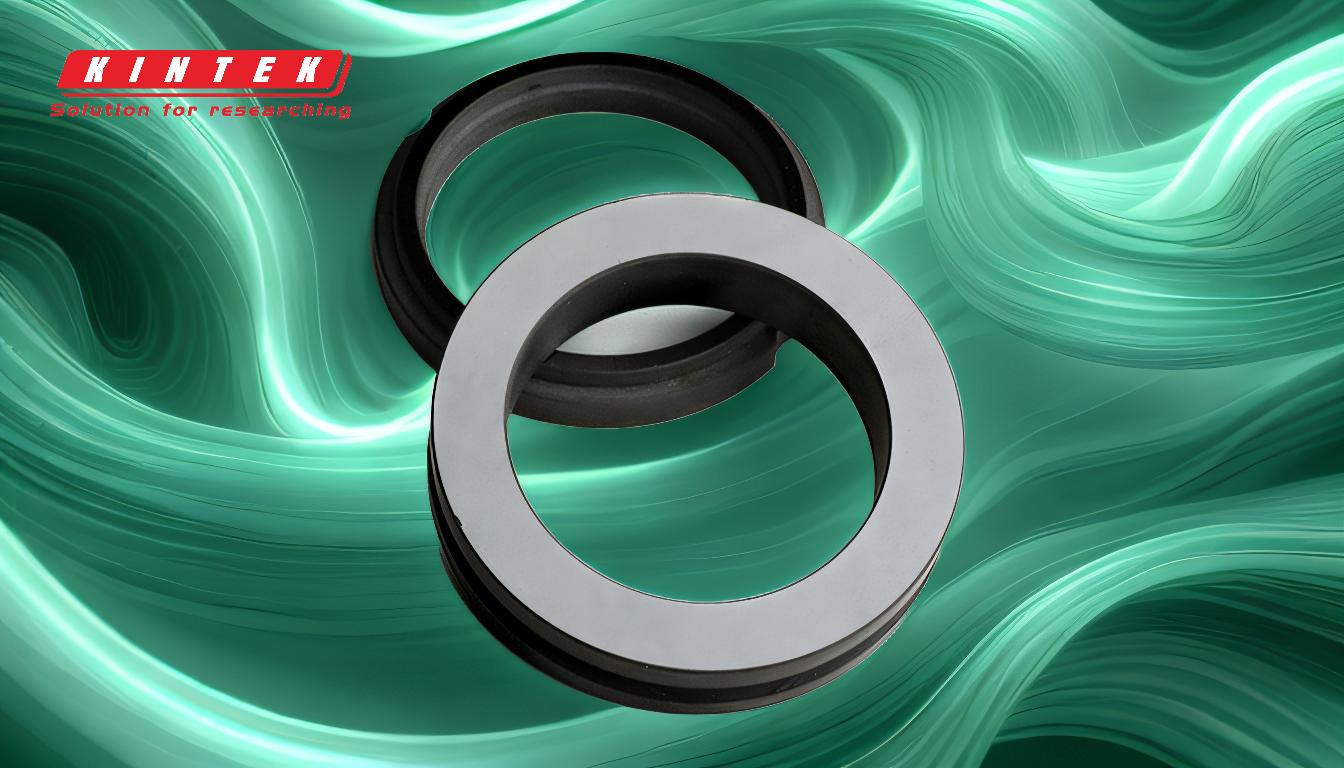
-
Improved Film Uniformity and Quality:
- LPCVD operates at lower pressures, which minimizes unwanted gas-phase reactions. This results in films with higher uniformity and better quality compared to conventional CVD.
- The process ensures consistent thickness and composition across the substrate, which is critical for applications requiring precise material properties.
-
Enhanced Conformability and Trench Coverage:
- LPCVD excels in conformal coating, meaning it can uniformly cover complex geometries, including deep trenches and high-aspect-ratio structures.
- This capability is essential for semiconductor manufacturing, where uniform coverage is required for devices like transistors and interconnects.
-
Lower Operating Temperatures:
- LPCVD can occur at lower temperatures than traditional CVD, making it suitable for depositing films on temperature-sensitive materials, such as aluminum.
- The temperature can be further reduced by incorporating energy sources like plasma, enabling the deposition of materials that would otherwise degrade at higher temperatures.
-
Versatility in Material Deposition:
- LPCVD is capable of depositing a wide range of materials, including silicon dioxide, silicon nitride, polycrystalline silicon, and advanced materials like graphene and carbon nanotubes.
- This versatility makes LPCVD a preferred method for applications in microelectronics, optoelectronics, and nanotechnology.
-
Reduced Gas-Phase Reactions:
- The lower pressure in LPCVD reduces the likelihood of gas-phase reactions, which can lead to impurities and defects in the film.
- This results in films with higher purity and better performance in electronic and optical applications.
-
Scalability and Control:
- LPCVD is highly scalable, with deposition rates easily controlled by adjusting the flow rate of precursor gases.
- This makes it suitable for large-scale manufacturing, where consistent and reproducible results are essential.
-
Economic and Operational Advantages:
- LPCVD offers economic benefits due to its ability to synthesize thick coatings efficiently.
- The process allows for flexibility, such as codeposition of different materials and the inclusion of plasma or initiators to enhance reactivity and deposition quality.
-
Non-Line-of-Sight Deposition:
- Unlike physical vapor deposition (PVD), LPCVD is a non-line-of-sight process, meaning it can coat nonuniform and complex surfaces with ease.
- This capability is particularly advantageous for coating intricate components in industries like aerospace and automotive.
By leveraging these advantages, LPCVD has become a cornerstone technology in the fabrication of high-performance thin films and advanced materials, meeting the demanding requirements of modern industrial applications.
Summary Table:
Advantage | Description |
---|---|
Improved Film Uniformity & Quality | Ensures consistent thickness and composition, minimizing gas-phase reactions. |
Enhanced Conformability & Trench Coverage | Uniformly coats complex geometries, ideal for semiconductor manufacturing. |
Lower Operating Temperatures | Suitable for temperature-sensitive materials, with optional plasma assistance. |
Versatility in Material Deposition | Deposits silicon-based films, graphene, carbon nanotubes, and more. |
Reduced Gas-Phase Reactions | Produces high-purity films with fewer impurities and defects. |
Scalability & Control | Adjustable deposition rates for large-scale, reproducible manufacturing. |
Economic & Operational Advantages | Efficient synthesis of thick coatings with flexible codeposition options. |
Non-Line-of-Sight Deposition | Coats nonuniform and complex surfaces, ideal for aerospace and automotive. |
Unlock the potential of LPCVD for your applications—contact our experts today!