Press forging and drop forging are two common metal forming processes, each with distinct advantages and applications. Press forging involves the gradual application of pressure to shape metal, while drop forging uses a hammer to deliver rapid, high-impact blows. The choice between these methods depends on factors such as material type, desired precision, production volume, and cost considerations. Press forging is often preferred for its ability to produce complex shapes with high dimensional accuracy and superior surface finish, while drop forging is better suited for simpler shapes and high-volume production. Below, we explore the key advantages of press forging over drop forging in detail.
Key Points Explained:
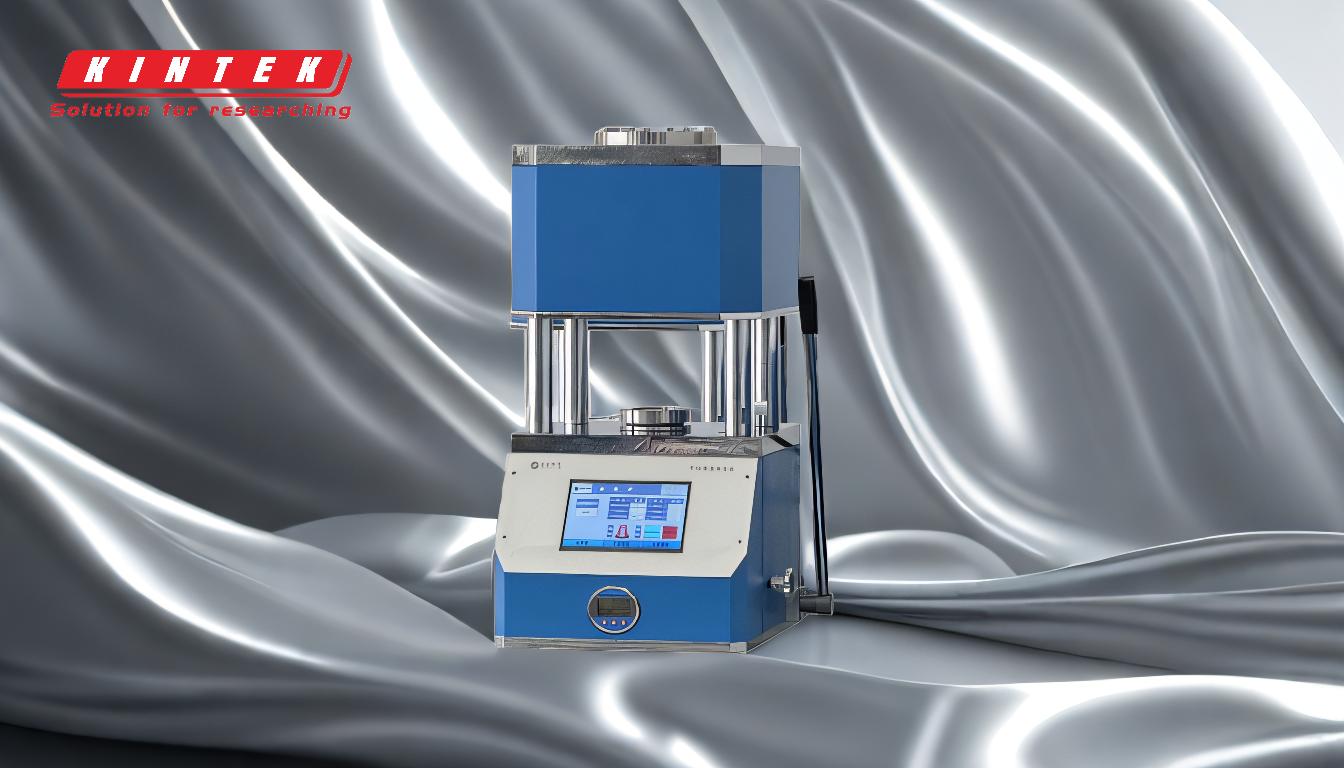
-
Precision and Dimensional Accuracy
- Press forging applies continuous pressure, allowing for precise control over the deformation of the metal. This results in parts with tighter tolerances and better dimensional accuracy compared to drop forging, which relies on high-impact blows that can cause slight variations in shape and size.
- The gradual pressure in press forging ensures uniform deformation, reducing the likelihood of defects such as cracks or voids.
-
Surface Finish
- The controlled and steady pressure in press forging produces a smoother surface finish, reducing the need for additional machining or finishing processes.
- In contrast, drop forging can leave marks or imperfections on the surface due to the rapid and forceful nature of the process.
-
Complex Geometries
- Press forging is better suited for creating intricate and complex shapes because the continuous pressure allows for more detailed die impressions.
- Drop forging, while effective for simpler shapes, may struggle to achieve the same level of detail due to the limitations of high-impact deformation.
-
Material Utilization
- Press forging minimizes material waste by ensuring consistent and controlled deformation. This is particularly beneficial when working with expensive or high-performance alloys.
- Drop forging can result in higher material loss due to flash (excess material that escapes from the die cavity) and less precise shaping.
-
Mechanical Properties
- The gradual application of pressure in press forging enhances the mechanical properties of the forged part, such as strength and fatigue resistance, by promoting uniform grain flow.
- While drop forging also improves mechanical properties, the rapid deformation can sometimes lead to uneven grain structures, particularly in thicker sections.
-
Tool and Die Life
- Press forging tends to be gentler on dies and tooling because the process involves steady pressure rather than repeated impacts. This results in longer tool life and reduced maintenance costs.
- Drop forging, with its high-impact nature, can cause more wear and tear on dies, requiring frequent replacements or repairs.
-
Noise and Vibration
- Press forging operates more quietly and with less vibration compared to drop forging, which can be noisy and disruptive in a manufacturing environment.
- This makes press forging a more operator-friendly process, especially in settings where noise reduction is a priority.
-
Production Flexibility
- Press forging is adaptable to a wide range of materials, including those that are more brittle or difficult to shape, such as titanium or nickel-based alloys.
- Drop forging is generally limited to more ductile materials that can withstand the high-impact forces.
-
Cost Considerations
- While press forging may have higher initial setup costs due to the need for precision dies and equipment, it can be more cost-effective in the long run for producing high-quality, complex parts with minimal waste.
- Drop forging is often more economical for high-volume production of simpler parts but may incur additional costs for secondary machining or finishing.
In summary, press forging offers significant advantages over drop forging in terms of precision, surface finish, material utilization, and the ability to produce complex geometries. However, the choice between the two methods ultimately depends on the specific requirements of the application, including material type, production volume, and budget constraints.
Summary Table:
Advantage | Press Forging | Drop Forging |
---|---|---|
Precision & Accuracy | High dimensional accuracy with tight tolerances | Slight variations due to high-impact blows |
Surface Finish | Smooth surface, minimal need for secondary finishing | Marks or imperfections due to rapid deformation |
Complex Geometries | Ideal for intricate and detailed shapes | Limited to simpler shapes |
Material Utilization | Minimizes waste, especially with expensive alloys | Higher material loss due to flash |
Mechanical Properties | Uniform grain flow enhances strength and fatigue resistance | Uneven grain structures in thicker sections |
Tool & Die Life | Longer tool life, reduced maintenance | Higher wear and tear, frequent replacements |
Noise & Vibration | Quieter operation with minimal vibration | Noisy and disruptive |
Production Flexibility | Adaptable to brittle or difficult-to-shape materials | Limited to ductile materials |
Cost Considerations | Higher initial setup but cost-effective for complex parts | Economical for high-volume, simpler parts |
Ready to optimize your metal forming process? Contact us today to learn how press forging can benefit your production needs!