Pressing and sintering are widely used in manufacturing to produce high-quality, durable components with complex shapes and tailored material properties. The process involves compacting powdered materials under pressure and then heating them in a sintering furnace to fuse the particles, resulting in improved strength, reduced porosity, and enhanced mechanical properties. This method is cost-effective, versatile, and suitable for a wide range of industries, including aerospace, defense, electronics, and dental laboratories. By controlling parameters like temperature, pressure, and atmosphere, manufacturers can achieve consistent geometries, superior quality, and reduced defects in the final products.
Key Points Explained:
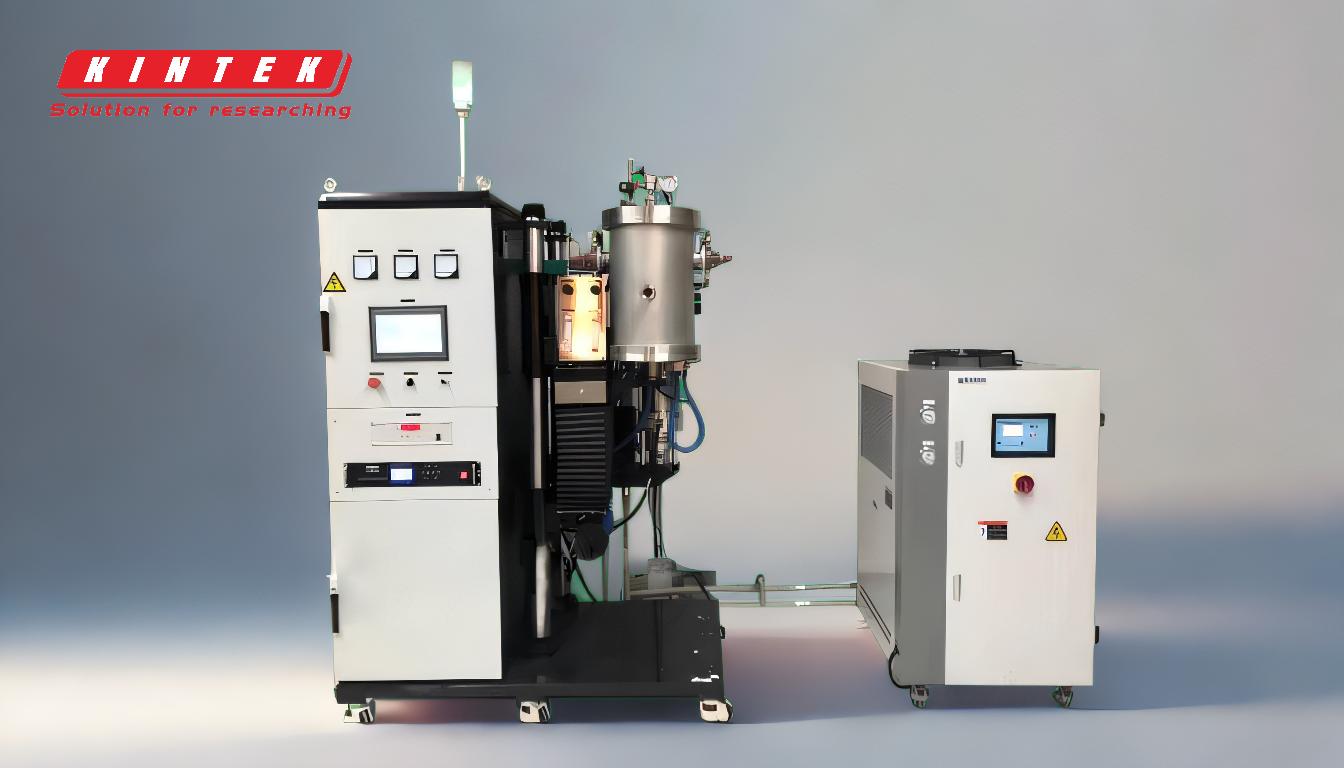
-
Improved Mechanical Properties:
- Pressing and sintering enhance the strength and durability of materials by developing sintered necks between particles, reducing pores, and increasing density.
- The diffusion of elements like nickel, copper, and graphite during sintering further improves the material's properties, making it suitable for high-performance applications.
-
Complex Shapes and Intricate Designs:
- The process allows for the production of components with complex geometries and intricate designs, which are difficult to achieve with traditional manufacturing methods.
- This is particularly beneficial in industries like aerospace and electronics, where precision and intricate designs are critical.
-
Tailored Material Compositions:
- By controlling the sintering parameters, manufacturers can tailor the material composition to meet specific requirements, such as enhanced wear resistance or thermal conductivity.
- This flexibility in material selection makes sintering suitable for a wide range of applications, from super alloys in aerospace to zirconia in dental laboratories.
-
Cost-Effectiveness:
- Sintering reduces manufacturing costs by minimizing material waste and eliminating the need for additional machining or finishing processes.
- The ability to produce consistent geometries in large quantities further enhances productivity and reduces expenses.
-
Versatility in Material Selection:
- The process is compatible with a wide range of materials, including metals, ceramics, and composites, making it a versatile solution for various industries.
- For example, zirconia sintering furnaces are used in dental laboratories to produce high-quality dental prosthetics with precise properties.
-
Superior Quality and Fewer Defects:
- Vacuum sintering furnaces produce clean, bright parts with fewer defects, ensuring superior quality and reliability.
- The high-precision controllers in modern sintering furnaces allow for precise temperature adjustments, resulting in consistent and high-quality end products.
-
Efficiency and Productivity:
- Sinter-HIP furnaces combine vacuum environments with high pressure, saving time and costs while producing components with consistent geometries.
- This efficiency boosts productivity and makes the process suitable for high-volume manufacturing.
-
Environmental and Maintenance Benefits:
- The sintering process eliminates the need for lubricants, reducing environmental impact and simplifying maintenance.
- Vacuum sintering furnaces are designed for easy maintenance, ensuring maximum productivity and minimal downtime.
By leveraging the advantages of pressing and sintering, manufacturers can achieve high-quality, durable components with tailored properties, making it a preferred method for a wide range of industrial applications.
Summary Table:
Advantage | Description |
---|---|
Improved Mechanical Properties | Enhances strength, durability, and reduces porosity through sintered particle fusion. |
Complex Shapes & Designs | Enables production of intricate geometries, ideal for aerospace and electronics. |
Tailored Material Compositions | Customizes material properties like wear resistance and thermal conductivity. |
Cost-Effectiveness | Reduces material waste and eliminates additional machining or finishing steps. |
Versatility in Material Selection | Compatible with metals, ceramics, and composites for diverse applications. |
Superior Quality & Fewer Defects | Produces clean, bright parts with precise temperature control for consistency. |
Efficiency & Productivity | High-volume production with consistent geometries, saving time and costs. |
Environmental & Maintenance Benefits | Eliminates lubricants, reduces environmental impact, and simplifies maintenance. |
Unlock the potential of pressing and sintering for your manufacturing needs—contact our experts today!