The Physical Vapor Deposition (PVD) process offers numerous benefits, making it a preferred choice for various industrial applications. PVD is known for its ability to produce durable, high-quality coatings that enhance the performance and longevity of materials. These coatings are highly resistant to wear, corrosion, and high temperatures, making them suitable for demanding environments. Additionally, PVD allows for precise control over the coating thickness and composition, enabling the creation of ultra-thin, uniform layers. This precision is particularly valuable in industries such as electronics, where thin films are essential for the production of integrated circuits and semiconductors. Furthermore, PVD is an environmentally friendly process, as it typically involves fewer hazardous chemicals compared to other coating methods. The process is also versatile, capable of coating a wide range of materials, including metals, ceramics, and polymers, which makes it applicable in various fields, from aerospace to medical devices.
Key Points Explained:
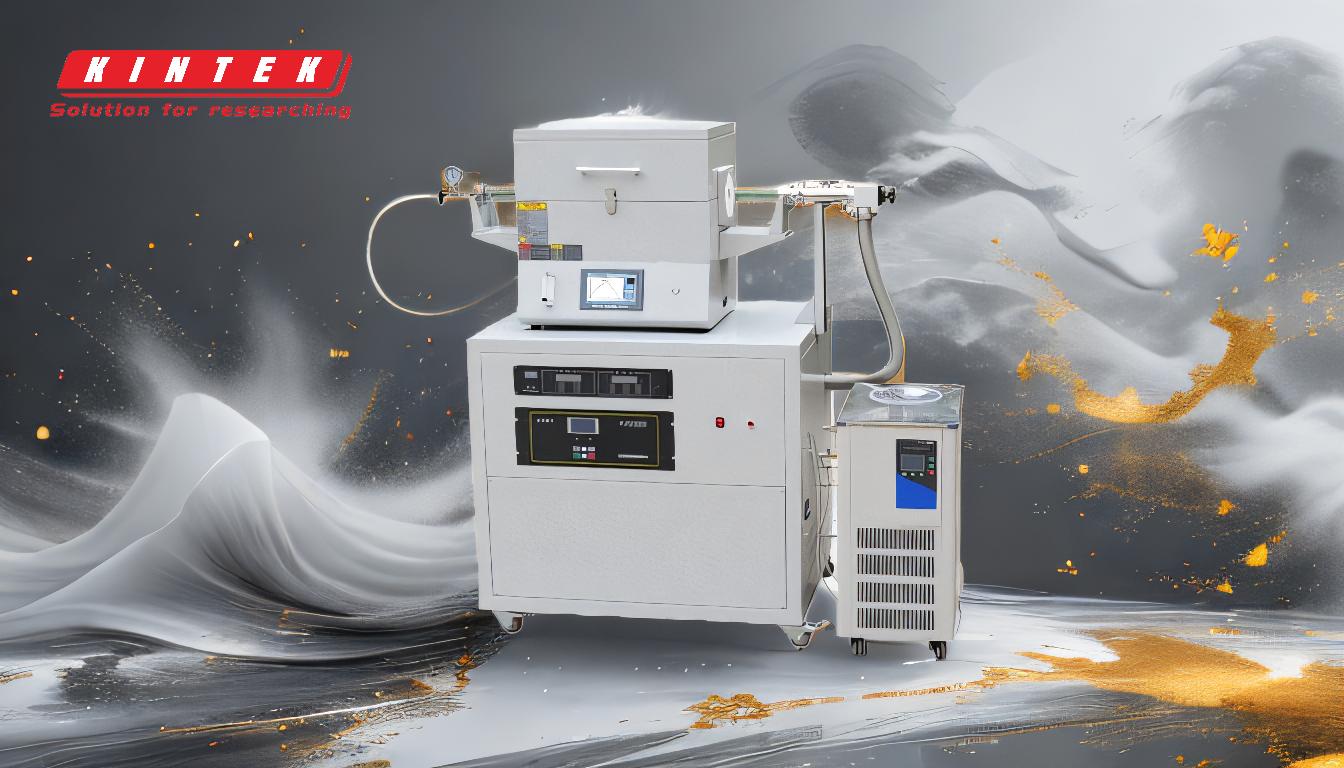
-
Durable and High-Quality Coatings:
- PVD coatings are known for their exceptional durability and quality. These coatings are highly resistant to wear, corrosion, and high temperatures, making them ideal for use in harsh environments. For example, PVD coatings are commonly used in the aerospace industry to protect components from extreme conditions, such as high temperatures and corrosive atmospheres.
-
Precision and Control:
- One of the significant advantages of PVD is the ability to precisely control the thickness and composition of the coatings. This precision allows for the creation of ultra-thin, uniform layers, which are crucial in the production of electronic components like integrated circuits and semiconductors. The ability to control the coating process also ensures consistent quality and performance across different batches.
-
Environmental Friendliness:
- PVD is considered an environmentally friendly coating process. Unlike some other coating methods, PVD typically involves fewer hazardous chemicals and produces minimal waste. This makes it a more sustainable option for industries looking to reduce their environmental impact. The process also consumes less energy compared to traditional coating methods, further contributing to its eco-friendliness.
-
Versatility:
- The PVD process is highly versatile and can be used to coat a wide range of materials, including metals, ceramics, and polymers. This versatility makes PVD applicable in various industries, from aerospace and automotive to medical devices and consumer electronics. For instance, PVD coatings are used in medical devices to enhance biocompatibility and reduce wear, while in consumer electronics, they improve the durability and aesthetic appeal of products.
-
Enhanced Performance in Electronics:
- In the electronics industry, PVD is particularly valuable for the production of thin films used in integrated circuits, semiconductors, capacitors, and resistors. The ability to create ultra-thin layers of material with precise control over their properties enhances the performance and reliability of electronic devices. This leads to an extended product lifecycle and improved functionality, as seen in the application of microwave plasma chemical vapor deposition for coating electronic components.
-
Lower Temperature Deposition:
- The use of plasma in PVD processes, such as microwave plasma chemical vapor deposition, allows for the deposition of coatings at lower temperatures. This is particularly beneficial for heat-sensitive substrates, as it reduces the risk of thermal damage. Lower temperature deposition also expands the range of possible substrates and coating materials, making PVD a more flexible option for various applications.
In summary, the PVD process offers a combination of durability, precision, environmental friendliness, and versatility, making it an essential technique in modern manufacturing and technology. Its ability to produce high-quality coatings with precise control over their properties ensures that it remains a preferred choice across a wide range of industries.
Summary Table:
Key Benefit | Description |
---|---|
Durable and High-Quality Coatings | Resistant to wear, corrosion, and high temperatures; ideal for harsh environments. |
Precision and Control | Ultra-thin, uniform layers with precise thickness and composition control. |
Environmental Friendliness | Fewer hazardous chemicals, minimal waste, and lower energy consumption. |
Versatility | Applicable to metals, ceramics, polymers; used in aerospace, medical, and more. |
Enhanced Performance in Electronics | Thin films for integrated circuits, semiconductors, capacitors, and resistors. |
Lower Temperature Deposition | Suitable for heat-sensitive substrates, reducing thermal damage risks. |
Unlock the potential of PVD coatings for your industry—contact us today to learn more!